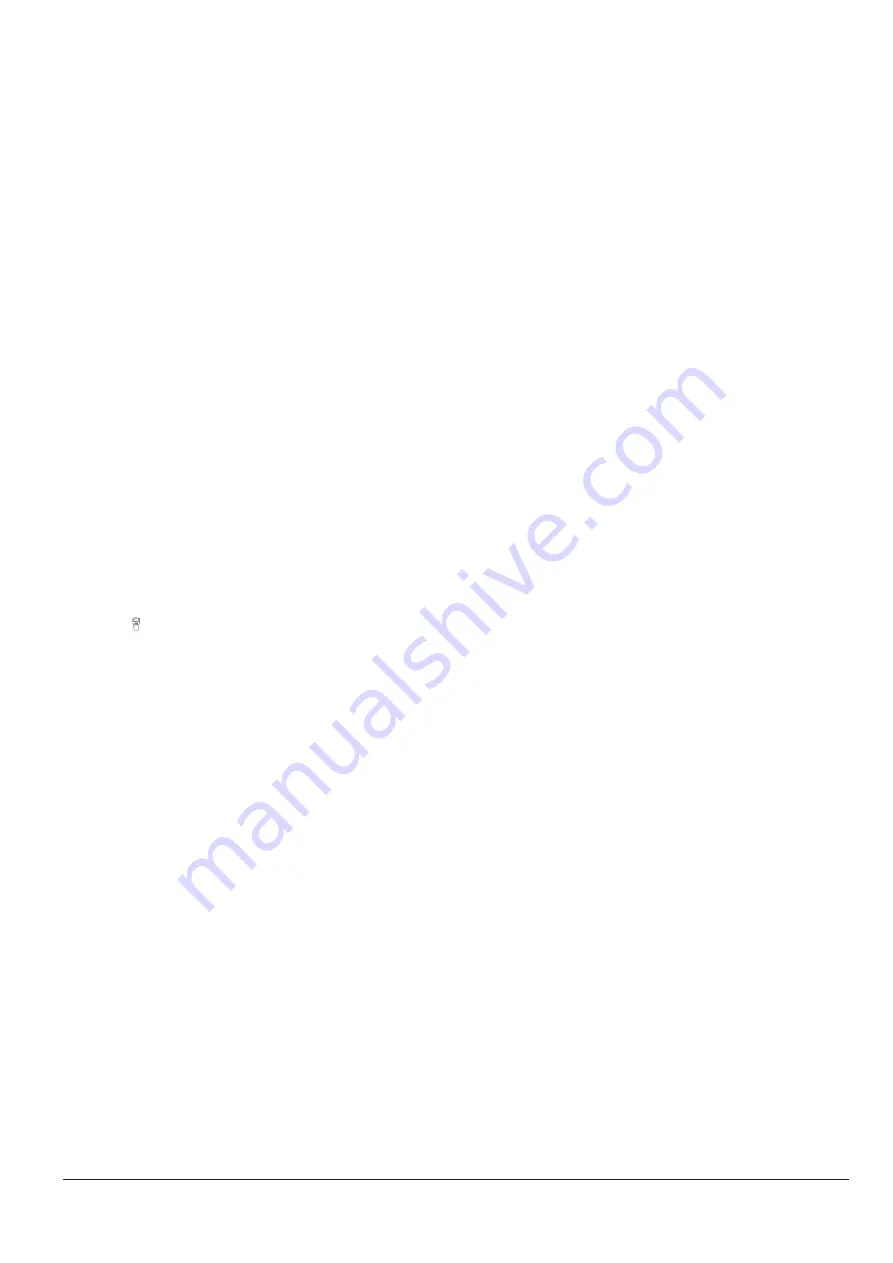
2
© 2014 OJ Electronics A/S
DATA LOGGING
OJ Air2 Master features a data logging function. Insert a standard SD
card into the OJ Air2 Master card reader. If the SD card contains a higher
program version than that which is already installed on the OJ Air2 Master,
updating will be started when the "turn and push" button on the OJ Air2
hand terminal is pressed. If the SD card is empty or contains a lower pro-
gram version than that which is already installed on the OJ Air2 Master, OJ
Air2 Master will automatically begin to log data on the SD card. The logged
data can be sent for analysis and troubleshooting at OJ Electronics A/S
on prior agreement with one of the company's support staff. The SD card
must not exceed 8 GB.
