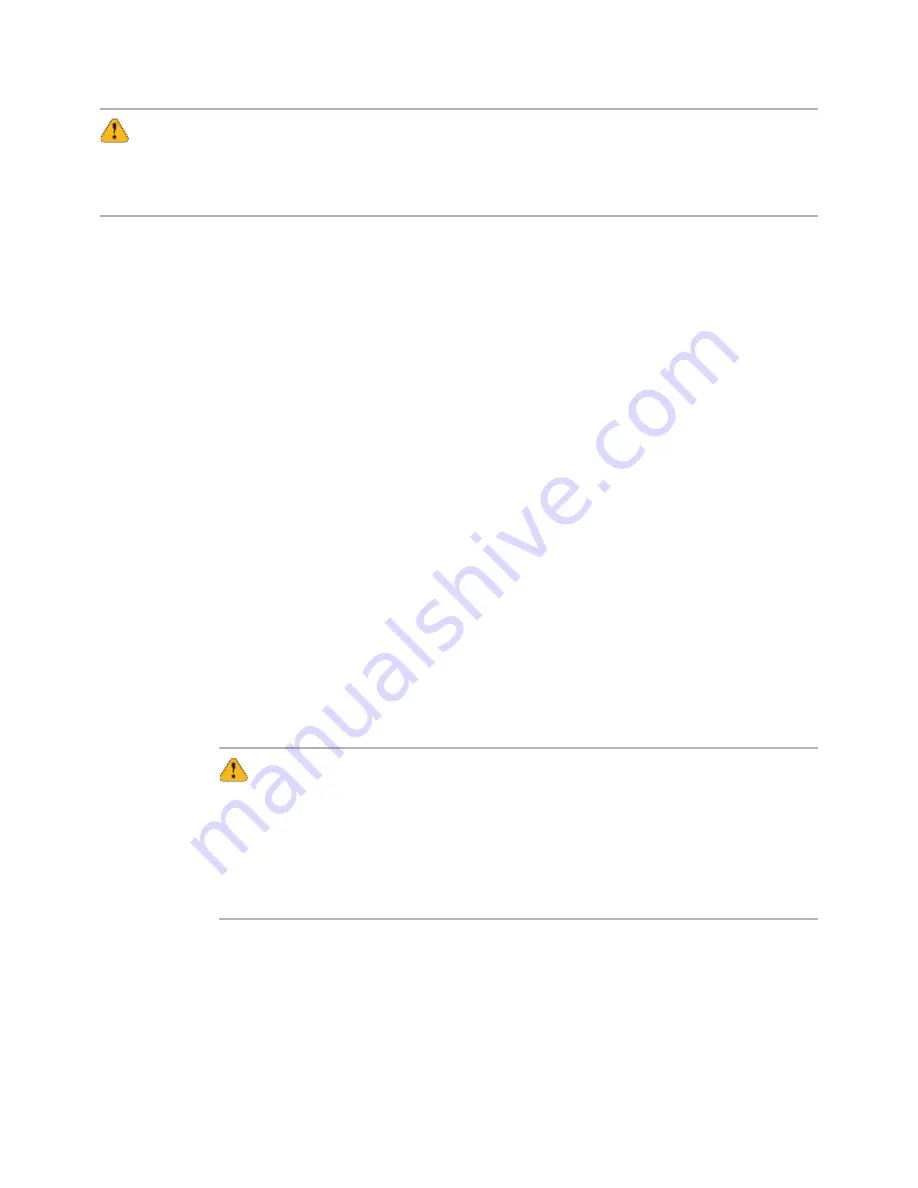
Maintenance
MTS Landmark™ Tabletop Load Units - Product Information
119
Do not perform the following procedure without clearing the path of motion of the actuator.
Ensure that all personnel, specimen/structures, and tools are away from the path of motion of
the actuator (crush zone).
1. Exercise the actuator.
The actuator should be exercised to warm it up. Electrical and mechanical adjustments are
more repeatable after the actuator is warmed up.
A. Select displacement control for the controller.
B. Disable the reset integrator or adjust the Reset control for zero.
C. Adjust the actuator for mid-displacement.
D. Turn on electrical and hydraulic system power.
E. Define a 50%, 0.1 Hz sine wave command and allow the actuator to warm up for
approximately one-half hour.
F. After the warmup period, stop the test program.
2. Check for actuator movement to determine how to proceed.
Disconnect the servovalve cable and observe the actuator rod.
l
If the actuator rod has no noticeable movement, the servovalve is at the null position
and does not need to be adjusted. Proceed to Step 4.
l
If the actuator rod noticeably moves, the servovalve requires adjustment. Proceed to
Step 3.
3. Set the adjuster pin.
This task describes the mechanical null adjustment procedure.
A. Insert a 3/32-inch hex key into the adjustor pin socket. For the location of the adjustor
pin, see the following figure.
Caution:
Excessive torquing may shear off the adjustor pin eccentric.
Do not apply more than 12 lbf-in. (1.36 N•m) of torquing force to the
adjustor pin.
If the pin does not turn using very little force, proceed to Step C of this task.
B. Slowly rotate the adjustor pin until the actuator movement is reduced to a minimum,
and then go back to Step 2. If the pin does not turn using very little force, proceed to
the next step.
C. Reduce system pressure to low pressure (refer to the appropriate controlling device
product manual). Slowly rotate the adjustor pin until the actuator movement is