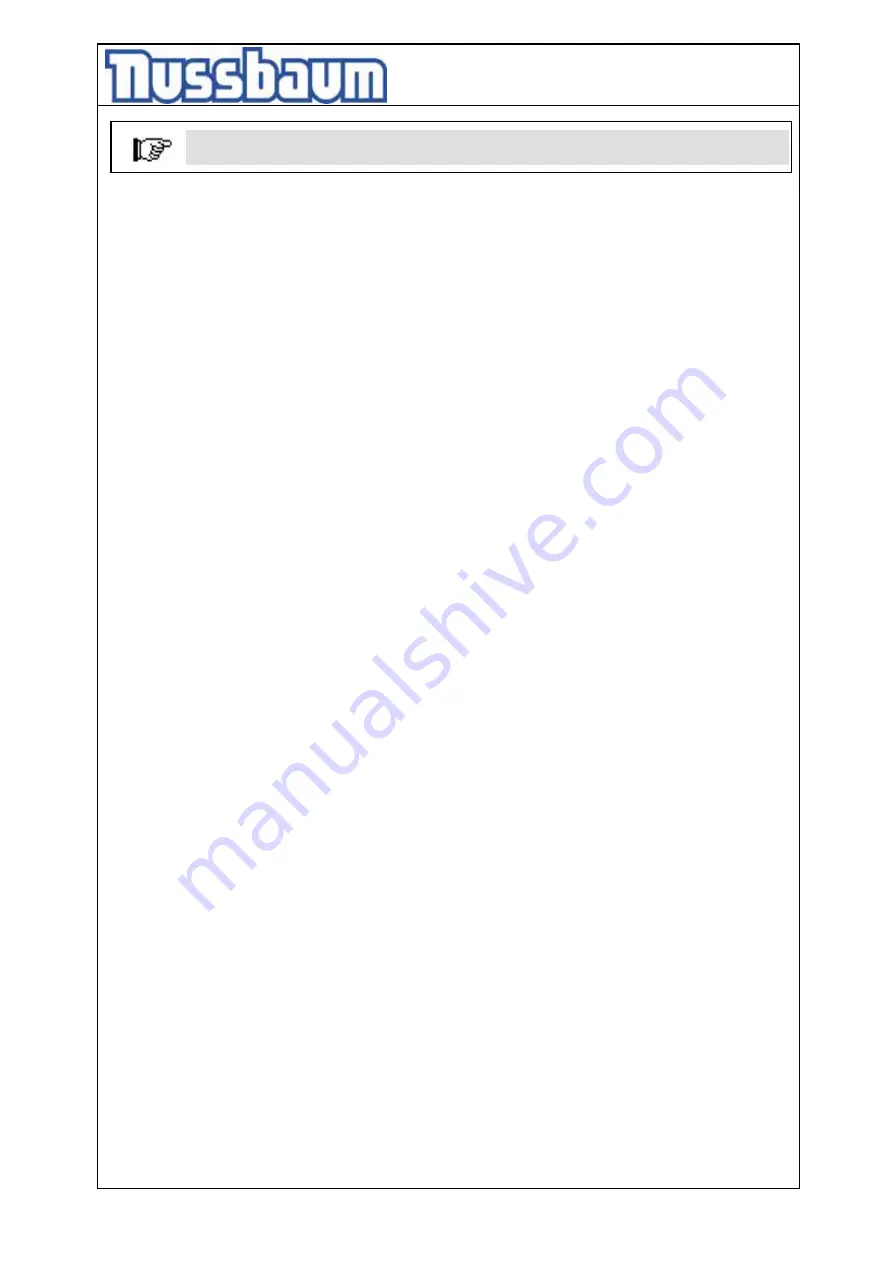
Operating Instruction and Documentation
SPL 4000
- 5 -
Filling out and undersigned and copying this sheet and send the original to the lift
manufacturer. The copy remains in the manual.
Otto Nußbaum GmbH & Co. KG
Korker Straße 24
D-77694 Kehl-Bodersweier
Record of installation
The automotive lift with the
serial number:............................................ was installed on:...............................................
at the firm:................................................. at:.....................................................................
The initial safety check was carried out and the lift was started.
The installation was carried out by the operating authority/competent (please delete as applicable).
The initial safety check was carried out by a competent person before the initial operation.
The operating authority confirms the correct installation of the automotive lift, the competent person
confirms the correct initial operation.
Used Dowels(*):________________________________(Type/Name)
Minimum anchorage depth (*) kept: _________________mm
F
ok
Starting torque (*) kept: __________________________NM
F
ok
............................................ ..................................................... ............................................
date name
of
the
operating
authority
signature of the operating authority
............................................ ..................................................... ............................................
date name
of
the
competent
person
signature of the competent person
Your customer service:.....................................................................................................(stamp)
(*) see supplement of the dowel manufacturers
Automotive Lift date: 07/2005 / Manual date: 04.12.2007
Summary of Contents for SPL 4000
Page 9: ...Operating Instruction and Documentation SPL 4000 9 2 5 Attestation of conformity...
Page 11: ...Operating Instruction and Documentation SPL 4000 11 3 3 Data sheet 4090 mm with extension...
Page 12: ...Operating Instruction and Documentation SPL 4000 12 3 3 1 Data sheet 3650 mm...
Page 13: ...Operating Instruction and Documentation SPL 4000 13 3 4 Foundation diagram 200mm...
Page 16: ...Operating Instruction and Documentation SPL 4000 16...