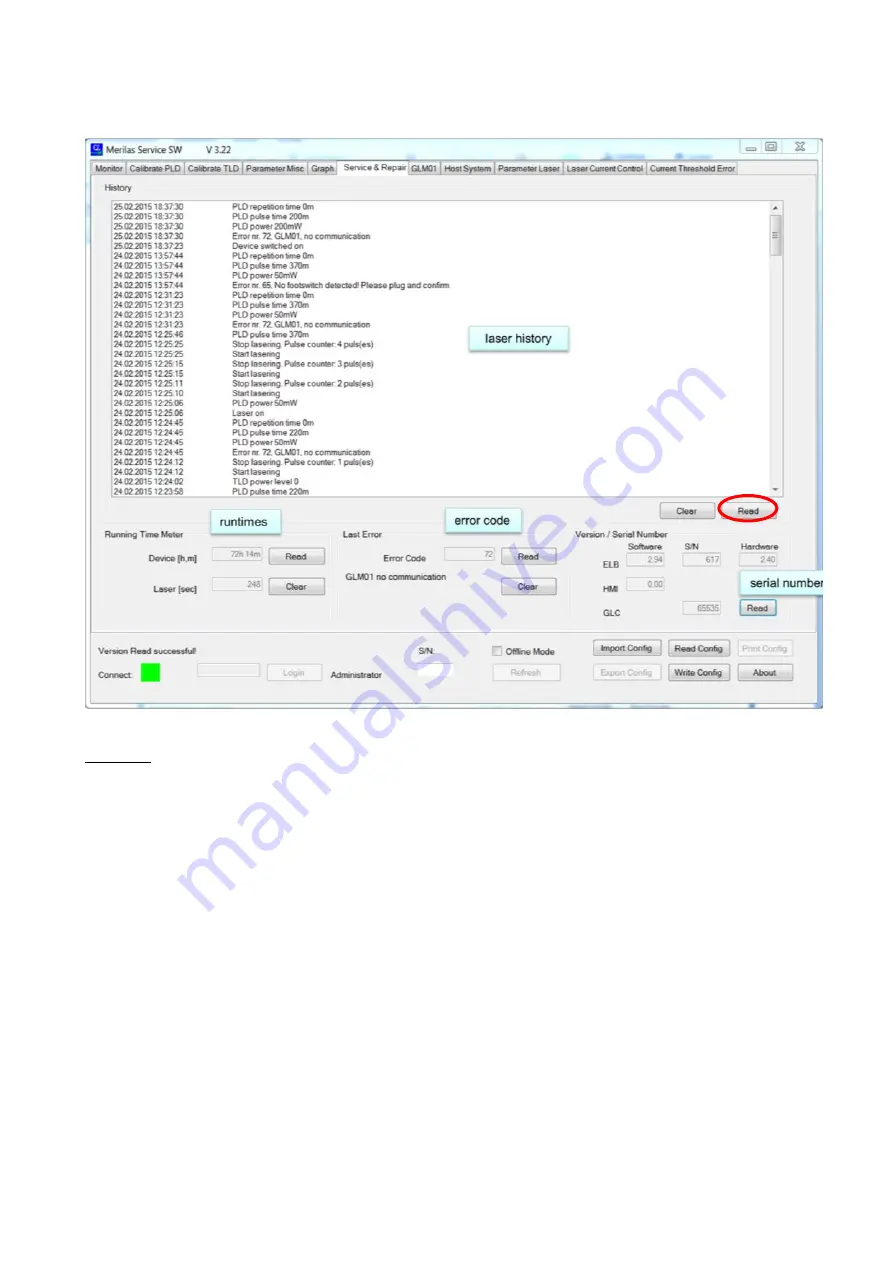
2021-03-23 / Rev. 10
VV016042
36
9.7.1.3
Safe History
This page contains information which is important for second-level support.
Procedure:
1. On this tab you can read the history, runtime, error code and version numbers.
2. To make a print screen and store the file,
right click into the blank window, and click on “Select all”, then right click onto
the marked text, and click on “Copy to Clipboard”. Open Word, or Word-Pad, and paste into document and safe
(SN…….._YYMMDD_Technician_History.doc) for future reference.
Summary of Contents for OS 4
Page 1: ......
Page 44: ...2021 03 23 Rev 10 VV016042 44 10 2 Core PCB ...
Page 134: ...2021 03 23 Rev 09 VV016042 134 18 Appendix C Safety check Please see form on next page ...
Page 136: ...2021 03 23 Rev 09 VV016042 136 19 Appendix D Functional test Please see form on next page ...
Page 151: ...VV016042 2021 03 23 Rev 10 ...