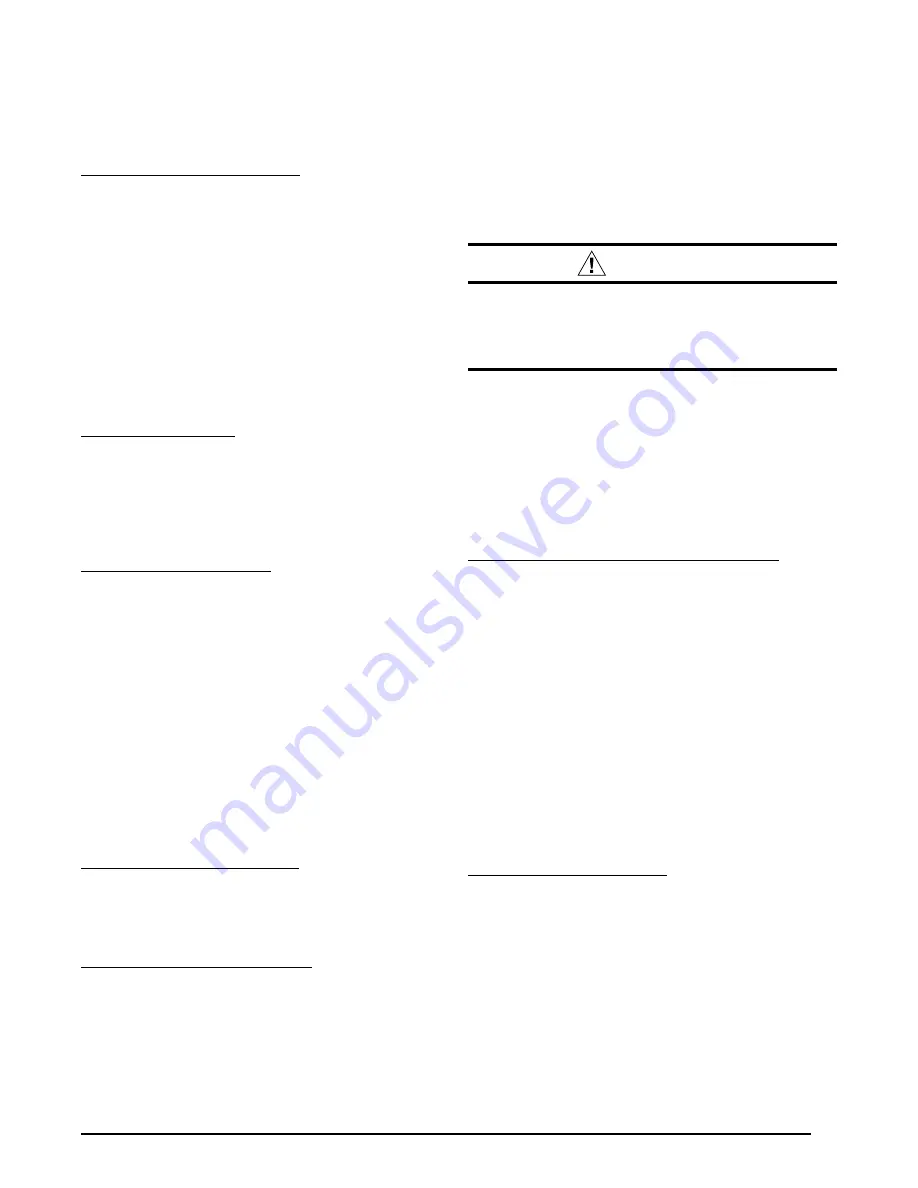
15
Heating Configurations
The back-up furnace in this heat pump is factory configured
to operate on high fire only, but can be field converted to
operate as a two-stage furnace.
Two Stage Heating Configuration
To configure this unit for two stage gas heating, a two
stage heat pump thermostat is used:
1. Remove the jumper wire between
W1
and
W2
on the
terminal block.
