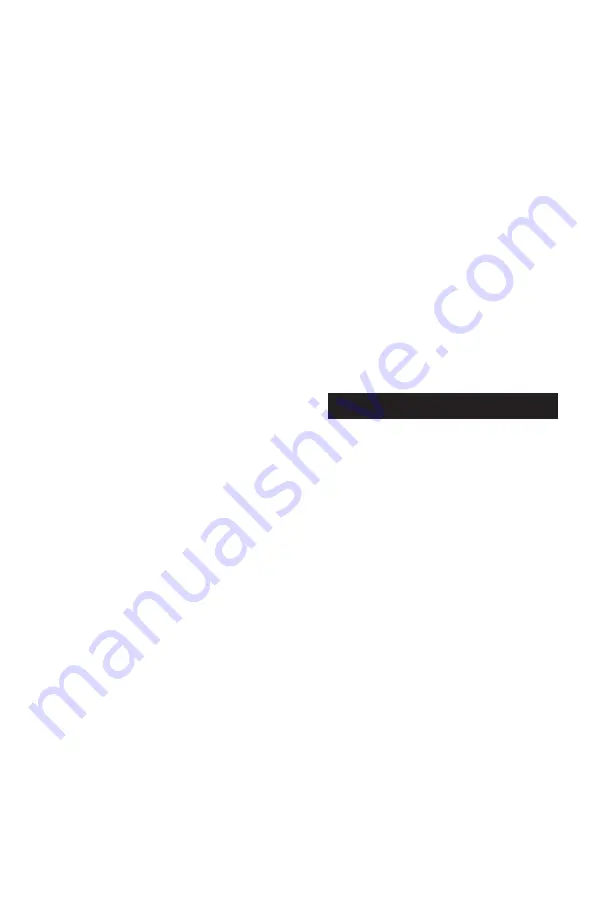
Flow altering devices such as elbows, valves,
and reducers can affect accuracy. The fol-
lowing recommended guidelines are given to
enhance accuracy and maximize performance.
Distances given here are minimum require-
ments; double them for desired straight pipe
lengths.
Upstream from the turbine, allow a minimum
straight pipe length at least 10 times the in-
ternal diameter of the turbine. For example,
with the
A109GMA100NA1
turbine, there
should be 10 inches (25.4 cm) of straight
pipe immediately upstream. The desired
upstream straight pipe length is 20 inches
(50.8 cm).
Downstream from the turbine, allow a mini-
mum straight pipe length at least 5 times the
internal diameter of your turbine. For ex-
ample, with the
A109GMA100NA1
turbine,
there should be 5 inches (12.7 cm) of
straight pipe imme-diately downstream. The
desired downstream distance is 10 inches
(25.4 cm).
A typical back pressure of 5 to 50 PSI (0.34
to 3.4 bar) will prevent cavitation. Create
back pressure by installing a control valve
on the downstream side of the meter at the
proper distance detailed above.
Foreign material in the liquid being
measured can clog the turbine’s rotor and
adversely af-fect accuracy. If this problem is
anticipated or experienced, install screens to
filter impurities from incoming liquids.
Model
A109GMA025NA1
Maximum Particulate Size
Inches:
0.005
Microns:
125
Mesh:
55
Standard Sieve:
125 µm
Alternative Sieve:
No. 120
Models
A109GMA100NA1 and
A109GMA200NA2
Maximum Particulate Size
Inches:
0.018
Microns:
500
Mesh:
28
Standard Sieve:
500 µm
Alternative Sieve:
No. 35
All Series FTB380 turbines are Factory Mu-
tual Approved and carry a Class 1, Division 1
Approval for hazardous environments. They
are tested and calibrated at the factory using
state-of-the-art calibration procedures and
test equipment.
To ensure accurate measurement, remove all
air from the system before use. To purge the
system of air:
1. Ensure some back pressure on the turbine.
2. Open the discharge valve or nozzle and
allow fluid to completely fill the system.
Make sure the stream is full and steady.
3. Close the discharge valve or nozzle.
4. Start normal operations.
Each turbine contains a removable back cov-
erplate. Leave the coverplate installed unless
accessory modules specify removal.
1. To protect against leakage, seal all threads
with an appropriate sealing compound.
Make sure the sealing compound does
not intrude into the flow path.
2. Make sure the arrow on the outlet is
pointed in the direction of the flow.
3. Tighten the turbine onto the fittings. Use
a wrench only on wrench flats.
NOTE: If connecting to new male threads,
burrs and curls can adversely effect
accuracy. Correct the problem prior to
turbine installation.
It is strongly recommended that accuracy be
verified prior to use. To do this, remove all
air from the system, measure an exact known
volume into an accurate container, and verify
the volume against the readout or recording
equipment. If necessary, use a correction
factor to figure final volume. For best results,
accuracy should be verified periodically as
part of a routine maintenance schedule.
The display electronics is normally installed
on the turbine housing at the factory unless
ordered without it.
3
CONNECTIONS
Summary of Contents for FTB380 Series
Page 1: ...FTB380 SERIES Aluminum Turbine Flowmeters...
Page 2: ......
Page 14: ......
Page 15: ......
Page 16: ...M 5065 1111...