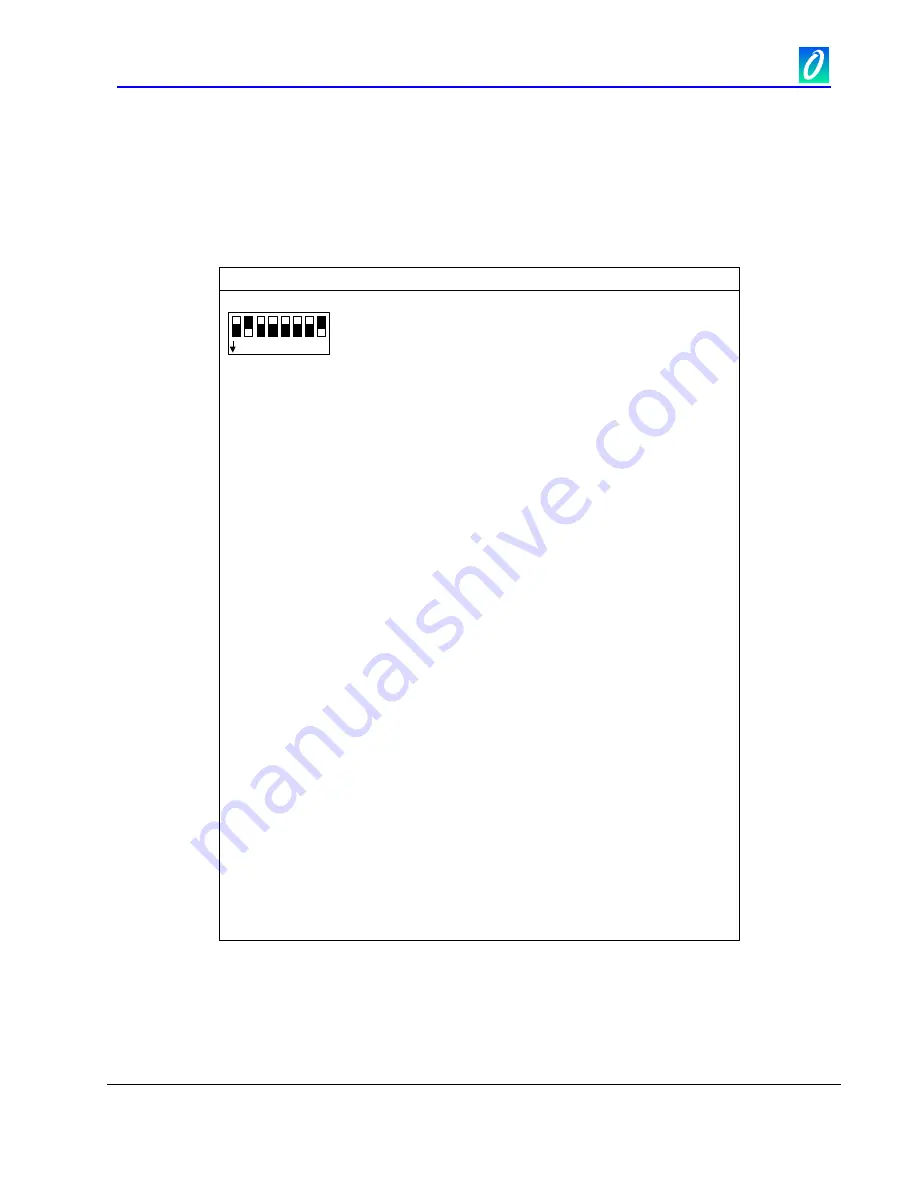
Maxiflex P3 PAC User Manual
66
-© Omniflex
UMM126XR18.pdf
For more control over the various settings, or for configuring Modbus Master, you must set
the serial port in the configuration file using Omniset.
The required protocol including any address selection is made by the correct selection on the
Serial Port Switch.
Follow the instructions below to set the required protocol mode:
Example of Serial Port DIP switch setting
8
1 2 3 4 5 6 7
ON
[ White square indicates position of switch lever ]
Switches 1-5 = Node Address
This is set as a binary number with Switch 1 the least significant bit, and
Switch 5 the Most significant bit.
To calculate the address setting, add the following weightings of the
switches that are ON:
1 ON = +1
2 ON = +2
3 ON = +4
4 ON = +8
5 ON = +16
In this example an address of 2 is selected.
Switch 6 reserved
.
(always leave switched off)
Switch 7 Default Conet/s (19200 baud) Protocol Select
.
Switch 7 ON = Conet/s default mode of operation
In this example this switch is shown OFF.
Switch 8: Default Modbus ASCII Slave Protocol Selection
Switch 8 ON = Modbus ASCII slave at 9600 baud
(Data bits: 7;Parity: none; Stop bits: 1)
In this example, the Switch 8 is shown in the ON position to set the
serial port to its default configuration of MODBUS Slave ASCII at 9600
baud.
Set as shown, (switches 2 and 7 on) the serial port will operate as a Modbus
ASCII slave port at 9600 baud, and will respond to the slave address of 2.
Set both Switch 7 and 8 OFF to use internal software settings, set using
Omniset. If either switch is on, then the internal software settings will be
ignored.
Table 11.1: Serial Port Address switch settings