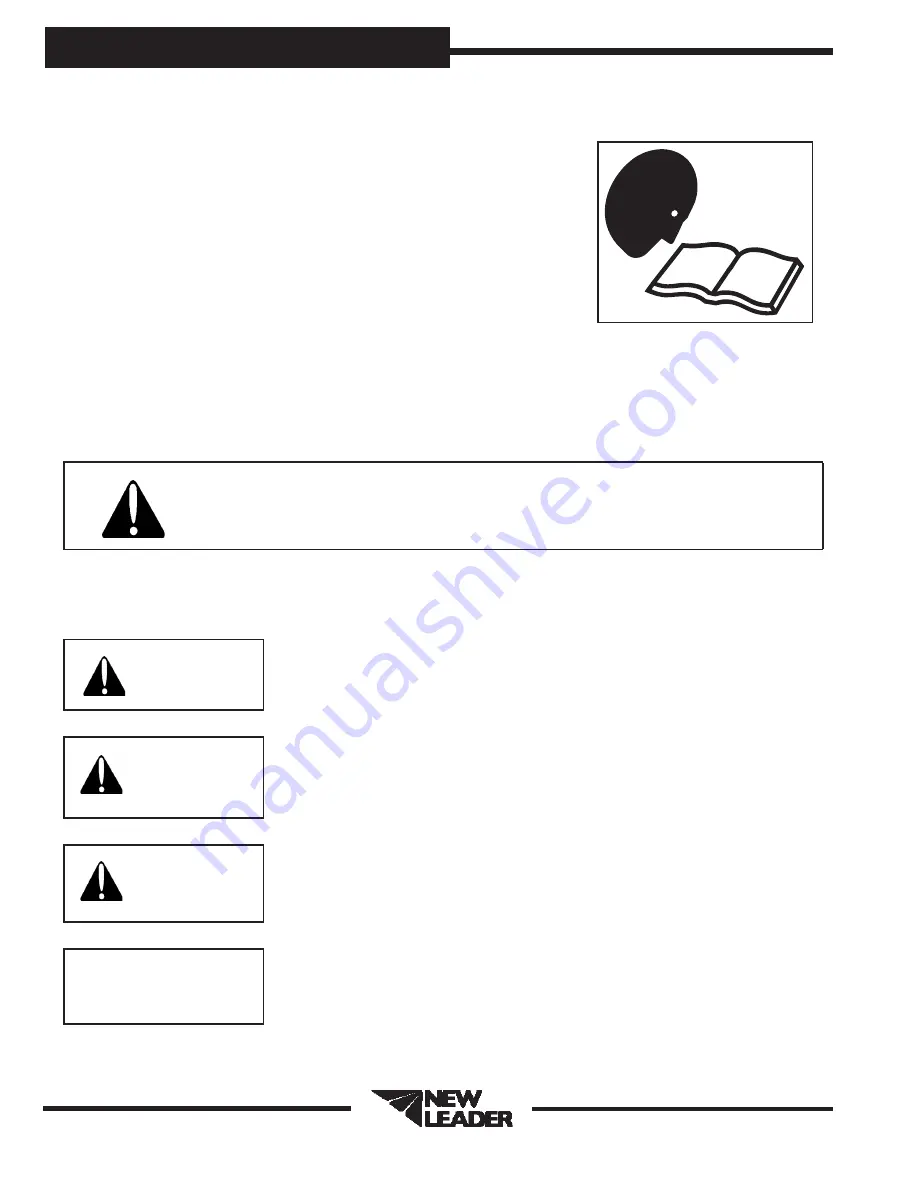
- 8 -
www.NewLeader.com
(800) 363-1771
312884-AA-C
NL345
Safety
Important Safety Information
Figure 1�1 - The need for safety cannot be stressed strongly enough
in this manual� At New Leader Manufacturing, we urge you to make
safety your top priority when operating any equipment. We firmly
advise that anyone allowed to operate this machine carefully read,
learn and understand all messages and information in this manual
and on machine’s safety decals before operating machine, as well as
familiarize themselves with the location and function of all machine
controls�
The following guidelines are intended to cover general usage and to
assist you in avoiding accidents� There will be times when you will
run into situations that are not covered in this section� At those times
the best standard to use is common sense� If, at any time, you have
a question concerning these guidelines, please call your authorized
dealer or our Product Sales & Support Department at (800) 363-1771�
Figure 1�1
Safety Alert Symbols
TAKE NOTE! THIS SAFETY ALERT SYMBOL FOUND THROUGHOUT THIS MANUAL IS
USED TO CALL YOUR ATTENTION TO INSTRUCTIONS INVOLVING YOUR PERSONAL
SAFETY AND THAT OF OTHERS� FAILURE TO FOLLOW THESE INSTRUCTIONS CAN
RESULT IN INJURY OR DEATH�
In this manual and on the safety signs placed on the unit, the words “DANGER,” “WARNING,” “CAUTION,”
and “NOTICE” are used to indicate the following:
Indicates an imminently hazardous situation that, if not avoided, WILL
result in death or serious injury� This signal word is to be limited to the
most extreme situations and typically for machine components that, for
functional purposes, cannot be guarded�
DANGER
Indicates a potentially hazardous situation that, if not avoided, COULD
result in death or serious injury, and includes hazards that are exposed
when guards are removed� It may also be used to alert against unsafe
practices�
WARNING
Indicates a potentially hazardous situation that, if not avoided, MAY result
in minor or moderate injury� It may also be used to alert against unsafe
practices�
CAUTION
NOTICE!
Is used for informational purposes in areas which may involve damage or
deterioration to equipment but generally would not involve the potential
for personal injury�
NOTE:
Provides additional information to simplify a procedure or clarify a process�
Summary of Contents for NL345/MULTAPPLIER
Page 6: ...Insert Current New Leader Warranty Warranty...
Page 26: ...26 www NewLeader com 800 363 1771 312884 AA C NL345 Informational Decals 1 1...
Page 86: ...86 www NewLeader com 800 363 1771 312884 AA C NL345 Header Hydraulic Schematic TR3000 Brakes...
Page 114: ...114 www NewLeader com 800 363 1771 312884 AA C NL345 Notes This Page Intentionally Left Blank...