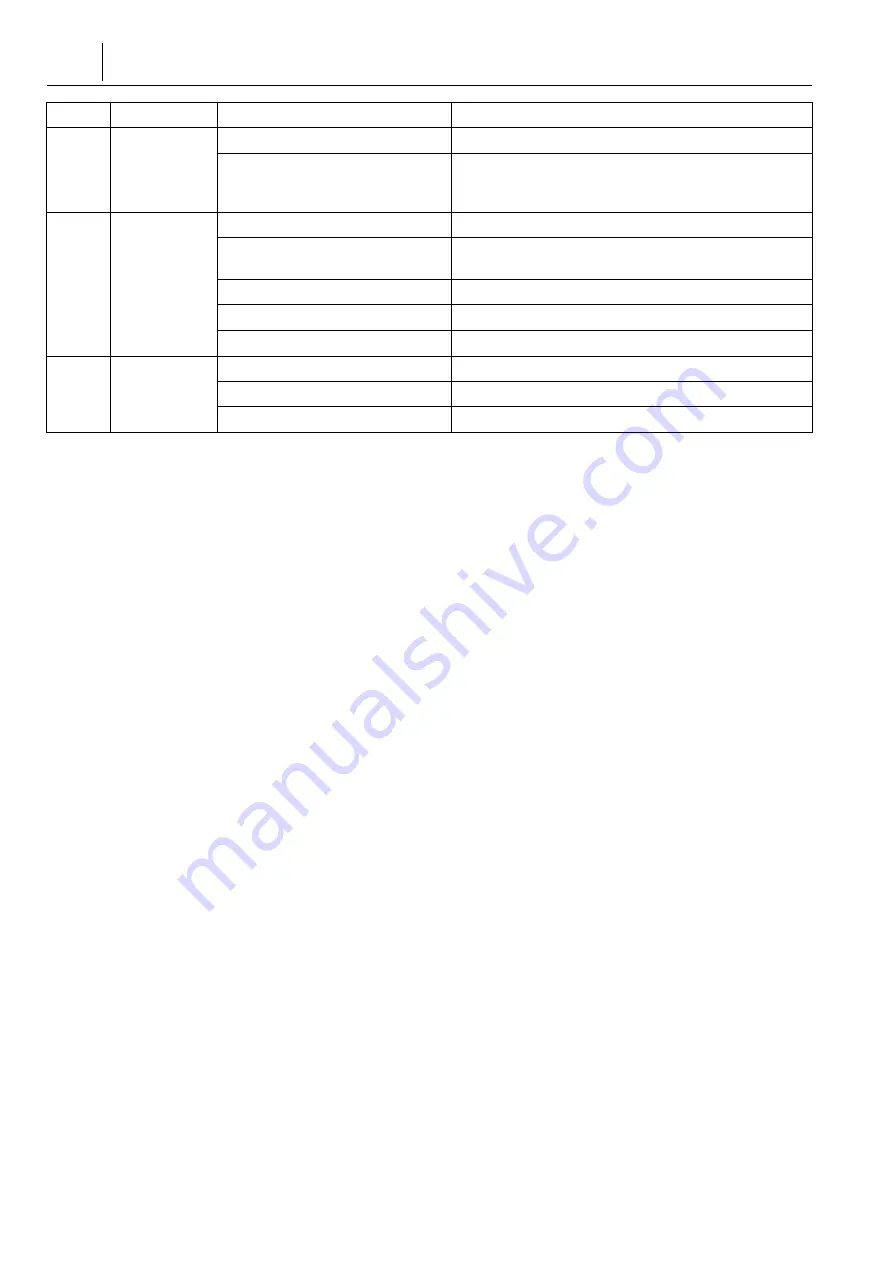
บ٢ʰʕʍʒɁႱࢠ
HYDRAULIC UNIT ALARMS
194
2
Pressure
fluctuation
Air entry into piping
Item 4
Pressure gage reading abnormal
Item 1
When necessary to replace the pressure gage, contact the
Mori Seiki Service Department for assistance.
3
Abnormal
noise
generated
Hydraulic oil viscosity inappropriate
Low oil level in tank
“Checking Oil Level/Replenishing Oil” (page 94),
“Replacing Oil” (page 94)
Suction strainer clogging
“Cleaning Suction Strainer and Tank” (page 96)
Pressure fluctuation
Item 2
Pump component damage/wearing
Contact the Mori Seiki Service Department for assistance.
4
Oil leakage
Oil leakage from connections
Tighten connections.
Hose deterioration, damage
Contact the Mori Seiki Service Department for assistance.
Oil leakage from pump
Contact the Mori Seiki Service Department for assistance.
Item
Status
Cause
Reference Items/Recovery Procedures
Summary of Contents for NL1500/500
Page 8: ......
Page 9: ...CONTENTS FOR SAFE MACHINE OPERATION REGULAR MAINTENANCE TROUBLESHOOTING INDEX...
Page 10: ......
Page 19: ...FOR SAFE MACHINE OPERATION...
Page 50: ......
Page 51: ...1 1 CHAPTER 1 CHAPTER 1 REGULAR MAINTENANCE...
Page 167: ...2 2 CHAPTER 2 CHAPTER 2 TROUBLESHOOTING...
Page 181: ...181 ZERO POINT RETURN COMMAND ALARM TRIGGERED X X Axis Z Z Axis Y Y Axis...
Page 232: ......
Page 240: ......
Page 242: ......