NOTE! The SD card must be inserted into the OJ Air2 Master with the
connectors facing forwards (fig. 8).
INSTALLATION
OJ Air2 Master is designed to be mounted on a standard 35 mm DIN rail and
installed in a control panel or similar enclosure which complies with local
requirements on electrical installations. (For dimensions, see figs 1 and 2.)
The supply voltage is 24 V AC ±15%, max. 60 VA, 50/60 Hz and is con-
nected via 1.5 mm
2
screw terminals on the OJ Air2 Master (fig. 7). The power
supply must not be connected to earth (GND). The enclosure rating is IP20.
Input and output signals to sensors and actuators are connected to OJ Air2
Master by connectors equipped with screw terminals for max. 1.5 mm
2
.
OJ Air2 Master is equipped with:
• 6 x digital potential-free and freely definable inputs
• 2 x digital potential-free max. 230 V AC / 5 A relay outputs
• 5 x digital potential-free max. 30 V AC / 3 A relay outputs
• 2 x analogue inputs (0-10 V DC)
• 2 x temperature sensor inputs (PT1000 thermistor)
• 3 x analogue outputs (0-10 VDC / Max. 10 mA)
• 1 x RJ45 port for external Modbus TCP/IP
• 1 x RJ12 port for connection of hand terminal
• 1 x RJ12 port for external Modbus RTU
• 3 x RJ12 ports for internal system Modbus RS485
Supply voltage
A 24 V AC power supply must be connected to terminals 1 & 2 on OJ Air2
Master. The power supply must not be connected to earth (GND).
Electrical connections are illustrated in fig. 7.
Connection of OJ Air2 hand terminal
The OJ Air2 hand terminal is connected to OJ Air2 Master via the RJ12 6/6
port marked on the front (see fig. 4).
Installation of TCP/IP connection
The TCP/IP network cable is connected to OJ Air2 Master via the RJ45
port marked TCP/IP (see fig. 4)
Installation of external Modbus cable
External Modbus RS485 is connected to OJ Air2 Master via the RJ12 port
marked MODBUS RS485 (see figs 4 & 11).
Communication speed can be set to 9.6 kBaud, 19.2 kBaud or 38.4 kBaud.
Installation of internal Modbus cable
Internal Modbus is connected to OJ Air2 Master via an RJ12 port. OJ Air2
Master is equipped with three RJ12 ports for connection and loop connec-
tion of RS-485 Modbus to other Modbus components in the installation.
Modbus ports are marked RS485 B and RS485 C (see fig. 5).
NOTE! The port marked RS485 A has no internal function and should there-
fore not be used.
IP address
The IP address in the OJ Air2 Master can be set to either "DHCP" or
"Static" in the "User"/"Internet" menu.
SPECIFICATION
Sensor inputs
OJ Air2 Master is equipped with two sensor inputs for PT1000 sensors
(1000 Ω @ 0°C).
Sensor 1 should be connected to the "Tin 1" input, terminals 16 & 17.
Sensor 2 should be connected to the "Tin 2" input, terminals 17 & 18.
Note: terminal 17 is shared by Tin 1 and Tin 2.
The measurement range of the sensors is -40°C to +100°C.
Electrical connections are illustrated in fig. 7. Terminal 19 is not used.
Digital inputs
OJ Air2 Master is equipped with six potential-free digital inputs.
Digital input 1 should be connected to the "Din 1" input, terminals 3 & 4.
Digital input 2 should be connected to the "Din 2" input, terminals 4 & 5.
Note: terminal 4 is shared by Din 1 and Din 2.
Digital input 3 should be connected to the "Din 3" input, terminals 6 & 7.
Digital input 4 should be connected to the "Din 4" input, terminals 7 & 8.
Note: terminal 7 is shared by Din 3 and Din 4.
Digital input 5 should be connected to the "Din 5" input, terminals 9 & 10.
Digital input 6 should be connected to the "Din 6" input, terminals 10 & 11.
