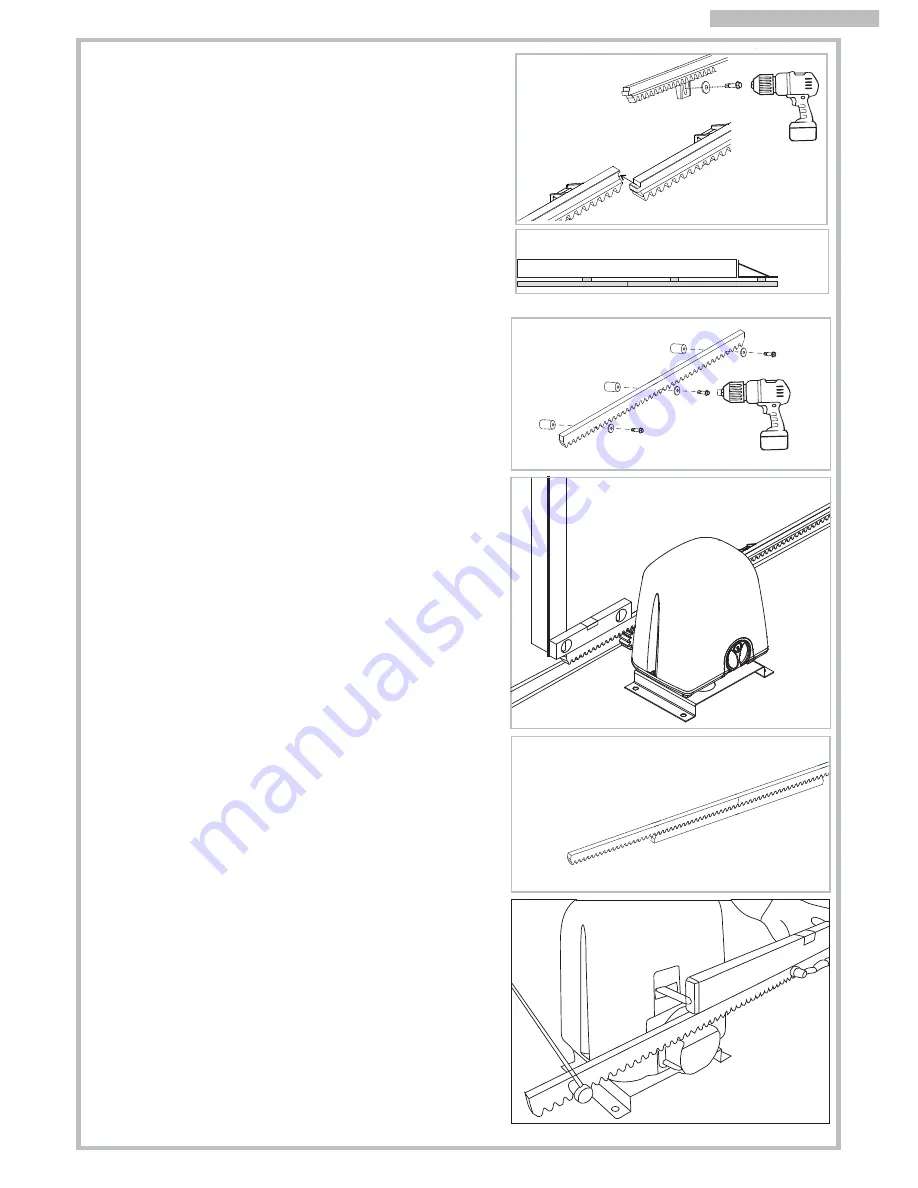
Fig. 8
Fig. 9
Fig. 10
Fig. 11
Fig. 11a
Fig. 7a
6
e) Keep the rack perfectly flat and fix it to the gate.
f) Repeat the same procedure until the gate is fully covered.
g) In case the last section of rack partially comes out from the
rack edge, do not cut it. Add a bracket as a gate extension
to support the last bit of rack (Fig. 8).
h) To avoid the gates weight being supported by the motors
drive pinion cog, adjust the four screws to lower a little the
gear motor and then tighten again all the nuts.
3.6.2 WELDING METAL TOOTHED RACK B102 –
STEEL RACK M4 12X30MM (1M SECTIONS)
a) Move the gate manually to its open position.
b) Assemble the three threaded stand-offs on the first section of
rack, positioning in the middle of the slot (Fig. 9).
c) Align the first section of the rack to the gates edge and lower
it on the pinion. Use a spirit-level to ensure the rack is
perfectly straight and level.
d) Weld the threaded stand-off to the gate (Fig. 10)
e) Move the gate manually, checking that the rack is always
resting on the motors drive pinion cog, and weld second
and third stand-offs.
f) Place the second section of rack side by side with the first
one, using an upside-down section of rack to synchronise
the rack teeth as illustrated in Fig. 11.
g) Move the gate manually and weld the three threaded
stand-offs.
h) Repeat the same procedure until the gate is fully covered.
i) In case the last section of rack partially comes out from the
rack edge, do not cut it. Add a bracket as a gate extension
to support the last bit of rack (Fig.8).
j) To avoid the gates weight being supported by the motors
drive pinion cog, adjust the four screws to lower a little the
gear motor and then tighten again all the nuts.
Check the gate always reaches the mechanical
stops keeping the alignment between the rack and
the motor drive pinion cog. Ensure that there are no
friction points in the gates complete travel.
ENGLISH