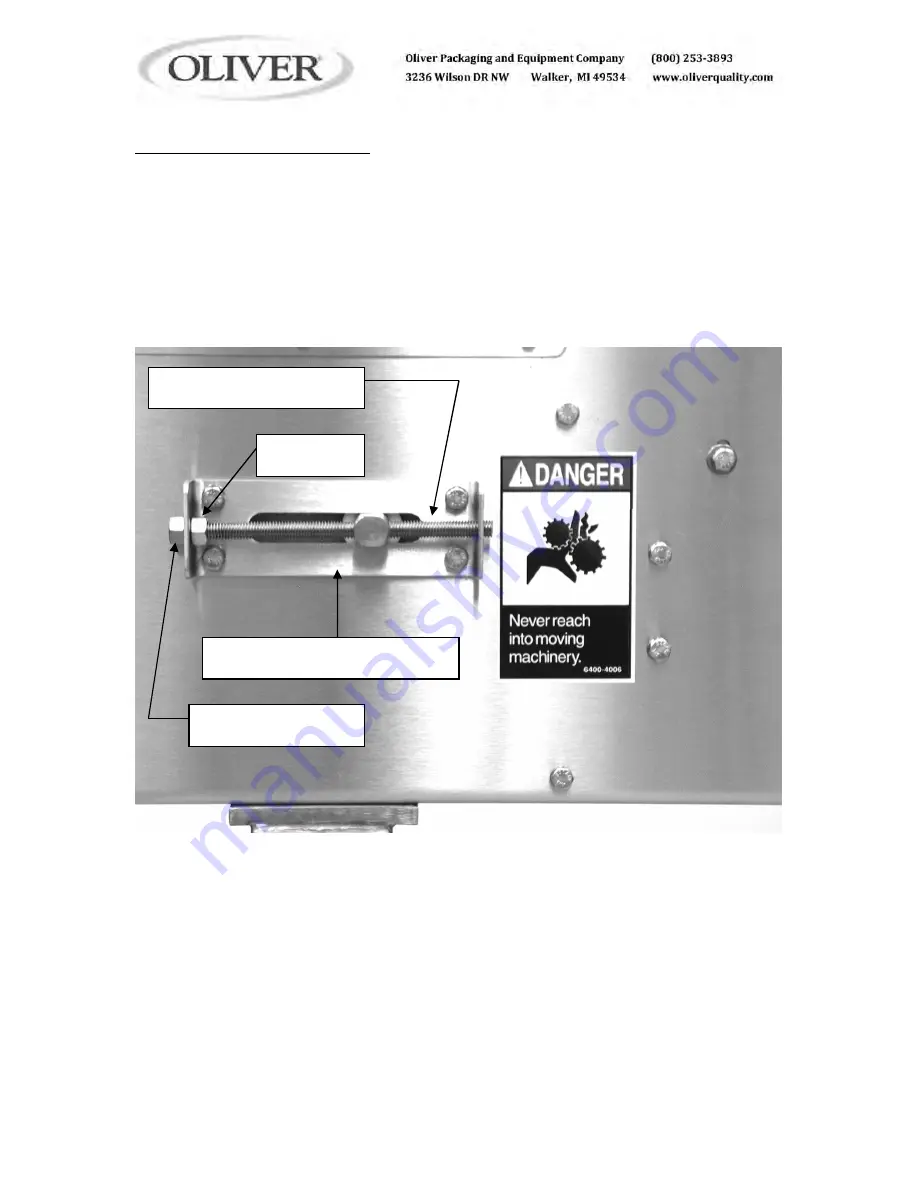
1808-CE
1808S20011
8-2
(
“ROUTINE MAINTENANCE” CONTINUED)
The main drive chains are tensioned by adjusting the chain take-up units located at the
in-feed end of the machine (see photo below). To tighten the chains, loosen the jam nut
on the adjusting screw. Turn the adjusting nut clockwise to tighten the chains. Turn the
adjusting nut ½ turn on one side of the machine and then ½ turn on the other side of the
machine and check chain for tension. Proper tension is when the return tray carriers on
the bottom of the conveyor can be lifted up about 1
” without the chain feeling over tight.
If the chain is very sloppy when lifted, it is too loose. After adjusting, tighten the jam
nuts.
JAM NUT
ADJUSTING SCREW
CHAIN TAKE-UP UNIT
ADJUSTING NUT
Summary of Contents for 1808-CE
Page 10: ...1808 CE 1808S20017 2 6 NAMEPLATES DIAGRAM...
Page 41: ...1808 CE 1808S20023 11 1 FRAME AND DRIVE ASSEMBLY Rev 7 31 13...
Page 44: ...1808 CE 1808S20024 12 1 LEG ASSEMBLY...
Page 46: ...1808 CE 1808S20025 Rev 5 23 19 13 1 HEAT SEAL FRAME ASSEMBLY...
Page 49: ...1808 CE 1808S20026 Rev 5 23 19 14 1 HEAT SEAL ROLL ASSEMBLY...
Page 51: ...1808 CE 1808S20027 15 1 DISCHARGE ASSEMBLY...
Page 53: ...1808 CE 1808S20028 16 1 FILM MANDREL ASSEMBLY...
Page 55: ...1808 CE 1808S20029 Rev 5 23 19 17 1 ELECTRICAL ASSEMBLY...