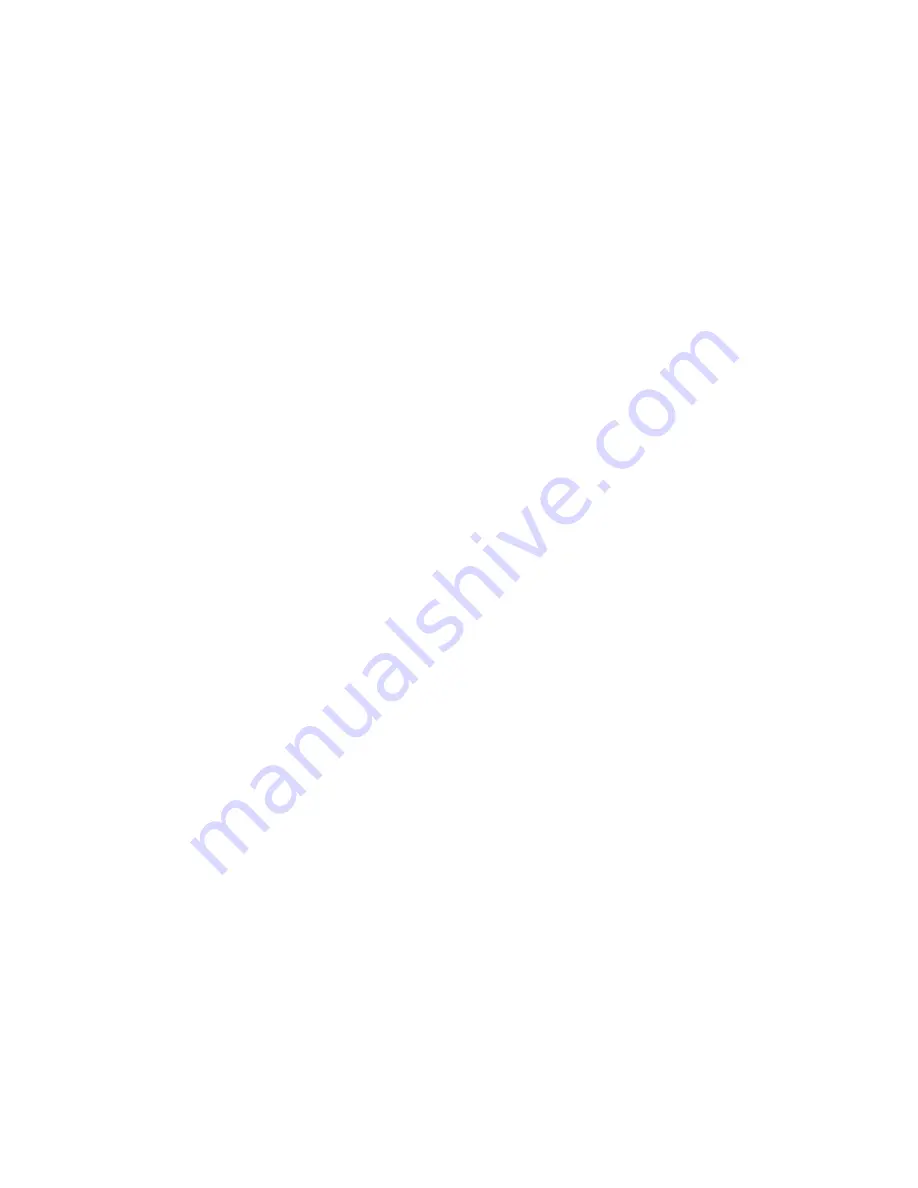
Operation
MTS Landmark™ Tabletop Load Units - Product Information
81
Additional Station Manager and Interlock Functionality
(Units equipped with electromagnetic rotary servo
motor only)
Units equipped with an electromagnetic servo motor have additional functionality not found on other
units.
When the operator puts the load frame in the actuator velocity limiting mode (indicated by the turtle
symbol), the servo motor HSM is triggered in Station Manager to power off the servo motor and set an
interlock. This allows the operator to install or adjust a specimen without power to the servo motor. In
addition, this functionality also sets the Station Manager actuator angle to the current location. This
prevents the actuator from returning to its original position when the interlocks are reset and power is
restored to the servo motor.