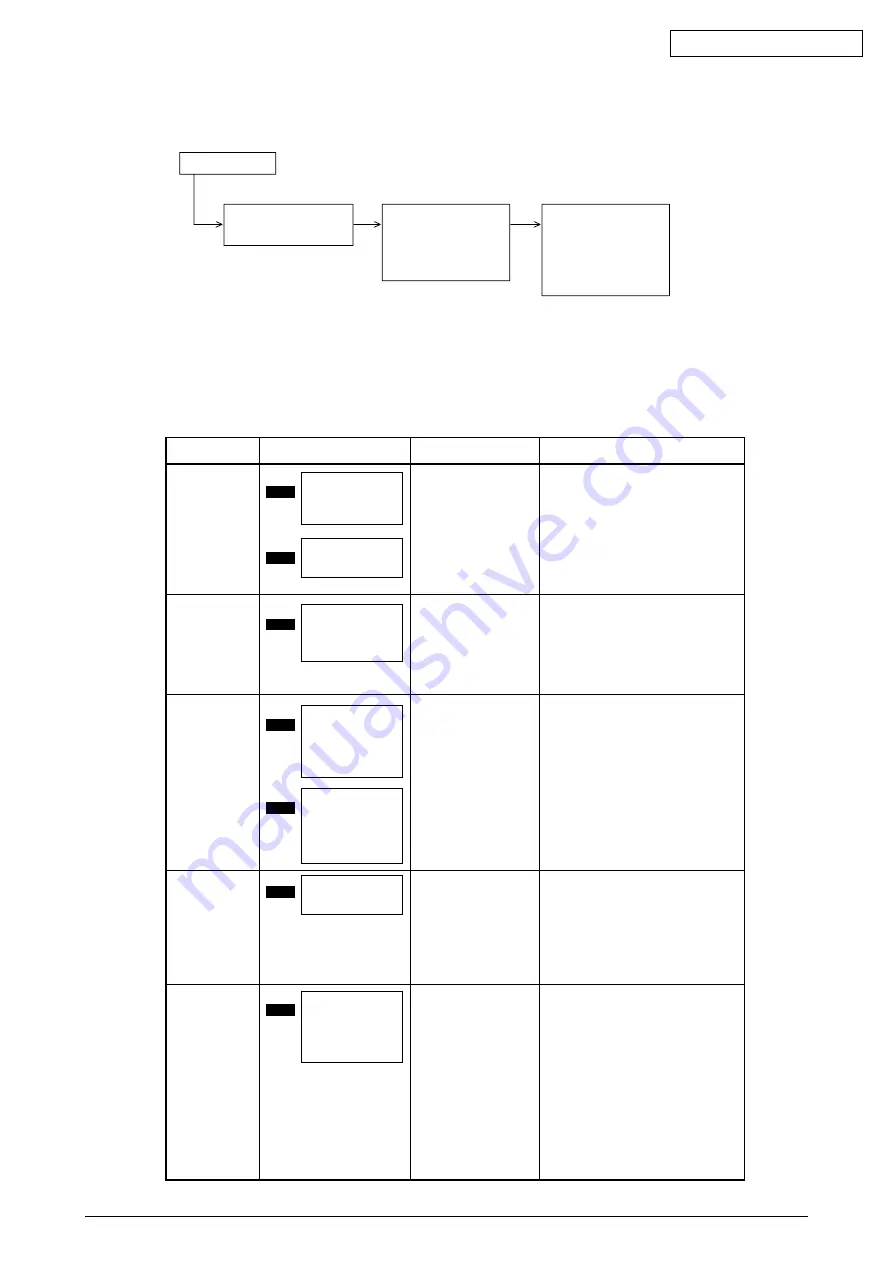
43502101TH Rev.1
154 /
Oki Data CONFIDENTIAL
4.3
Troubleshooting Method
When a problem occurs, go through the troubleshooting according to the following procedure.
4.3.1
LCD Status Message List
The listing of the statuses and problems displayed in the form of messages on the LCD is provided in
Table 4-1.
Table 4-1
Problem occurs
Problem displayed by
the LCD message
Troubleshooting
according to the LCD
Status Message List
(see 4.3.1)
Carry out detailed
troubleshooting
according to the
Troubleshooting Flow
(see 4.3.1)
Jam error
(feeding)
Jam error
(ejection)
Paper size error
Tray paper out
Paper size
request
Notifies of occurrence of
jam while the paper is
being fed from High
Capacity Second Paper
Feeder.
Scroll disply.
Notifies of occurrence of
jam while the paper is
being ejected from the
printer.
Scroll disply.
Notifies of incorrect size
paper feeding from High
Capacity Second Paper
Feeder.
Scroll disply.
Notifies of no paper state
of the High Capacity
Second Paper feeder.
Scroll disply.
Notifies of correct paper
size for the High capacity
Second Paper Feeder.
Scroll disply.
OPEN UPPER
COVER
PAPER JAM
CHECK TRAY2
PAPER JAM
OPEN UPPER
COVER
EXIT JAM
OPEN UPPER
COVER
PAPER SIZE
ERROR
CHANGE PAPER
TO mmmm/pppp
TRAY2 SIZE
MISIMATCH
LOAD mmmm
TRAY2 EMPTY
mmmm : Papre size
(A4, Letter, Legal,
etc.)
CHANGE PAPER
TO mmmm/pppp
TRAY2 SIZE
MISMATCH
mmmm : Papre size
(A4, Letter, Legal,
etc.)
pppp : Media Type
(Plain, Transparency,
etc.)
• Check the paper in the High Capacity
Second Paper Feeder.
Carry out the recovery printing by
opening and closing the cover, and
turn the error display off.
• When the problem occurs frequently,
go through the Troubleshooting.
• Check the paper in the printer. Carry
out the recovery printing by opening
and closing the cover, and turn the
error display off.
• Check the paper in the High Capacity
Second Paper Feeder.
Also check to see if there was a
feeding of multiple sheets.
Carry out the recovery printing by
opening and closing the cover, and
turn the error display off.
• Load the paper in High Capacity
Second Paper Feeder.
• Load the requested size paper in the
High Capacity Second Paper
Feeder.
Classification
LCD Status Message
Description
Recovery method
Summary of Contents for B4500 Series
Page 1: ...Oki Data CONFIDENTIAL B4500 B4550 B4600 Maintenance Manual 032007A PRINTING SOLUTIONS ...
Page 17: ...43502101TH Rev 1 17 Oki Data CONFIDENTIAL Upper cover unit Figure 2 2 Upper cover ...
Page 85: ...43502101TH Rev 1 85 Oki Data CONFIDENTIAL 2 High Voltage Sensor Board ...
Page 88: ...43502101TH Rev 1 88 Oki Data CONFIDENTIAL 3 Power Supply Board CN2 CN101 ...
Page 171: ...Please refer to the Illustrated Parts Manual for spare part information ...