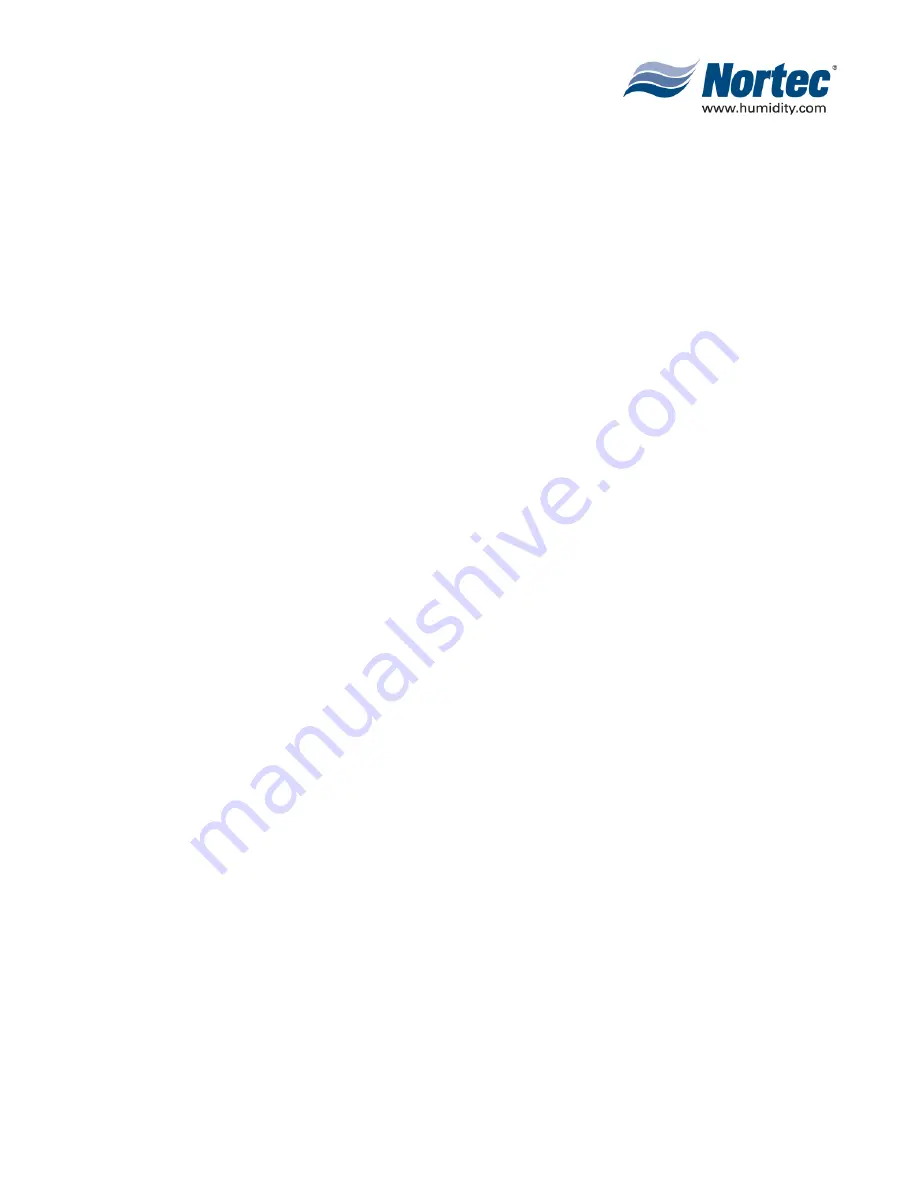
10-40
Page 32
2008-10-01
(f)
Provide easily accessible, primary voltage terminal block, internal to
cabinetry, for single point field connection of electrical supply.
(g)
Single point connection for gas inlet must be provided. Internal piping from
gas inlet to burners must be factory installed and tested. Field piping from
the gas inlet to the burners is not allowed.
