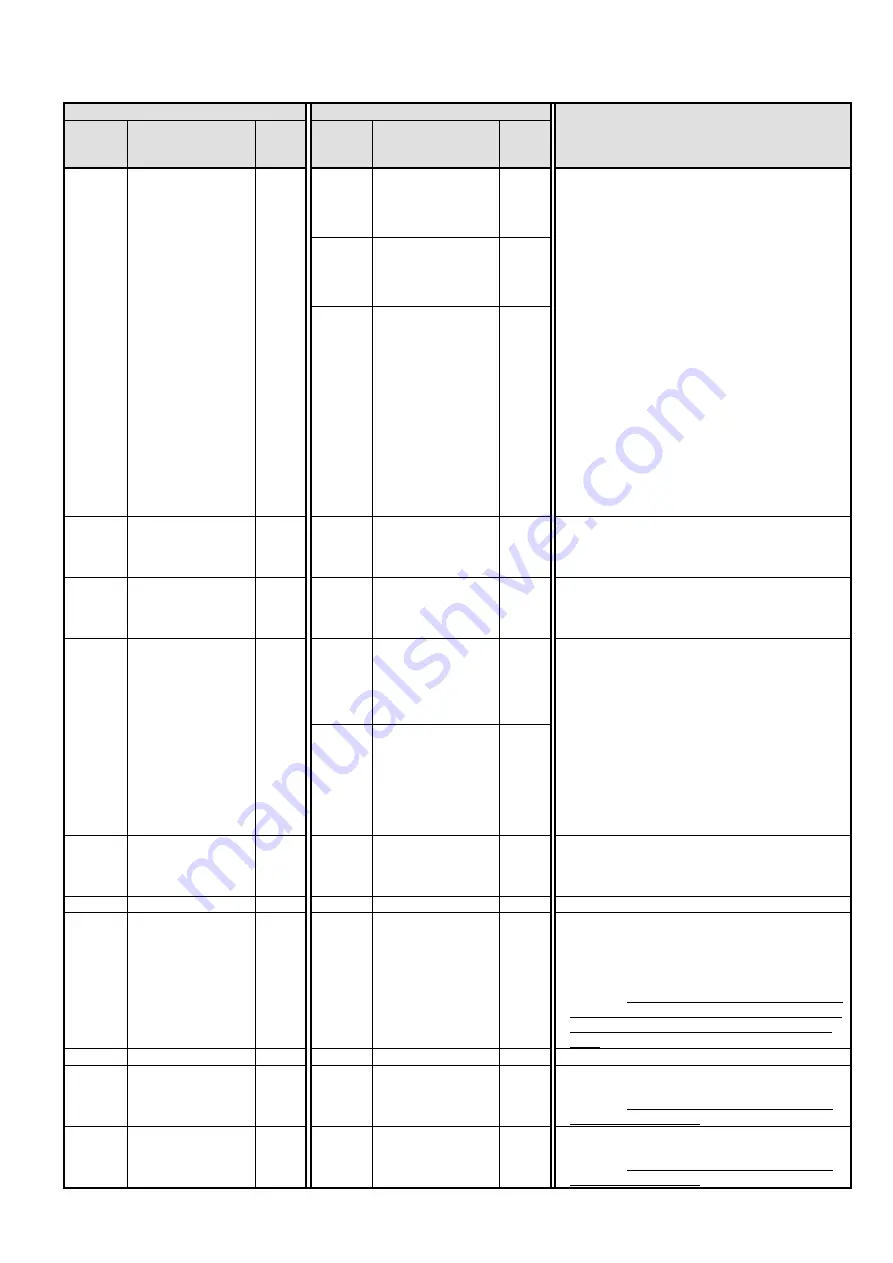
38
9.5. Parameters Related to Sequence
SS2 series
G5 series
Remarks
Parameter
No.
[hex]
Parameter name
Default
setting
[dec]
Parameter
No.
[dec]
Parameter name
Default
setting
[dec]
Pn60
Positioning
Completion Range
25
Encoder
unit
Pn431
Positioning
Completion Range 1
10
Command
unit
Set the positioning completion range.
● For the SS2 series, the encoder unit (multiple
of 4) is used in setting.
● For the G5 series, the command unit
(command pulse unit) is used in setting.
* Be careful in setting because the setting unit
and motor resolution are different between
the SS2 and the G5 series.
* For the SS2 series, the output turns ON
when the position error reaches not more
than
Positioning Completion Range
(Pn60).
* For the G5 series, you can use
Positioning
Completion Condition Selection
(Pn432)
to set the output condition. The default
setting is
0: Positioning completion output
(INP1) turns ON when the position error is
within the Positioning Completion Range 1
(Pn431).
* The setting unit of the G5 series can be
changed to
1: Encoder units (external scale
units)
by using
Position Setting Unit
Selection
(Pn520).
Pn432
Positioning
Completion
Condition Selection
0
Pn520
Position Setting Unit
Selection
0
Pn61
Zero Speed
Detection
20
r/min
Pn434
Zero Speed
Detection
50
r/min
Set the rotation speed at which to output the zero
speed detection output.
● The default setting differs between SS2 and
G5 series.
Pn62
Rotation Speed for
Servomotor
Rotation Detection
50
r/min
Pn436
Rotation Speed for
Motor Rotation
Detection
1,000
r/min
Set the rotation speed at which to output the
motor rotation speed detection output (TGON).
● The default setting differs between SS2 and
G5 series.
Pn63
Deviation Counter
Overflow Level
100 x
256
Encoder
unit
Pn014
Error Counter
Overflow Level
100,000
Command
unit
Set the detection level of an Error Counter
Overflow Error (Alarm No. 24).
● For the SS2 series, the encoder unit (multiple
of 4) is used in setting.
● For the G5 series, the command unit
(command pulse unit) is used in setting.
* Be careful in setting because the setting unit
and motor resolution are different between
the SS2 and the G5 series.
* The setting unit of the G5 series can be
changed to
1: Encoder units (external scale
units)
by using
Position Setting Unit
Selection
(Pn520).
Pn520
Position Setting Unit
Selection
0
Pn64
Deviation Counter
Overflow Alarm
Disabled
0
-
-
-
The G5 series has no parameter of
Deviation
Counter Overflow Alarm Disabled
. Increase
the set value of
Error Counter Overflow Level
(Pn014) to avoid detection.
Pn65
Not used.
-
-
-
-
-
Pn66
Stop Selection for
Drive Prohibit Input
0
Pn505
Stop Selection for
Drive Prohibition
Input
0
Set the stop method when the drive prohibition
function is activated by the input of
Forward/Reverse drive prohibition input
(POT/NOT).
● In both the SS2 and the G5 series, the default
setting is 0: After a dynamic brake stop (error
counter cleared), the torque command is 0 in
the drive prohibition direction (error counter
held).
Pn67
Not used.
-
-
-
-
-
Pn68
Stop Selection at
Alarm
0
Pn510
Stop Selection for
Alarm Detection
0
Set the stop method for alarm (error) occurrence.
● In both the SS2 and the G5 series, the default
setting is 0: After a dynamic brake stop, the
dynamic brake is held.
Pn69
Stop Selection with
Servo OFF
0
Pn506
Stop Selection with
Servo OFF
0
Set the stop method for servo OFF.
● In both the SS2 and the G5 series, the default
setting is 0: After a dynamic brake stop, the
dynamic brake is held.