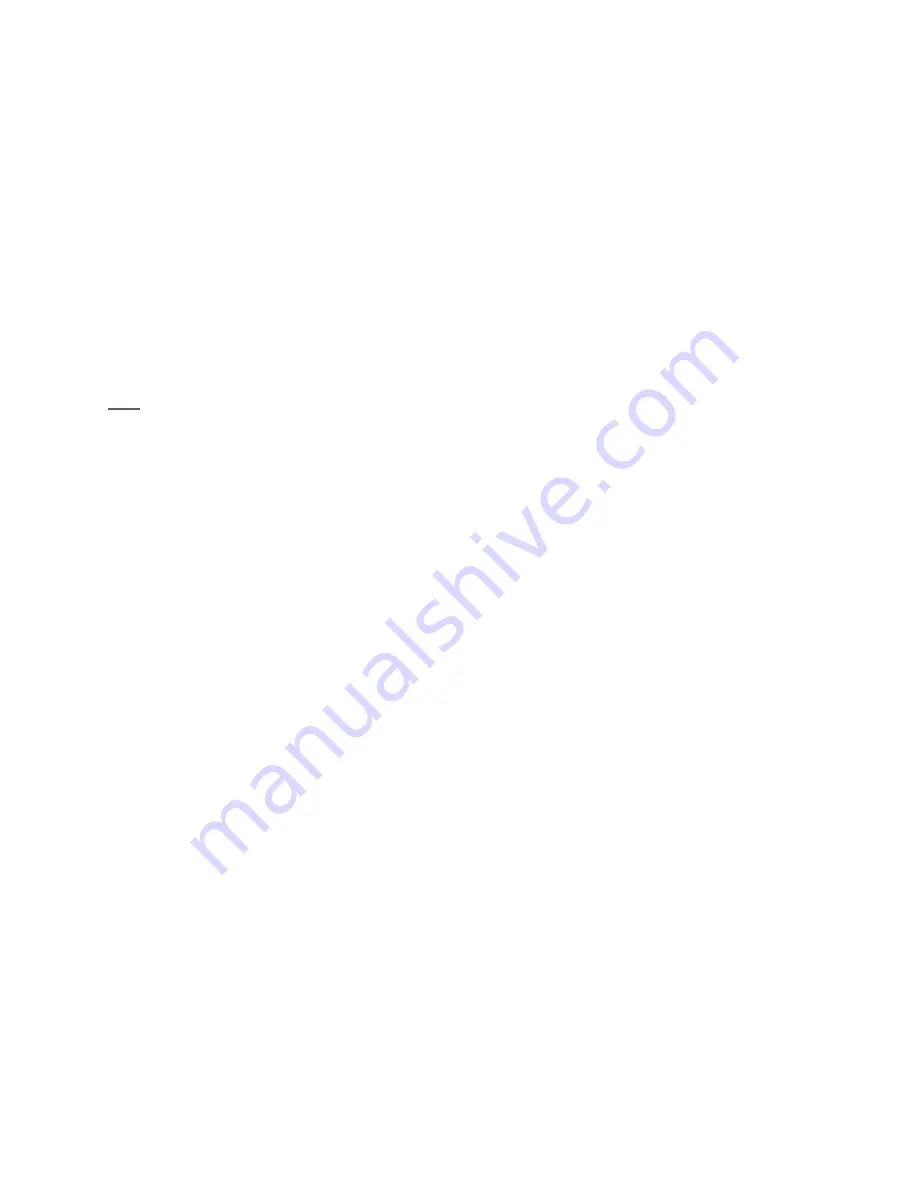
7
3.1.
Features & Benefits
▪
High pressure coolant when properly applied can save considerable time per cycle,
dramatically improve tool life, and remove many of the requirements for operator
intervention.
▪
Cutting operations that suffer from chip evacuation problems can see improved speed,
accuracy, surface finish and reliability when using the R Series high pressure system.
▪
In problem holes, high pressure can allow for higher speeds and higher feed rates, with
little to no pecking. This allows for 5-20% faster drilling.
▪
Coolant fed reamers & boring tools, either through tool or close nozzle, can greatly
improve finish, tool life and accuracy.
▪
In severe milling applications, the improvements will be easily recognized through the
lack of re-cutting of chips.
▪
Heavy cuts can be made far more reliably with high pressure coolant. Tools that smoke
or burn will see tool life greatly improved. This allows for much ‘heavier’ cuts with tools
that can be pushed much harder, greatly improving cycle times.
▪
Jobs already being run with ‘flood’ coolant will see dramatic increase in productivity with
high pressure coolant.
▪
Often, time consuming programing methods such as rough/finish cuts, interrupted feed,
non-optimum tool and feed speeds can be eliminated with the use of high pressure
coolant. High pressure coolant gives the ability to break and/or control the chips that
typically cause slow speeds.
▪
Rings of material left on drills and boring bars can be blown off with high pressure
coolant.
▪
Coolant through sub spindle can stop miss chucking and reduce parts being marked by
chips left in the collet.
Summary of Contents for V Series
Page 6: ......
Page 17: ...11 5 Floor Layout ...
Page 29: ...23 ...
Page 39: ...33 11 1 Relief Valve Identifier ...
Page 44: ......
Page 45: ...1 ...
Page 46: ......