Note: terminal 10 is shared by Din 5 and Din 6.
Electrical connections are illustrated in fig. 7.
Analogue inputs
OJ Air2 Master is equipped with two analogue inputs for 0-10 V DC signals.
Input 1 should be connected to the "Ain 1" input, terminals 12 & 14.
Input 2 should be connected to the "Ain 2" input, terminals 13 & 14.
Note: terminal 14 is a shared GND for Ain 1 and Ain 2.
The input range of the analogue inputs is 0-10 V DC.
Electrical connections are illustrated in fig. 7.
Terminal 15 is co24 V DC.
Digital outputs
OJ Air2 Master is equipped with seven potential-free digital relay outputs.
Digital outputs 1 & 2 may be connected to max. 230 V AC/DC - AC1.
Digital output 1 should be connected to the "Dou 1" output, terminals 24 & 25.
Digital output 2 should be connected to the "Dou 2" output, terminals 26 & 27.
Digital outputs 3-7 may be connected to max. 30 V AC/DC.
Digital output 3 should be connected to the "Dou 3" output, terminals 28 & 29.
Digital output 4 should be connected to the "Dou 4" output, terminals 30 & 31.
Digital output 5 should be connected to the "Dou 5" output, terminals 32 & 33.
Digital output 6 should be connected to the "Dou 6" output, terminals 34 & 35.
Digital output 7 should be connected to the "Dou 7" output, terminals 36 & 37.
Electrical connections are illustrated in fig. 7.
Analogue outputs
OJ Air2 Master is equipped with three 0-10 V DC analogue outputs, which
can be used to connect control signals for heating battery, rotary heat
exchanger or damper motor on cross-flow heat exchanger.
Analogue output 1 should be connected to the "Aou 1" output, terminals
20 & 21.
Analogue output 2 should be connected to the "Aou 2" output, terminals
20 & 22.
Analogue output 3 should be connected to the "Aou 3" output, terminals
20 & 23.
Note: terminal 20 is a shared GND for Aou 1, Aou 2 and Aou 3.
Electrical connections are illustrated in fig. 7.
TECHNICAL DATA
Processor ..................................ARM9, 32-bit
Operating system ......................Linux, Unix type
Supply voltage ...........................24 V AC ±15%, 50/60 Hz
Power consumption ..................max. 60 VA
Electrical connection .................max. 1.5 mm
2
, screw terminals
TCP/IP .......................................10/100 Mbit Ethernet, RJ45 port
Hand terminal ............................Modbus RS485, 115 kBaud, RJ12 port
Internal Modbus ........................RS-485, 38.4 kBaud
Internal Modbus connection .....2 x RJ12 (6P6C)
Internal Modbus protocol ..........38.4 kBaud, 1 start bit, 8 data bits, 1 stop bit
Digital inputs ..............................6 x 3.3 kΩ, pull-up
Analogue inputs .........................2 x 0-10 V, resolution 10 mV, Rin 20 kΩ
Sensor inputs ............................2 x PT1000
Digital output (DO1-DO2) ..........Max. 230 V / 5A relay
Digital output (DO3-DO7) ..........Max. 30 V / 3A relay
Analogue outputs .....................3 x 0-10 V DC
Ambient operating temperature .0°C/+50°C
Dimensions ................................156 x 93 x 58 mm
Modbus cable dimension ..........MPFK6S or similar
Enclosure ...................................IP20, ABS
Weight .......................................430 g
COMMUNICATION
Internal Modbus communication
Internal communication between OJ Air2 system components such as OJ
Fan IO and RHX2M is via Modbus with the following communication proto-
col: 38.4 kBaud, 1 start bit, 8 data bits, 1 stop bit and no parity.
External communication
OJ Air2 Master can be connected to a BMS system via Modbus RS485,
Modbus TCP/IP, BACnet or LonWorks.
Modbus
Modbus protocol can be downloaded from www.ojelectronics.com.
BACnet
BACnet protocol can be downloaded from www.ojelectronics.com.
LonWorks
LonWorks protocol and newest xif file can be downloaded from
www.ojelectronics.com.
SERVICE AND MAINTENANCE
No special maintenance is required.
Please contact your supplier if faults arise.