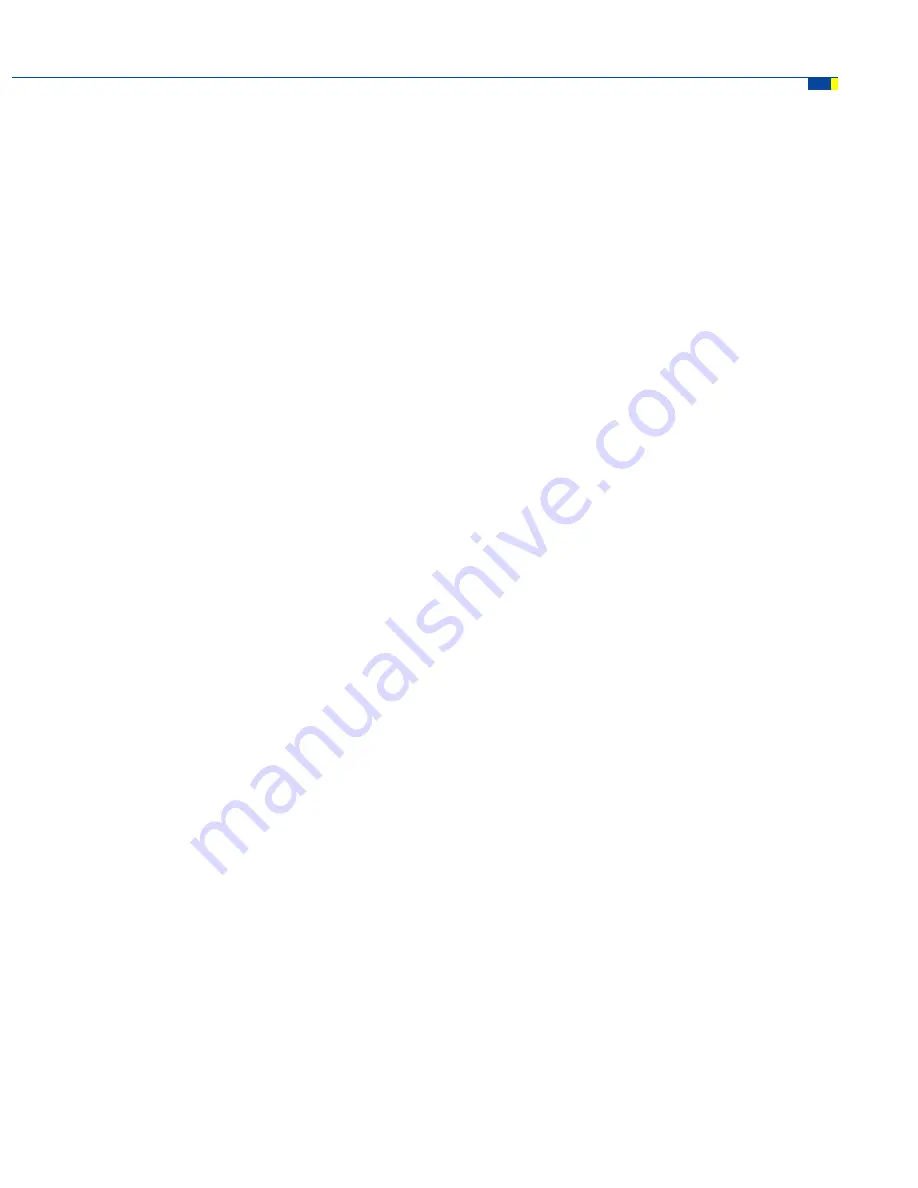
M4RTU/M4 I/O User’s Guide
11
Available Options
The M4RTU/M4 I/O accommodates eight digital and four analog G4 I/O modules. For applications requiring
additional I/O modules, the Modular Controller product line includes a Modular Controller I/O Extender, called
the M4RTUX, which connects to the M4RTU/M4 I/O base unit using an Opto 22 shielded 25-pin M4RTUXCAB
cable. The M4RTUX provides an additional eight digital and four analog I/O channels. With the M4RTUX option
connected to the M4RTU/M4 I/O base unit, up to 24 G4 I/O modules can be installed. Additional I/O can be
connected via an RS-485 serial link.
To accommodate a wide variety of applications, seven power supplies are available for the M4RTU/M4 I/O:
four wide-input-range DC (12V, 24V, 48V, 125V), two wide-input-range AC (120V, 220V), and one line filter base
for connecting user-supplied power supplies. These fuse-protected power supplies feature input-to-output
isolation protection, a built-in EMI filter, and an on/off switch. They supply enough power to operate the M4RTU/
M4 I/O base unit, three M4BUS expansion options, and I/O modules for both the base unit and the Modular M4
Controller I/O Extender. They can also supply the current loop for analog current modules.
The M4BUS technology provides a variety of communication interface cards. M4RTU/M4 I/O options include
Ethernet interface cards (M4SENETU and M4SENETC), an ARCNET
®
interface card (M4SARC), a serial (RS-232
and RS-422/RS-485) interface card (M4SSER), a fiber optic ARCNET
®
card (M4SARCF) and a fiber optic ARCNET
®
repeater card (M4SARCFR). These open options allow customers to share real-time data with telemetry-based
SCADA systems or network-based control and information systems. The available serial ports communicate at
up to 115 K baud. These ports can be used to support additional I/O units, perform host communications,
interface to a modem or transmit data to and from third-party devices. The Ethernet and ARCNET options
enable you to connect the M4RTU/M4 I/O to other major system components using plantwide information
networks. All modular interface cards for serial communications or network connectivity are supported as
standard selections in the FactoryFloor software.
Software
M4RTU/M4 I/O configuration and program development are performed on a PC workstation through OptoControl,
Opto 22’s PC-based graphical, flowchart language. OptoControl is easy to learn, easy to use, and is designed to
harness all the power of Opto 22’s distributed, control hardware platform. One of the fundamental advantages
of OptoControl is its usability. Six months after you write an OptoControl program, you can come back to it and
understand it. Four key features of OptoControl are:
•
OptoControl’s flowchart programming environment, which provides a precise, graphical view of your
control process.
•
OptoControl’s “Strategy Tree,” which provides a graphical tree-like view of your control system
configuration.
•
OptoControl’s animated debugger, which makes it easy to step through your process and see what’s
happening at every point in your control program.
•
OptoControl flowcharts, which can be packaged as subroutines to provide extensive code reusability.
INTRODUCTION
Summary of Contents for Modular M4RTU
Page 6: ...6 M4RTU M4 I O User s Guide TABLE OF CONTENTS...
Page 74: ...74 M4RTU M4 I O User s Guide FIELD WIRING...
Page 80: ...80 M4RTU M4 I O User s Guide PRODUCT SPECIFICATIONS...
Page 82: ...82 M4RTU M4 I O User s Guide ADDRESS JUMPER CONFIGURATION...
Page 86: ...86 M4RTU M4 I O User s Guide UPGRADING RAM AND FLASH EEPROM...
Page 89: ...M4RTU M4 I O User s Guide 89 WORKSHEETS Figure F 3 M4RTUX I O Extender I O Module Worksheet...
Page 91: ...M4RTU M4 I O User s Guide 91 WORKSHEETS Figure F 5 Field Wiring Worksheet Example 2...
Page 94: ...94 M4RTU M4 I O User s Guide WORKSHEETS...