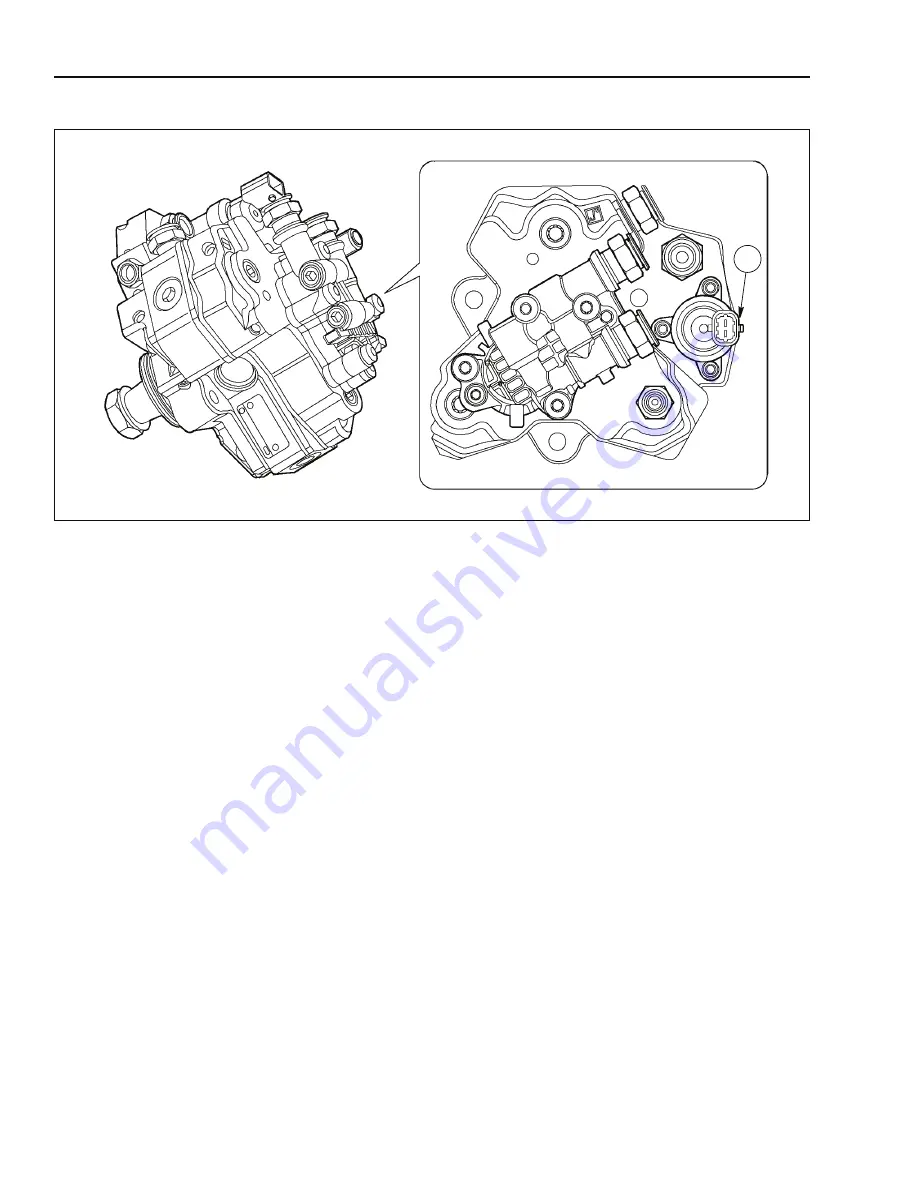
2-66
Issued 11-06
Bur
87519804 NA
CHAPTER 2 - 667TA ENGINE OVERHAUL
ENGINE REPAIR MANUAL
HIGH PRESSURE PUMP - PRESSURE REGULATOR
BS06K212
Figure 2-86
A. PRESSURE REGULATOR
The quantity of fuel supplied to the high pressure
pump is controlled by the supply pressure regulator
solenoid valve. The high pressure regulator is
controlled by the EDC7UC31 control unit.
Delivery pressure to the common rail is modulated
between 250 and 1600 bar (3626 and 23206 psi) by
the EDC7UC31 control unit by controlling the high
pressure regulator solenoid valve.
•
This component is a Normally Open solenoid
valve.
•
The solenoid is connected to the EDC7UC31
control unit on pins 9A - 10A.
•
The solenoid valve impedance is approximately
3.2 ohms.
A
Summary of Contents for 667TA/EBF
Page 4: ...SECTION 1 ENGINE REPAIR MANUAL II Issued 11 06 Bur 87519804 NA NOTES ...
Page 8: ...1 2 Issued 11 06 Bur 87519804 NA CHAPTER 1 DIAGNOSTICS ENGINE REPAIR MANUAL NOTES ...
Page 16: ...1 10 Issued 11 06 Bur 87519804 NA CHAPTER 1 DIAGNOSTICS ENGINE REPAIR MANUAL NOTES ...
Page 22: ...2 4 Issued 11 06 Bur 87519804 NA CHAPTER 2 667TA ENGINE OVERHAUL ENGINE REPAIR MANUAL NOTES ...
Page 144: ...3 2 Issued 11 06 Bur 87519804 NA CHAPTER 3 CHARGING AND START UP ENGINE REPAIR MANUAL NOTES ...
Page 150: ...3 8 Issued 11 06 Bur 87519804 NA CHAPTER 3 CHARGING AND START UP ENGINE REPAIR MANUAL NOTES ...