(h)
Humidifier to prevent “back-siphoning” using an internal air gap for supply
water, to meet local plumbing codes.
(i)
Drain line to include a vacuum breaker to prevent siphon drainage of the
tank.
(j)
Allowance for combustion air shall be provided in cabinet ventilation design.
Option for direct vent of combustion must be available for use with BH
exhaust vent.
(4)
Gas appliance shall be low emission. Units with Carbon Monoxide (CO) levels
higher than 10 ppm and Nitrous Oxide (NOx) levels above 40 ppm are not
acceptable.
(a)
System shall be rated as a class I appliance certified for use with exhaust
vent type B.
XXXXX OR XXXXX
(b)
System shall be rated as a class III appliance certified for use with exhaust
vent type BH.
XXXXX OR XXXXX
(c)
System shall be rated as a class III appliance certified for use with exhaust
vent type BH and use with direct vent of combustion air. (Must be specified
for factory configuration)
(5)
Stainless Steel combustion chamber(s)/heat exchanger(s) shall have flat surfaces
to retard scale build-up. Tubular heat exchangers are not acceptable.
(a)
Each burner, capable of true modulation will provide steam production of 25
to 105 lbs/hr (11 to 48 kg/hr). Time proportioning modulation is not
acceptable.
(b)
Units with multiple heat exchangers, models 210 to 630 lbs/hr (95 kg/hr to
286 kg/hr) must be capable of producing a minimum output of 25 lbs/hr
(11kg/hr).
(c)
Units with multiple heat exchangers, models 210 to 630 lbs/hr (95 kg/hr to
286 kg/hr) must alternate the lead burners (duty cycle) to promote equal
usage.
(d)
Gas system with gas valve(s), explosion proof, premix combustion air
blower(s), microprocessor controlled ignition, flame sensing and fault
indicator light(s), 100% premix infrared burner(s), hot surface igniters(s) and
heat transfer efficiency maintained over all operating ranges.
Summary of Contents for GS Series GSP Indoor
Page 1: ...1503540 C GS Series GSTC GSP Indoor GSTC Outdoor Engineering Manual ...
Page 7: ...2008 10 01 THIS PAGE INTENTIONALLY LEFT BLANK ...
Page 8: ...10 00 Page 1 2008 10 01 10 00 PRINCIPLE OF OPERATION ...
Page 10: ...10 00 Page 3 2008 10 01 Figure 1 GS Indoor Series Figure 2 GS Outdoor Series ...
Page 11: ...10 00 Page 4 2008 10 01 Figure 3 GSTC Key Pad Figure 4 GSP Key Pad ...
Page 13: ...10 00 Page 6 2008 10 01 THIS PAGE INTENTIONALLY LEFT BLANK ...
Page 14: ...10 10 Page 7 2008 10 01 10 10 OPERATION ...
Page 17: ...10 10 Page 10 2008 10 01 Figure 3 Physical Dimensions GS Outdoor Humidifier ...
Page 21: ...10 10 Page 14 2008 10 01 Figure 4 GSTC GSP Indoor Clearance Figure 5 GSTC Outdoor Clearance ...
Page 23: ...10 10 Page 16 2008 10 01 THIS PAGE INTENTIONALLY LEFT BLANK ...
Page 24: ...10 20 Page 17 2008 10 01 10 20 MAINTENANCE ...
Page 27: ...10 20 Page 20 2008 10 01 THIS PAGE INTENTIONALLY LEFT BLANK ...
Page 28: ...10 30 Page 21 2008 10 01 10 30 OPTIONS ACCESSORIES ...
Page 35: ...10 30 Page 28 2008 10 01 THIS PAGE INTENTIONALLY LEFT BLANK ...
Page 36: ...10 40 Page 29 2008 10 01 10 40 SPECIFICATION ...
Page 44: ...10 40 Page 37 2008 10 01 THIS PAGE INTENTIONALLY LEFT BLANK ...