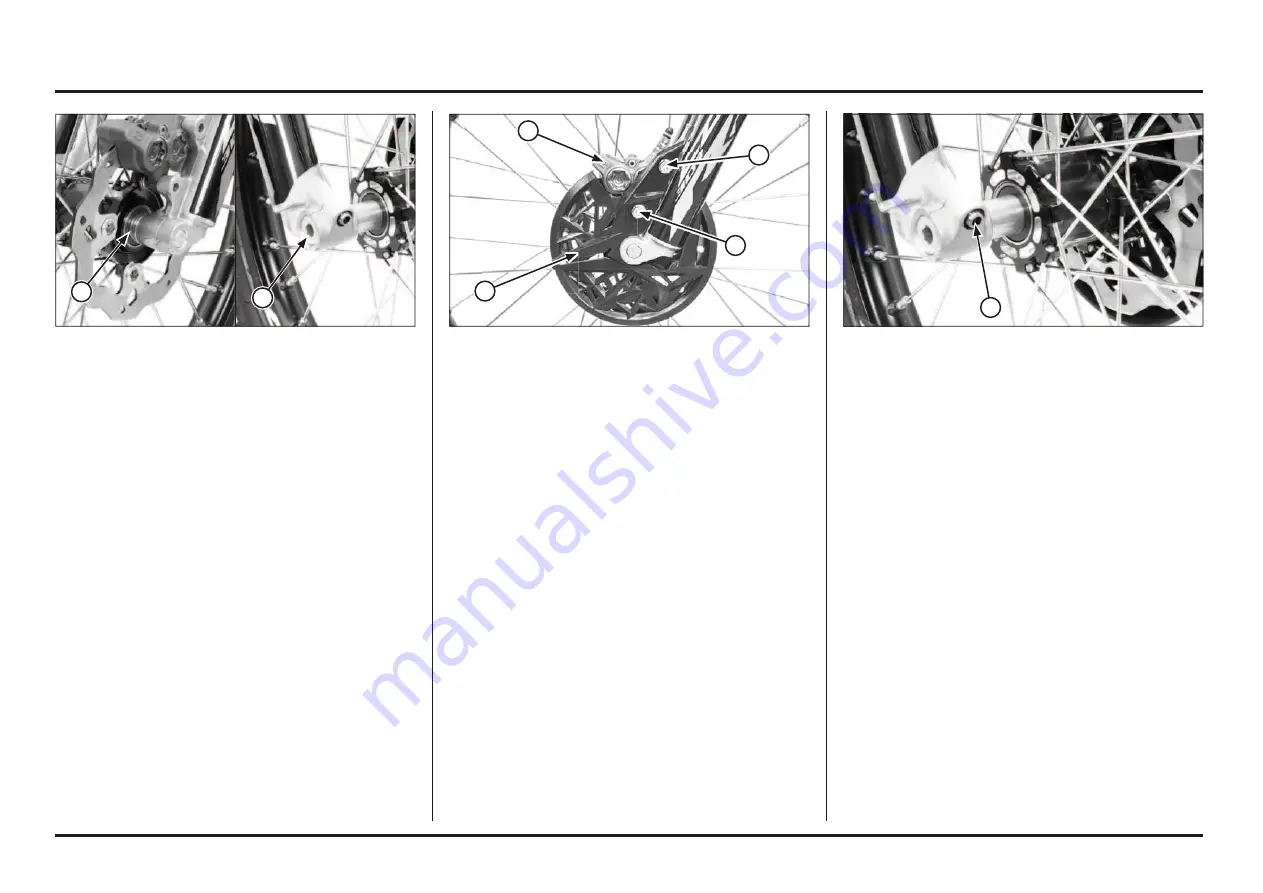
5-2
5-2
Frame servicing
(1) SIDE COLLAR
(2) AXLE
INSTALLATION
Clean the surfaces where the axle and axle clamps con-
tact each other.
Place the front wheel between the fork legs.
Apply thin layer of grease to the axle surface.
Apply grease to the axle threads.
Install the axle from the right side through the wheel and
left side collar.
Tighten the axle to the specified torque.
Torque: 69 N•m (7.0 kgf•m, 51 lbf•ft)
(1) BRAKE CALIPER
(2) DISC COVER
(3) BOLTS
Install the brake caliper, flange collars and disc cover.
Apply a locking agent to the threads and tighten the mou-
nting bolts to the specified torque.
Torque: 26 N•m (2.7 kgf•m, 20 lbf•ft)
With the front brake applied, pump the fork up and down
several times to seat the axle and check the front brake
operation.
(1) AXLE PINCH BOLTS
While keeping the fork parallel, tighten the axle pinch bolt
to the specified torque.
Torque: 23 N•m (2,3 kgf•m, 17 lbf•ft)
2
1
1
1
2
3
3
Summary of Contents for COTA 301RR 2023
Page 1: ...PGM FI Racing Trial Owner s Manual 2023...
Page 6: ...Labels ED 2ED 3 2 1 6...
Page 7: ...Labels 3ED 4ED 4 2 1 7 3 5...
Page 11: ...Memo Memo...
Page 43: ...Service data 2 20 2 20 1 FUEL FEED HOSE 2 TRANSMISSION BREATHER HOSE 1 2...
Page 63: ...3 20 3 20 Memo...
Page 125: ...4 62 4 62 Memo...
Page 175: ...6 20 6 20 Memo...
Page 179: ...7 6 7 6 Memo...
Page 180: ...Printed in Spain 62NN4TREMH...