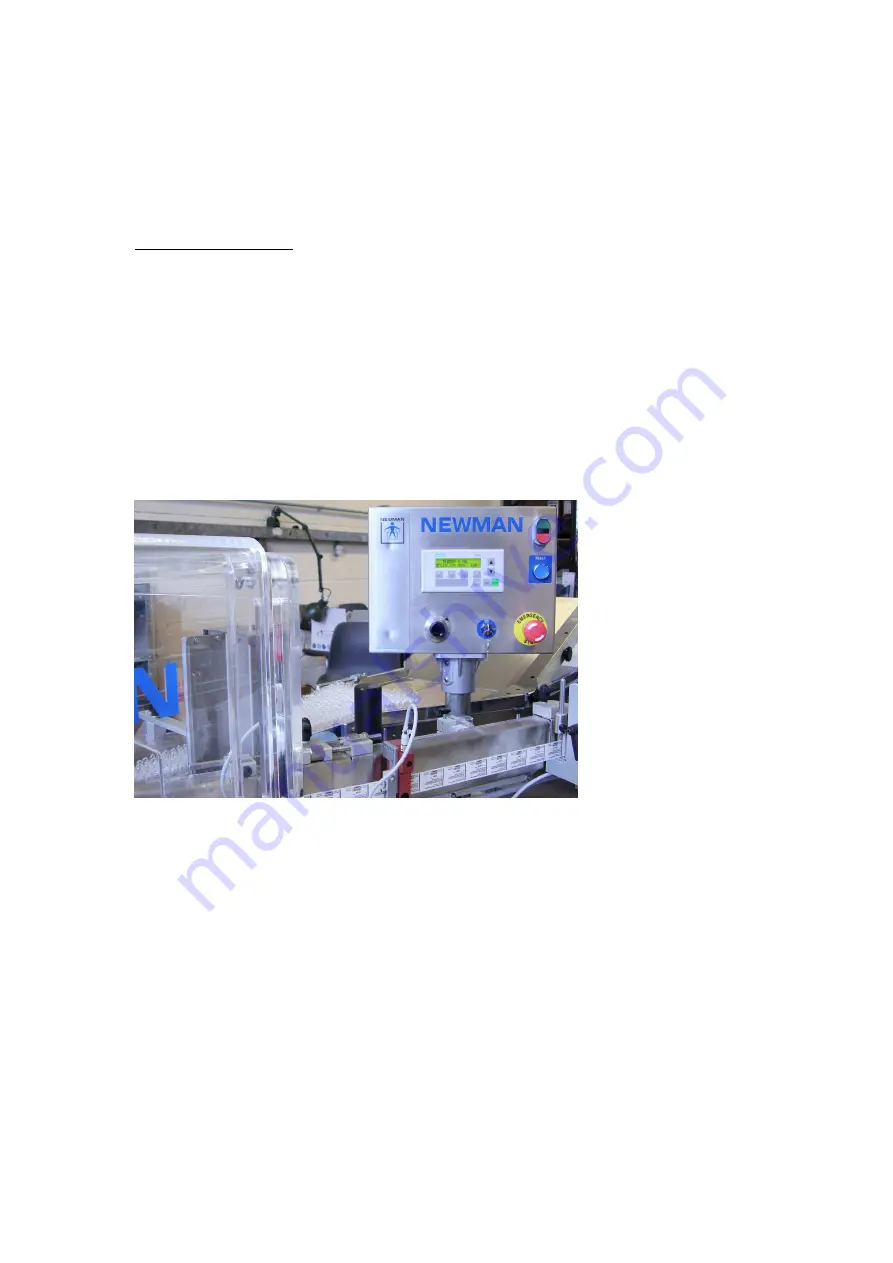
4VAL Operating & Maintenance Manual Version 1.1 © Newman Labelling Systems Ltd Page 12 of 56
Documented training with certificates for all attendees along with course
documentation is increasingly being requested and Newman is able to quote and
provide this service. Please contact Newman for further information.
2.3 INSTALLATION
Prior to starting Installation it is important to fully understand the following
instructions. Unpack the machine very carefully to avoid damage and make sure that
all small items and boxes are retained before discarding the packaging. Screw in the
four adjustable feet (or castors), move the machine into position, set the conveyor
height and level machine by adjusting the feet.
The Operator Panel has been lowered to approximately guard level for transport
purposes as shown in photo below. This needs to be raised to a suitable height for
operation. Ensure that one person supports the box before another person releases the
clamp to raise the box.
Operator panel lowered for shipment
Reassemble the coder (if fitted) to the machine and connect the pneumatic and
electrical services. The coder is usually secured onto the label arm mounting bracket
with 4 off M6 socket head screws.
Check that your electrical supply details correspond with those on the machine plate
and machine electrical drawings. Ensure that a suitably qualified person connects the
supply to the isolator. If your supply uses an earth leakage circuit breaker (ELCB) /
residual current device (RCD) it is recommended to be 100mA minimum trip rating.
The machine is supplied with all guards necessary for safe operation. If any
modifications are made for any reason, care should be taken to ensure that the overall
safety is not impaired.