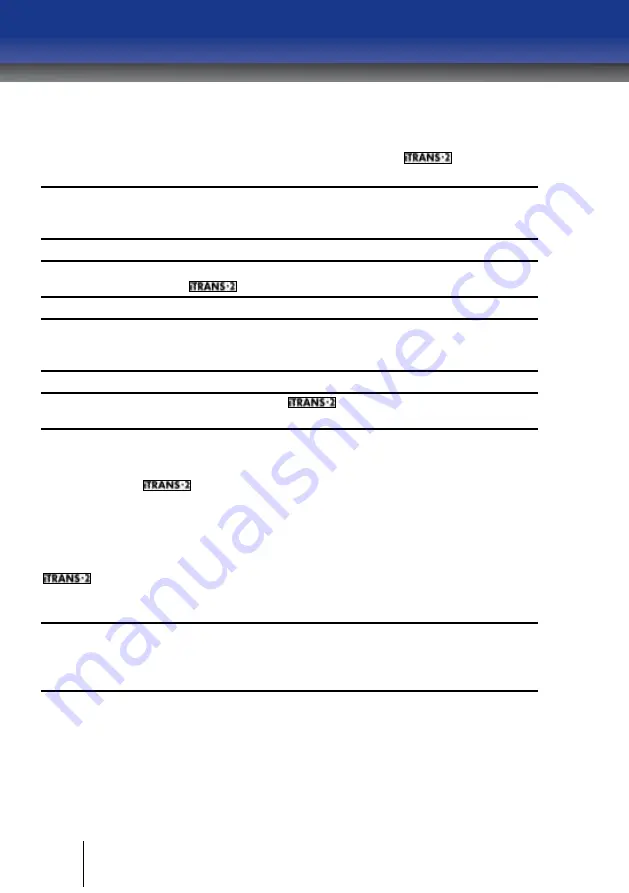
24
5.
Thread control, signal, and power wires into the transmitter housing.
6.
Shielding from either the controller or remote sensors should be
bonded to the enclosure screw located inside the
.
IMPORTANT:
Use of this product in areas where it may be subject to large
amounts of electromagnetic interference may affect the reliable operation of
this device and should be avoided.
WARNING:
Supply wire with a minimum rating of 90°C must be used for
interconnection to the
.
NOTE:
For classified locations, a “poured” wire seal must be installed within
18 inches (457mm) of the main unit for both power entry and remote
sensors.
NOTE:
Remove power from the
before making any wiring
connections.
Alarm Relay Wiring (J1, J5, and J6)
To connect the
control wires to the three relay terminals on the relay
board, wire the unit to the connectors shown in Figure 2-4. The low alarm
relay is activated when the low alarm threshold is met. This is a non-
latching, Normally Open (NO) contact. The high alarm relay is activated
when the high alarm threshold is met. This is a non-latching, Normally Open
(NO) contact. The fault alarm relay is activated upon power-up of the
. When the fault condition is met, the circuit opens. This is an
Electronically closed (NC) contact. See Figure 4-1 for relay wiring.
NOTE:
It is recommended that on-board relays should not be used to drive
loads directly. On-board relays should be used to drive a secondary, higher-
power relay which is connected to the control device (e.g., strobe, siren,
exhaust fan, etc.).
Summary of Contents for iTrans 2
Page 6: ...6...
Page 9: ...9...
Page 10: ...10...
Page 19: ...19 Figure 2 5 Electronics Board for Remote Sensor...
Page 20: ...20...
Page 28: ...28 Figure 4 4 Wiring Diagram for a Single On board Sensor...
Page 31: ...31 Figure 4 7 Wiring Remote Sensors Back to...
Page 52: ...52...
Page 60: ...60...
Page 66: ...66...
Page 72: ...72 Figure A 4 Wiring Diagram of Single Sensor HART Supported...
Page 73: ...73 Figure A 5 Wiring Diagram of Dual Sensor HART Supported...
Page 80: ...80 Figure A 15 EDD GUI View Figure A 16 PC to HART Interface Wiring Diagram...
Page 86: ...86...
Page 90: ...90...
Page 98: ...98...
Page 100: ...100...
Page 104: ...104...
Page 105: ...105...