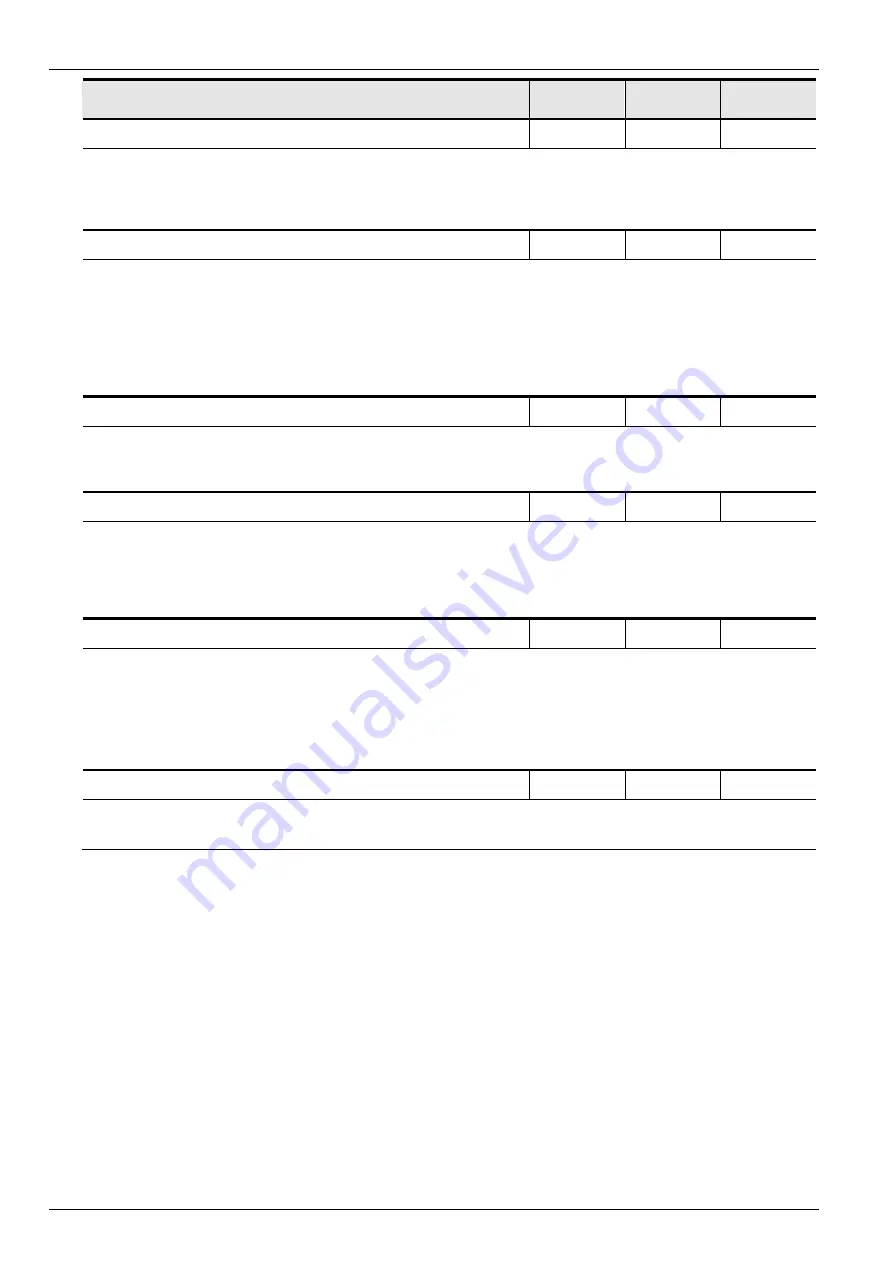
NORDAC SK 5xxE Manual
78
Subject to technical alterations
BU 0500 GB
Parameter
Set value / Description / Note
Device
Supervisor
Parameter
set
P211
Dynamic boost
S P
0 ... 150 %
[ 100 ]
The dynamic boost affects the torque generating current and is therefore a load-dependent
parameter. The factory 100% setting is also sufficient for typical applications.
Too high a value can lead to overcurrent in the FI. Under load therefore, the output voltage will be
raised too sharply. Too low a value will lead to insufficient torque.
P212 Slip
compensation
S P
0 ... 150 %
[ 100 ]
The slip compensation increases the output frequency, dependent on load, to keep the DC
asynchronous motor speed approximately constant.
The factory setting of 100% is optimal when using DC asynchronous motors and correct motor
data has been set.
If several motors (different loads or outputs) are operated with one FI, the slip compensation P212
must be set to 0%. This rules out a negative influence. This is equally valid for synchronous
motors that do not have slip due to their design.
P213
ISD control loop gain
S P
25 ... 400 %
[ 100 ]
This parameter influences the control dynamics of the FI current vector control (ISD control).
Higher settings make the controller faster, lower settings slower.
Dependent on application type, this parameter can be altered, e.g. to avoid unstable operation
P214 Torque
precontrol
S P
-200 ... 200 %
[ 0 ]
This function allows a value for the expected torque requirement to be set in the controller. This
function can be used in lifting applications for a better load transfer during start-up.
NOTE:
Motor torques (with rotation field R) are entered with a positive sign, generator
torques (with rotation field L) are entered with a negative sign. The reverse applies
for the counter clockwise rotation.
P215 Boost
precontrol
S P
0 ... 200 %
[ 0 ]
Only with linear characteristic curve (P211 = 0% and P212 = 0%).
For drives that require a high starting torque, this parameter provides an option for switching in an
additional current during the start phase. The application time is limited and can be selected at
parameter >Time boost precontrol< P216.
All current and torque current limits that may have been set (P112 and P536, P537) are
deactivated during the boost lead time.
P216
Time boost precontrol
S P
0.0 ... 10.0 s
[ 0 ]
Only with linear characteristic curve (P211 = 0% and P212 = 0%).
Application time for increased starting current.