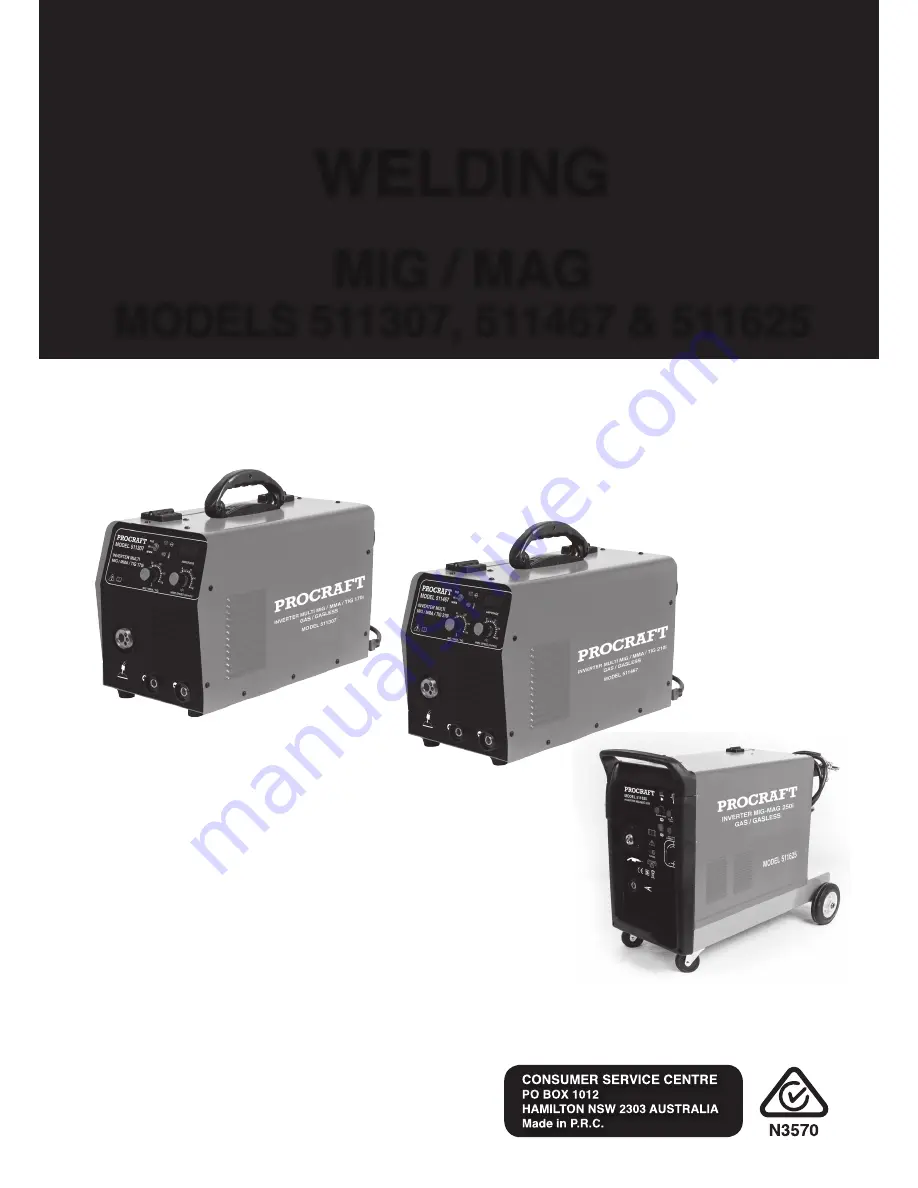
MIG / MAG
MODELS 511307, 511467 & 511625
WELDING
SAVE THIS MANUAL
WARNING!
READ AND UNDERSTAND ALL INSTRUCTIONS
Failure to follow all instructions listed below may result
in electric shock, fire, and/or serious injury.
SAVE THESE INSTRUCTIONS
Keep this manual for the safety warnings and precautions,
assembly, operating, inspection, maintenance and
cleaning procedures. Write the product’s serial number
in the back of the manual (or month and year of purchase
if product has no number). Keep this manual and the
receipt in a safe and dry place for future reference.
OPERATING INSTRUCTIONS
PROCRAFT