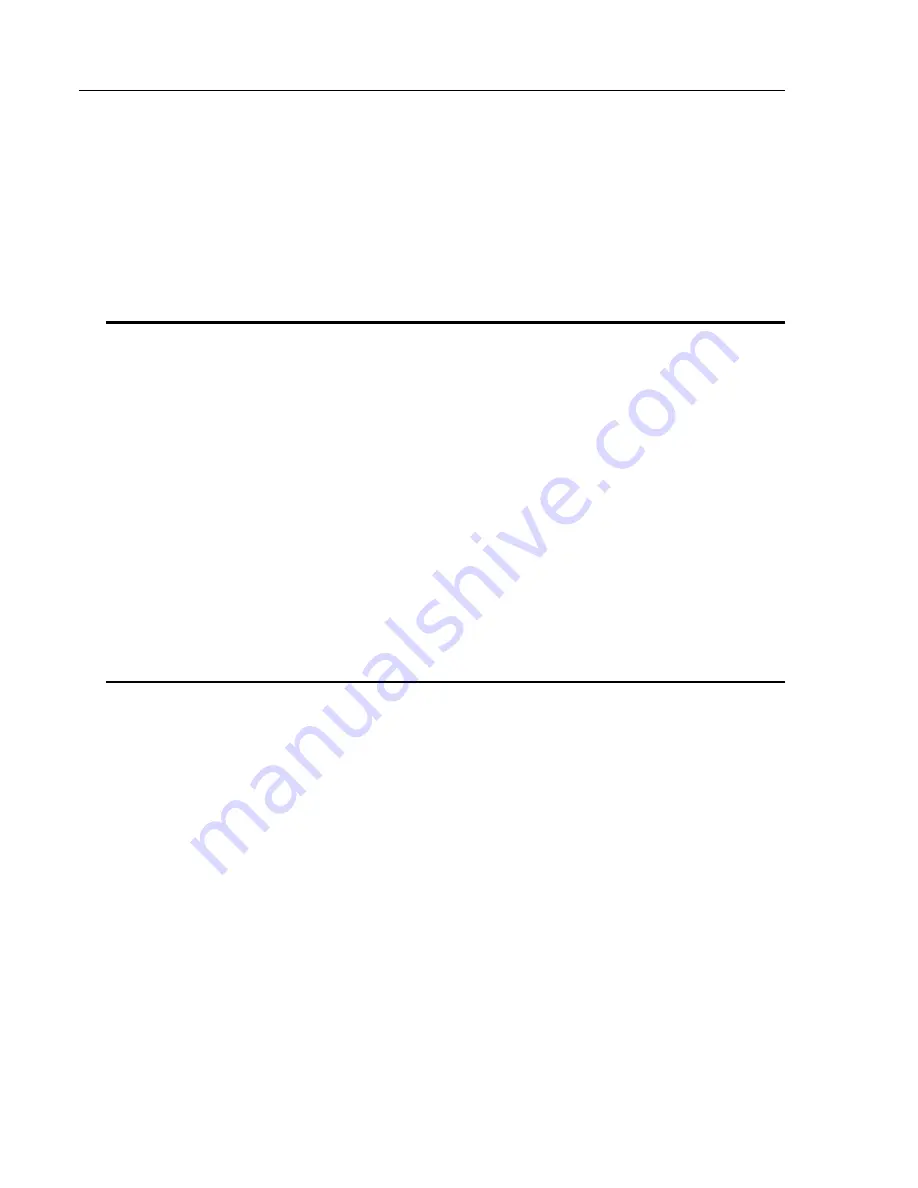
20
4 Troubleshooting
4.1
Table Top Does Not Float
Use the following procedure if the table top does not float, or lift up, when
pressure is applied to the isolators.
1.
Ensure that the supply pressure is 5–10 psig (0.4–0.7kg/cm
2
) above the
pressure reading of any of the leveling valves. If the load is increased,
the pressure should be increased to maintain the difference between
supply and valve pressure. Refer to Section 1.6.
2.
Check to see if all air lines are connected properly and the supply
pressure is adequate (see step 1). Refer to Figures 8, 9, and 10.
3.
Be sure that the needle valves are not closed completely.
4.
Check each leveling valve for clogging. To do this, press the control
arm down. Air should flow into the isolator, accompanied by the
familiar sound of moving air. Repair or replace any clogged valve. Use
the ARF filter/regulator to prevent this situation.
4.2
Poor Isolation Performance
The following may lead to poor isolation performance of your system.
1.
Vibration may be transmitted to the table through direct physical contact
of equipment with external sources of vibration.
2.
Isolators that float too high, too low, or are not centered may conduct
floor vibration to the table top. Refer to Section 2.3.2. (Figure 11)
Centered isolators will remain centered unless the table and isolators are
moved relative to each other.
3.
Equipment on the table may be vibrating at a resonant frequency of other
components. Improve the rigidity of the mounting for that equipment or
remove that item from the table.
4.
Non-level floor may prevent the horizontal isolation system from
functioning properly (see Section 1.5).
Summary of Contents for IPV
Page 2: ...ii...
Page 22: ...16 Figure 13 Double Bolt Tightening Sequence...
Page 32: ...INSTRUCTION MANUAL Vibration Control System...
Page 39: ...viii...
Page 63: ...24...
Page 64: ...25...