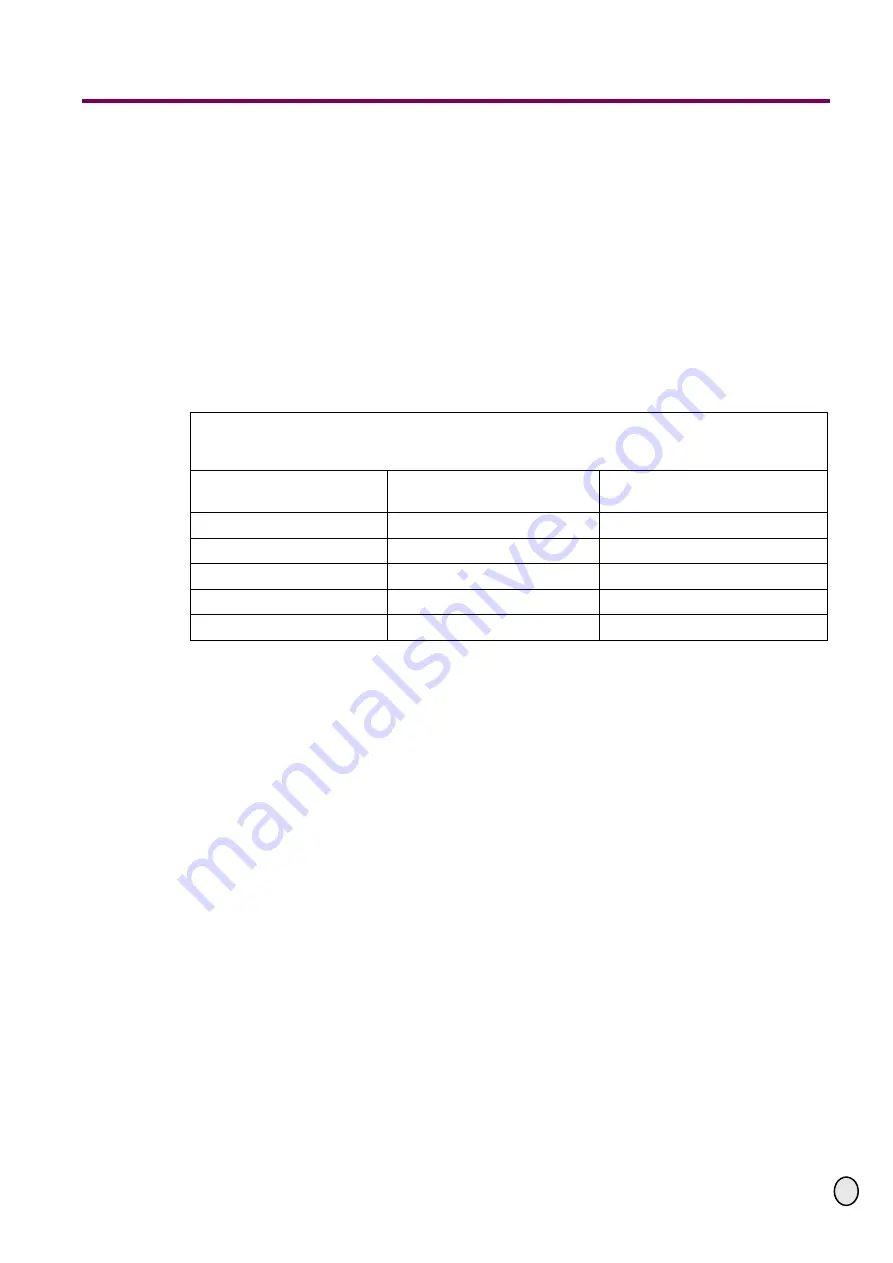
Assembly and maintenance instruction ball bearing spindle
OPTIMUM
M A S C H I N E N - G E R M A N Y
03 / 08 / 2006
Page 25
Ball bearing spindle assembly and maintenance instruction ; Version 1.4.7
©
20
06
D
5.2
Installation with spindle
The ball bearing spindle needs to be installed radial and without tension: When you tighten the
bearing, the slide needs to be moved on the corresponding side to and fro.
5.3
Lubricating notes
Before commissioning, imperatively lubricate the spindle on the complete length of the thread
with the help of the nut .
You may use common oils and greases for ball bearings (soda soap greases) as lubricant. But
please avoid lubricants with additives such as graphite and MOS.
Due to the axial movement between nut and spindle the loss of lubricant is higher than for ball
bearings so that it is not possible to have it lubricated for life time.
Oil lubrication
For higher speeds of the spindle ( >500 min
-1
) there is less heating up with oil lubrication then
with grease. But the maintenance intervals will be reduced depending on the applications you
should lubricate every 40 to 60 operating hours.
Grease lubrication
The grease lubrication will offer the advantages of an independent installation position and
larger lubricating intervals (from 300 to 700 operating hours) up to a speed of about 800 min
-1
.
If possible, use soda soap lubricants KP 2 K according to DIN 51 825.
5.4
Protective measures
Protect the lubricated ball screws from dust, chips.
Oil viscosity classes according to DIN 51517 T3
CLP ISO-VG for spindle Ø 16mm
Average speed [ min
-1
]
Recommended SO viscosity
class at 40 ° C
Required viscosity at operating tem-
peratures of about 30 °C (cST)
20
ISO VG 460
about 875
100
ISO VG 220
about 360
500
ISO VG 46
about 66
1000
ISO VG 22
about 36
1500
ISO VG 15
about 28