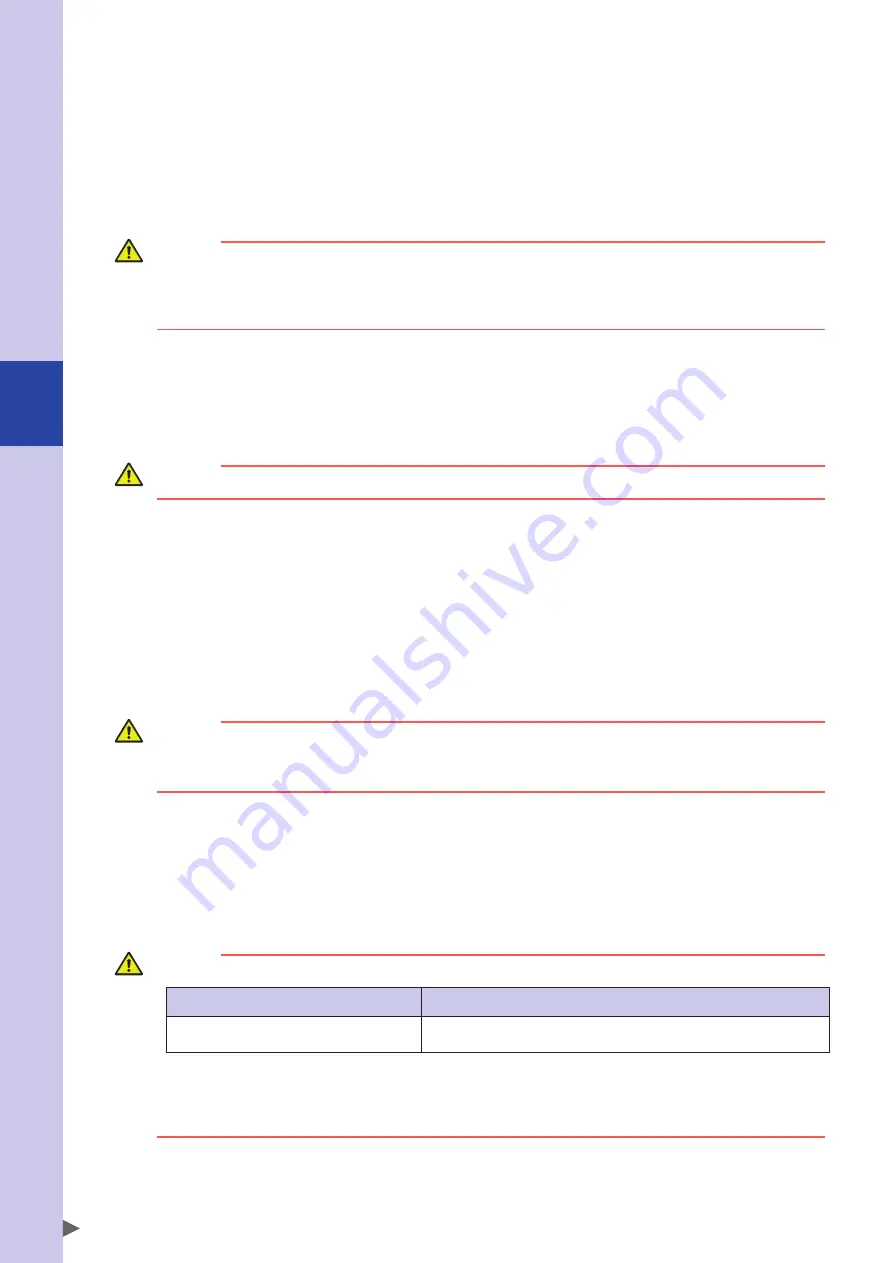
4
Edit
4-56
■
Origin shift
‹
ORGSFT
›
This parameter is used to correct the deviation amount of each axis if the work position deviates after the motor has been
replaced and an impact has been applied. When this parameter is initialized, "0" is set.
Set the electrical deviation origin position amount to the mechanical origin position of the robot. The value of this
parameter becomes the current motor position immediately after return-to-origin operation.
Example:
When the current position after moved to the work position before positional deviation is expressed by "A" pulse and the
current position after moved to the work position after positional deviation is expressed by "B" pulse, input the value (A - B).
CAUTION
• This parameter is important to determine the robot position.
• When this parameter is changed, the robot is put in the origin return incomplete status.
• This parameter is valid after performing absolute reset or return-to-origin.
• Setting incorrect values may cause of robot collision.
■
Dual offset
‹
DOFSET
›
The dual offset is the function that controls two motor axes of the same models with one motor axis and adjusts the origin
position of the sub axis to the main one. Refer to the YRCX operator's manual for details. When this parameter is
initialized, "0" is set.
CAUTION
This parameter is used only for the robots which are prepared to use dual offset function.
■
Origin method
‹
ORGMTD
›
This parameter sets the return-to-origin method of the robot. When this parameter is initialized, the value unique to the
model is set.
0: Mark method …… Method to set the origin position, such as match mark by the user
1: Sensor method …… Origin position detection method by inputting sensor
2: TORQUE (Stroke end method) … Origin position detection method by the robot stroke end
3: ZR_TORQUE (ZR-stroke end method) …
Origin position detection method by the specific robot stroke end
The origin position is detected by combining the Z and R-axis return-to-origin methods.
CAUTION
• If the setting is changed without consulting, your distributor shall not be held responsible for any trouble arising
from this setting change.
• When this parameter is changed, the robot is put in the origin return incomplete status.
■
Origin direction
‹
ORGDIR
›
This parameter sets the movement direction when the robot performs return-to-origin. When this parameter is initialized,
the value unique to the model is set.
0: Minus … The minus (-) direction of the motor position is the return-to-origin direction.
1: Plus … The plus (+) direction of the motor position is the return-to-origin direction.
CAUTION
• When any of the conditions shown below is satisfied, do not change the factory setting.
Conditions
Problem at setting change
The model is the F14H lead 5 mm.
When performing stroke end return-to-origin on the non-motor side, the origin
position becomes unstable.
When the setting needs to be changed, contact your distributor.
• If the setting is changed without consulting, your distributor shall not be held responsible for any trouble arising
from this setting change.
• When this parameter is changed, the robot is put in the origin return incomplete status.
Summary of Contents for YRCX Series
Page 1: ...7 6HULHV DW 1R 1 5 5RERW RQWUROOHU 23 5 7 21 0 18 6 5 5RERWV 5 6HULHV...
Page 2: ......
Page 10: ......
Page 12: ......
Page 14: ......
Page 20: ......
Page 28: ......
Page 164: ......
Page 166: ......
Page 178: ......
Page 186: ......
Page 264: ......
Page 265: ......
Page 266: ...DW 1R 1 XWKRUL HG LVWULEXWRU 3ULQWHG LQ XURSH...