2. Remove the
brown
jumper wire from the low side of
the gas valve and place it on
W2
of the terminal block.
3. Connect
W1
and
W2
to the thermostat. When the call
for first stage heat is received, the furnace will operate
at low fire and the blower will run at a lower speed.
When second stage heat is initialized, the furnace will
operate at high fire and the blower will run at a higher
speed.
NOTE:
The furnace will stage between low fire,
high fire and off depending on the thermostat signal.
High Fire Configuration
When shipped from the factory, the
W1
and
W2
terminals
on the terminal block are jumpered together.
NOTE:
This
overrides the staging feature and the furnace operates
on high fire only. All of the burners will operate on a call
for heat and the variable speed blower will operate at a
higher speed.
Timed Staging Configuration
1. Remove the jumper between
W1
&
W2
on the terminal
block and replace with a delay on make timer (2 wire
style).
2. Move the brown wire from the low side of the gas valve
to the
W2
of the terminal block.
IMPORTANT NOTE: Do not connect the thermostat’s
W2 to the furnace wiring when using timed stage
configuration
NOTE:
When low fire on the gas valve is energized,
the furnace operates in low fire mode at a lower blower
speed and the timer begins its delay function. If the room
thermostat is not satisfied before the timer activates, the
furnace will stage to high fire and the blower will operate
at a higher speed until the thermostat is satisfied.
Two Stage Cooling Configuration
The low voltage (24V) connections from the thermostat
are made at the terminal block in the gas furnace side
of the unit.
Connect
Y2
from the thermostat to
Y2
on the
terminal block.
Checking Heat Anticipator Settings
• Add the current draw of the system components.
OR
• Measure the current flow on the thermostat
R
-
W
circuit
after the circulating blower motor has started. Set the heat
anticipator according to the thermostat manufacturer’s
instructions for heat anticipator settings.
Configuring the Variable Speed Blower
The variable speed blower has been designed to give
the installer maximum flexibility for optimizing system
performance, efficiency, and comfort. It is equipped with
a microprocessor-controlled variable speed motor that is
pre-programmed to deliver optimum airflow in a variety of
conditions and system configurations. Because the blower
can be configured in many ways, it is important to read
and follow all instructions carefully.
CAUTION:
To avoid personal injury or property damage,
make certain that the motor leads cannot
come into contact with any uninsulated metal
components of the unit.
Before operation, the variable speed blower must be
configured to match the unit with the system, climatic
conditions, and other system options.
With the blower
installed and configured properly, the furnace will gradually
change speed in response to changes in system variables
such as thermostat settings, duct static, filters, etc. The
variable speed blower is configured by setting the 6
switches located on the motor control board as described
below:
Selecting the Basic Cooling/Heat Pump Airflow
The basic cooling/heat-pump airflow is selected by setting
switches 1 - 4 on the variable speed input board. Table 11
(page 28) lists the recommended airflow values (CFM)
and selector switch settings for each nominal system
capacity. All airflows for other modes of operation (except
secondary gas heat) are determined by this basic setting.
NOTE:
The CFM values listed in Table 11 are not
dependent on duct static pressure. The motor automatically
compensates (within the limits of the motor) for changes
in duct static pressure.
NOTE:
If coil icing occurs, the basic cooling/heat-pump
airflow selected may be too low. Verify the selected setting
is within the range shown in Table 11 and the system is
properly charged. If icing continues, raise the selected
airflow one or two steps.
Selecting Gas Heating Airflow
The gas heating airflow is selected by setting switches
5 & 6 . Refer to Table 12 (page 28) and select a nominal
rise based on the furnace’s nominal efficiency and firing
input. Follow across the table row to find the switch setting
and nominal air-flow. Verify the selected rise is within the
specification shown on the furnace rating label.
NOTE:
The Dual Fuel iHybrid™ heat pump is equipped
with a two stage furnace. The units are shipped from the
factory configured for high fire only. If configuring for two-
stage operation, the furnace will run at low fire during a
call for emergency heat.