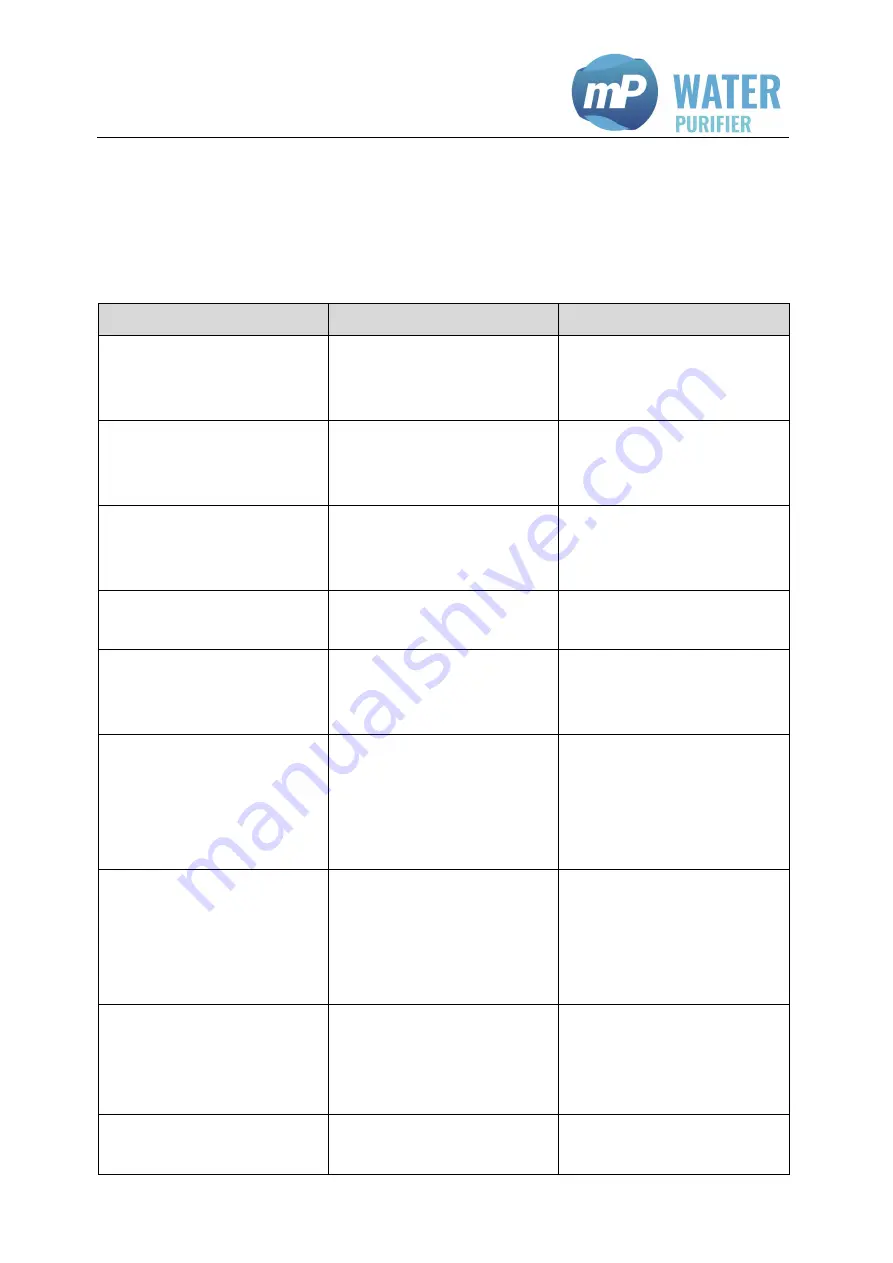
Errors and Countermeasures
27
Errors and Countermeasures
6
Display warning messages, their meanings and measures in order to eliminate them. If
these measure do not contribute to elimination contact the customer service.
Trouble
Reason
Measure
(2) OPERATING HOUR
LIMIT P1, Exchange
recommended
The Reverse osmosis pump
exceeded the maximum
operating hours.
Inform the customer service.
(4) OPERATING HOUR LIMIT
P2, Exchange recommended
The Circulation pump
exceeded the maximum
operating hours.
Inform the customer service.
(5) OPERATING HOUR LIMIT
UPW-Pak. Exchange
recommended
The UPW-Pak exceeded the
maximum operating hours.
Replace the polisher module
UPW-Pak. Reset the expired
operating hours.
(6) Please change UV lamp
The UV lamp exceeded the
maximum operating hours.
Replace the UV lamp. Reset
the expired operating hours.
(8) Pump P1 error: Check
pressure sensor!
No reverse osmosis-
pressure can be registered
for more than a half hour.
Check the main water supply
Inform the customer service.
(11) Q1 is over limit! Check
RO process.
The feed water quality is
insufficient. ProPak-R10
(Pretreatment module )
exhausted. Reverse osmosis
function.
Check pretreatment.
Replace the ProPak-R10
(pretreatment module).
Inform the customer service.
(12) Water level is too low!
The Product water tank is
empty.
Wait for tank filling. Check
the feed water supply. Check
the system for leaks. Check
the function of the RO
process.
(15) Warning: T3 is over
40°C!
The system temperature
caused by UV lamp or
recirculation pump is too
high.
Check Interval-Mode. Check
the temperature of the
environment and the feed
water.
(17) Warning Q3 is over limit! Q3 exceeds the limit.
Replace UPW-Pack.
Reset the expired operating