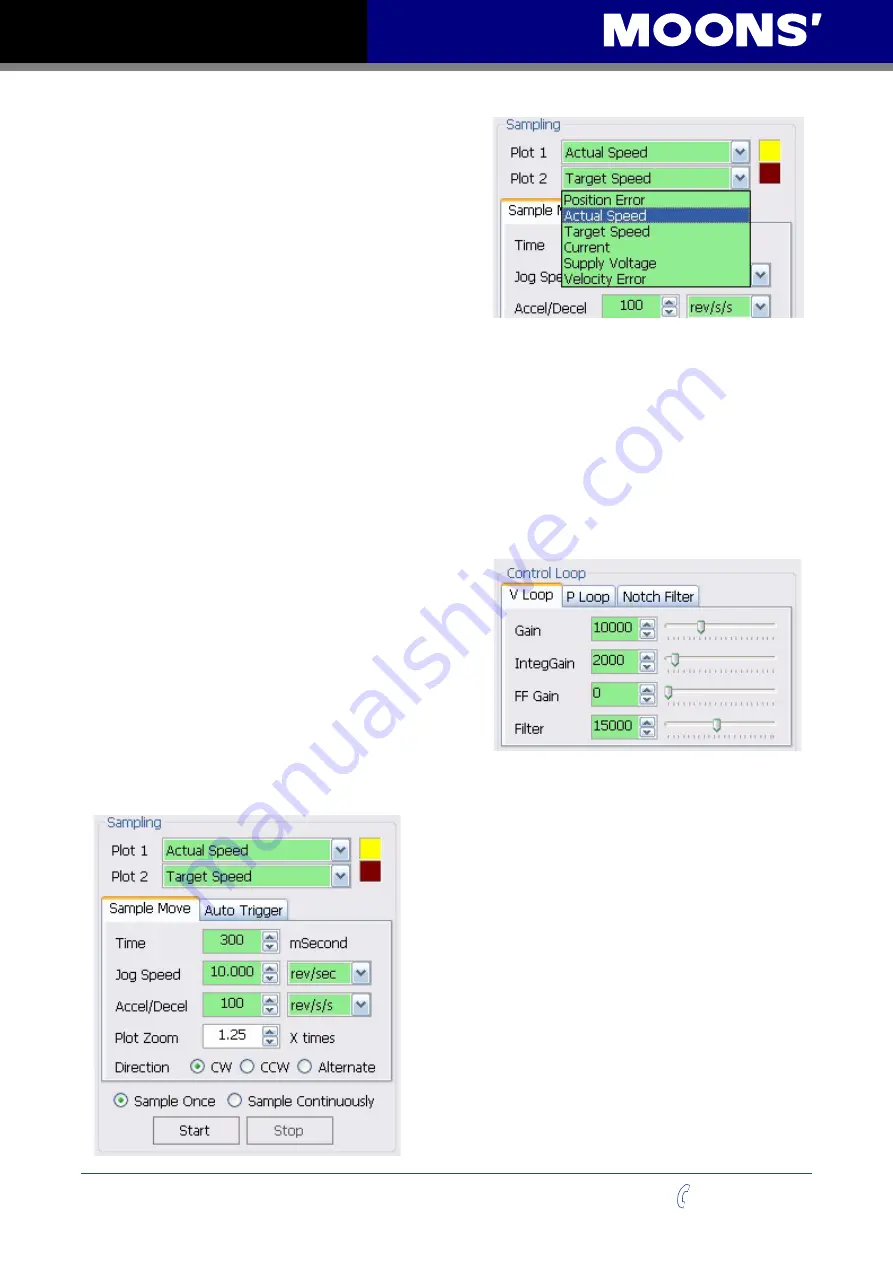
32
Rev. 1.0
0006302011
SSM23C User Manual
+86-400-820-9661
The mechanical system should be set up as close
to the final configuration as possible so that the
tuning represents what will be expected. The
critical components include the coupler, mechanical
interface ,and similar frictional and inertial loads. As
tuning can sometimes be an uncontrolled process
where the mechanical system can be damaged, care
must be taken to minimize this possibility. This could
include having limit sensors or mechanical stops that
help to prevent such damage.
SSM Quick Tuner contains a sampling Oscilloscope that will display of variety of measurements of
an executed move. Two plots can be displayed at one time and contain the real-time information
about the move performance. Before performing the test move, make sure the desired move
information is selected. This can include the typical information such as
Actual Speed
or
Position
Error
but also can include the
Supply Voltage
so that the power supply can be monitored for
proper voltage during the move.
5.5 Tuning the Velocity Loop
5.5.1 Entering a Sample Move
Start by selecting the
V Loop
tab in the
Control
Loop
dialog section. This will cause the
Sampling
to
perform moves that are based on
Time
and operates
the drive in the
Speed Only
Velocity mode.
Now parameters may be entered for a
Velocity
based move.
Plot 1 & Plot 2:
two different values can be selected
for viewing in the scope window, in this case
Actual
Speed
and
Velocity Error
are selected. These are typical values for Velocity tuning.
Sample Move:
move profile values are entered in
the
Sample Move
section. This example sets a move
Time
of 200ms at a
Jog
Speed
of 20 rev/sec and an
Accel/Decel
rate of 300 rev/s/s. In the window to the
right of the
Sampling
data entry section the
Desired
Profile
will be displayed. This provides a visual
reference of what the expected move will look like.
Plot Zoom:
the length of the plot values that are
displayed can be set from 1 to 5 times the profile
length.
Dir:
the direction of the move can be set to
cw
,
ccw
or
alternate
. These directions refer to the motor
shaft as viewed from the front of the motor.
Alternate
toggles the direction after each move. Start with a
known direction before switching to toggle.