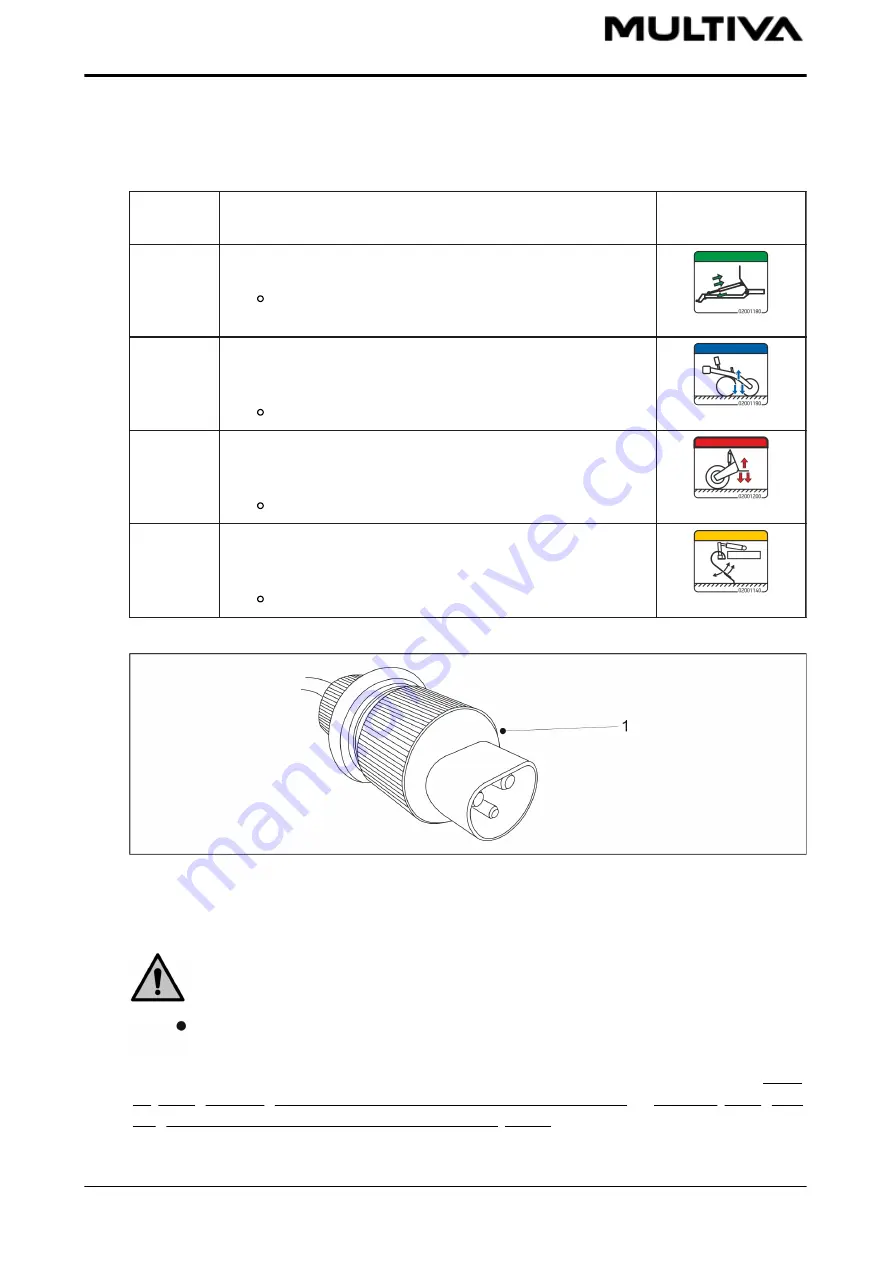
Number
Hydraulic hose
Colour code and
symbol
1.
Drawbar adjustment connection
2 male connectors of ½”
2.
Hydraulic connection of the coulter pressure
adjustment
2 male connectors of ½”
3.
Hydraulic connection for raising the machine to the
transport position
2 male connectors of ½”
4.
Hydraulic connection of the adjustment of the front
levelling board position
2 male connectors of ½”
Figure. 5.3. - 61. Comfort controller power cable DIN 9680
6. If the machine is equipped with a Comfort control system, plug the controller power
cable (1) into the tractor cabin plug.
DANGER
Ensure that the tractor is turned off and the key is removed from the ignition.
Ensure the cable is not crushed by the tractor's rear window. Fasten the cable
properly so that it is not pinched during turns or lifting.
7. If necessary, straighten the machine according to the instructions in section 5.3.3.
Adjusting the lengthwise level of the machine with a turnbuckle or 5.3.4. Adjusting the
lengthwise level of the machine with a drawbar cylinder.
Operation and maintenance manual
Cerex 300 and Cerex 400 Comfort
1.00
60 (187)
Summary of Contents for Cerex 300 Comfort
Page 179: ...Hydraulic schematics Cerex 300 and Cerex 400 1 Hydraulic schematics Cerex 300...
Page 180: ...Hydraulic schematics Cerex 300 and Cerex 400 2...
Page 181: ...Hydraulic schematics Cerex 300 and Cerex 400 3 Hydraulic schematics Cerex 400...
Page 182: ...Hydraulic schematics Cerex 300 and Cerex 400 4...
Page 183: ...Electrical schematics Cerex 300 and Cerex 400 Comfort 1 Electrical schematics...
Page 184: ...Electrical schematics Cerex 300 and Cerex 400 Comfort 2...
Page 185: ...Electrical schematics Cerex 300 and Cerex 400 Comfort 3...