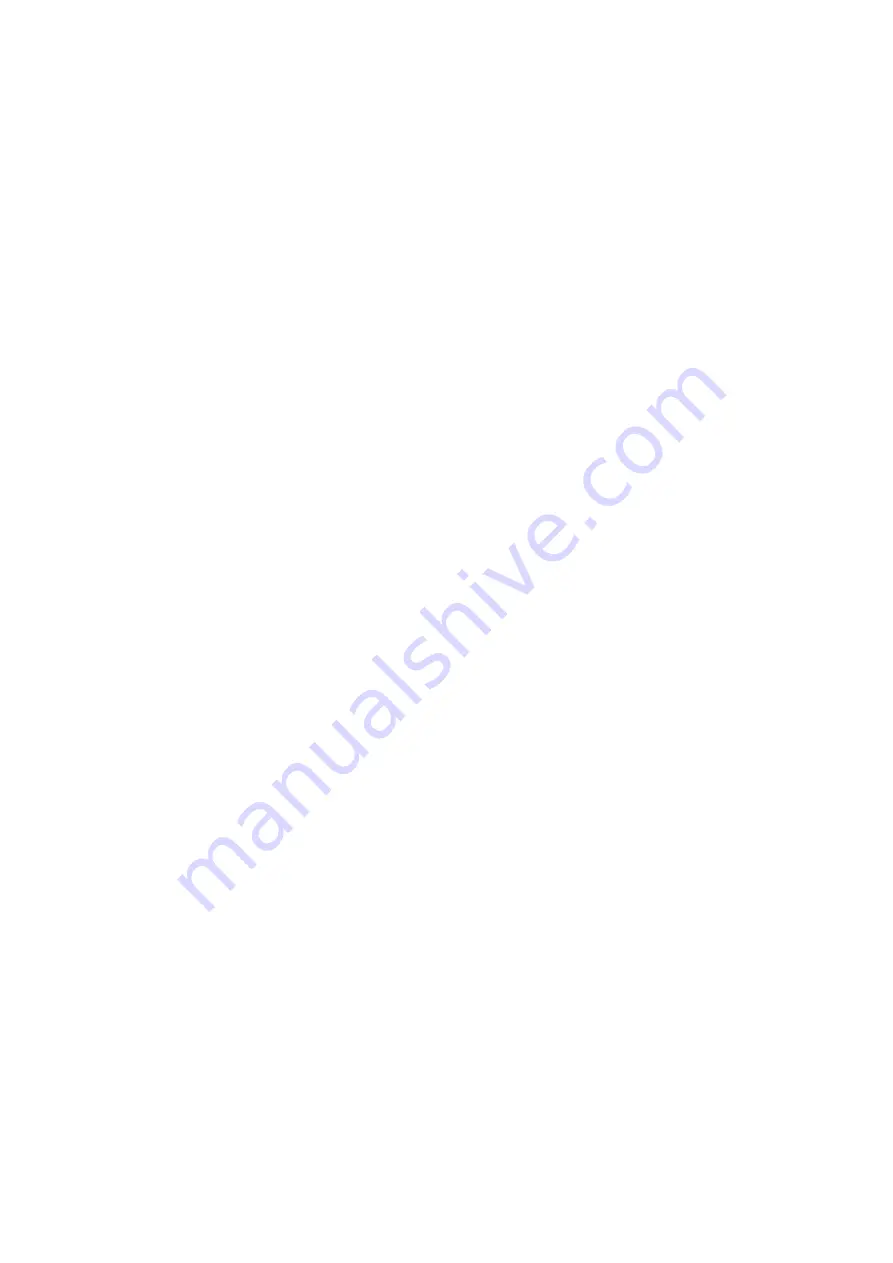
~ 3 ~
NOVATEK-ELECTRO MCK-108
This Operating Manual is intended to familiarize you with the design, the requirements for safety, operation
and maintenance procedures of the pumping plant controller MCK-108 (hereinafter referred to as either MCK-108
or the device).
MCK-108 complies with the requirements of:
IEC 60947-1;
ІEC 60947-6-2; CISPR 11; IEC 61000-4-2.
Harmful substances in amounts exceeding maximum permissible concentrations are not available
.
TERMS AND ABBREVIATIONS
List of Used Abbreviations:
EL
– Emergency Level
CPG
- Contact Pressure Gauge
UL
– Upper Level
AR time
- Automatic Reset time
LL
– Lower Level
DR
– Dry Run
MS
– Magnetic Starter
Conduction-measuring sensor
of liquid level is a sensor, the operating principle whereof is based on the increase
of electrical conduction between the common and the signal electrodes, if there is liquid between them.
Contact pressure gauge
(CPG) measures pressure, produced by liquid. For instance, one can determine the
liquid level in the tank by measuring pressure at the bottom of a tank (an outlet pipe).
The pressure gauge used in MCK-108 must correspond to type V (must have two contacts one of which must
be a break contact (closed at low pressure); the second contact must be a make one (closing at high pressure); if
pressure is between the high and the low levels, both contacts must be broken).
N o t e
- As usual, CPGs with two contacts have universal (transfer) contacts and the necessary type of CPG can be
set be the user.
Filling mode
- In this mode, MCK-108 controls the pump, filling the outer tank by pumping water from the well.
Drainage mode
is used for pumping liquid out of the well, for instance - in sewerage stations.
Two pumps may be used in the filling mode. For balancing the tear-and-wear, the user can set the alternate
operation of the pumps.
To prevent failure of the electric motor while draining the well one may use a dry run sensor (conduction-
measuring dry run sensor is located in the well). After deactivation of the pump electric motor due to dry run failure,
the pump activation delay is provided for the time of filling the well (the delay time is determined by the AR time
(automatic reset time) parameter and can be set by the user).
1. APPLICATION
The MCK-108 is designed to create technological processes automation systems, related to control and
maintaining of a set level of liquid substances in different kinds of tanks by controlling an electric motor (or electric
motors) of one or two pumps.
There is no amount of harmful substances, exceeding the maximum allowable concentration.
Maintaining of a set level of liquid substances is performed:
- in case of single-phase motor with capacity of up to 1 kW - by controlling the integrated pump relay;
- in case of three-phase motor or single-phase motor with capacity of over 1 kW - by controlling the magnetic
starter coil (contactor).
MCK-108 provides controlling of the electric motor (electric motors) of one or two pumps in an automated
mode according to one of the algorithms integrated into the device.
MCK-108 provides working with liquids of various electrical conduction - tap water and polluted water, milk and
food products (low-acid, alkaline etc.).
1.1
Controls and overall dimensions of MCK-108 are specified in figure 1.
1.2 Designation of contacts
1
– sensor "
DR
" (Dry Run);
2
– normally broken contact of the functional relay;
3
– normally closed contact of the functional relay;
4
– common contact of the functional relay;
5
– common contact of the pump relay;
6
– normally broken contact of the pump relay;
7, 8
– power supply;
9
– sensor "
LL
" (Lower Level);
10
– sensor "
UL
" (Upper Level);
11
– sensor "
EL
" (Emergency Level);
12
– common contact for sensors.