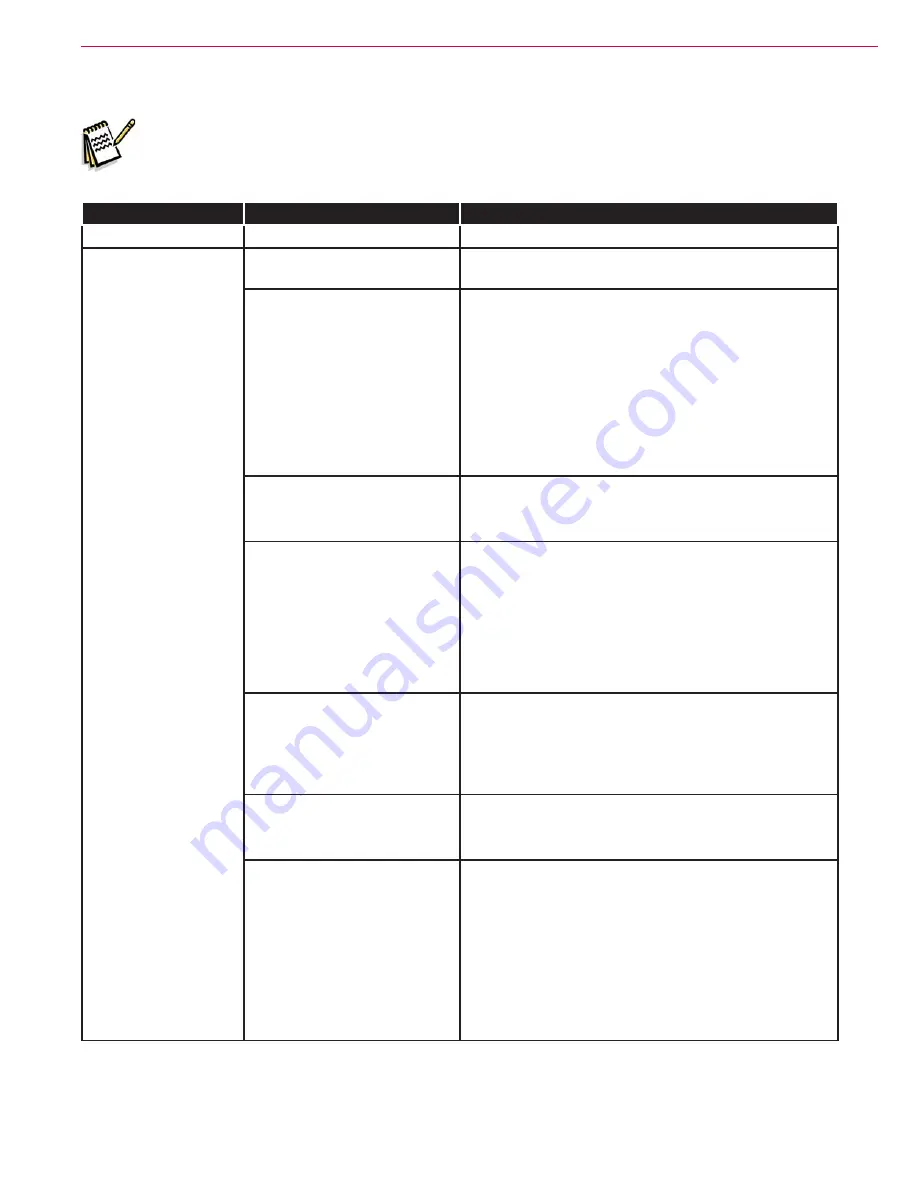
Solution System
150
Service Manual – SC6500
™
Troubleshooting
Note:
You can use the Service Test Mode to toggle the various system components on and off to
check for function. Refer to the
Control System/Service Mode
section for information on
how to enter and use the Service Test Mode.
Problem
Cause
Correction
Problem
Cause
Solution
Inadequate or no
solution flow
The solution shutoff valve is
in the off position.
Open the solution shutoff valve.
Clogged solution filter,
solenoid valve, hoses.
Clogged solution delivery
trough (cylindrical decks
only)
•
Check the solution filter for obstructions and clean
as necessary.
• Check the solenoid valve for obstructions and
clear as necessary.
• Check the solution hoses for obstructions and
clear as necessary.
• Check the solution manifold and solution delivery
trough and clear/clean as necessary (disc decks
only).
L1 Solution solenoid open
(Main Controller Error Code
33)
•
Check for open circuit in the L1 coil and wiring
(wire colors VIO and YEL/GRN).
•
Check for 36V at the L1 coil.
L1 Solution solenoid short
to ground (Main Controller
Error Code 34)
•
Disconnect the L1 solenoid coil wiring and check
to see if the code disappears.
−
If the code disappears, replace the solenoid.
−
If the code reappears, test the wiring for a short
back to the battery ground. Repair or replace
the defective wire.
•
Substitute a new A1 control board.
Solution solenoid L1
overload (Main Controller
Error Code 12)
•
Check for a short in the solenoid wiring and repair
as necessary.
• Check the solenoid coil resistance. The nominal
coil resistance is 74 ohms. If the coil resistance is
lower than 58 ohms, replace the solution solenoid.
Solution pump open (Main
Controller Error Code 35)
• Check for an open circuit in the M12 pump motor
and wiring (wire colors VIO and BLU/ORN).
•
Check for 36V at the pump motor.
Solution pump overload
(Main Controller Error Code
13)
•
Check for a short in the solution pump wiring and
solution pump M12 and repair as necessary.
• Disconnect the pump motor and run the machine
to see if the wiring is shorted.
•
Check the pump motor current draw. The normal
current load is 0.8 to 1.8 amps. A current load
of 3.2 amps or over will cause a pump motor
overload error code 13. If the pump motor draws
excessive current, replace the pump motor.