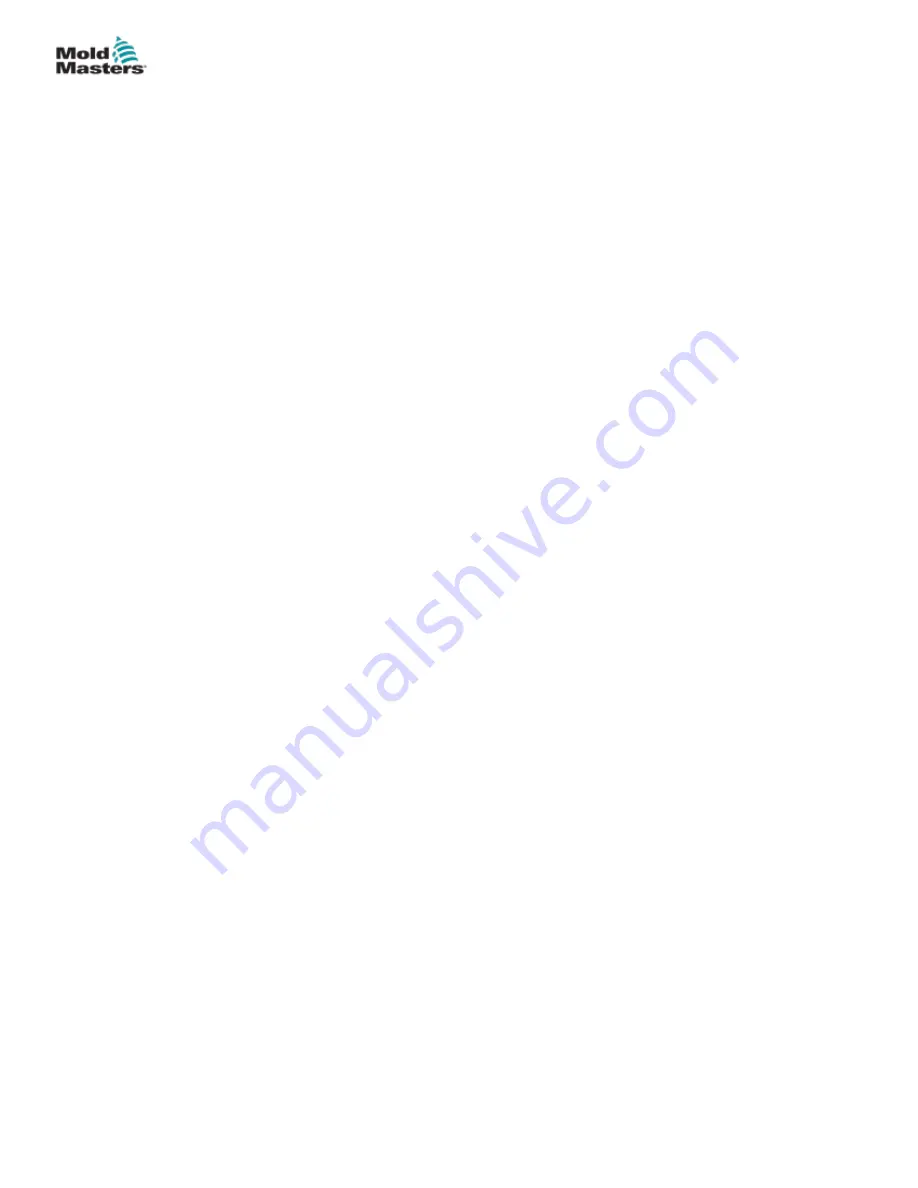
3.
Back off the machine barrel, introduce the appropriate purge compound
and purge until previous material is cleaned, then introduce new color.
Increase barrel / extruder heats to help flush previous color (see machine
maker recommendations).
4.
Increase injection speed to help flush previous material.
5. Use Hot Runner purging compound (e.g. ASACLEAN™, Dyna-Purge
®
) at
recommended temperatures to further reduce color change time.
6.
Run parts until color has completely flushed through.
7. Continue processing while resetting Hot Runner system temperatures and
injection speed back to normal.
8.
Return all settings to normal and confirm acceptable part quality.
Procedure A: Simple and Effective - continued
9.3 Procedure B: More Comprehensive
1. Empty hopper of existing color and clean thoroughly.
2. Increase Hot Runner system temperature on all zones 20°C (68°F) above
processing temperatures. On
Mold-Masters
controllers, simply push the
boost button to increase temperatures for a pre-determined time and
temperature.
3.
Back off the machine barrel, introduce the appropriate purge compound
and purge until previous material is cleaned, then introduce new color.
Increase barrel / extruder heats to help flush previous color (see machine
maker recommendations).
4.
Increase injection speed to help flush previous material.
5. Use Hot Runner purging compound (e.g. ASACLEAN™, Dyna-Purge
®
) at
recommended temperatures to further reduce color change time.
6. Run 10 - 15 shots with natural material.
7.
Back off the injection unit and switch off all heat on the Hot Runner.
8. Allow the Hot Runner system to cool down.
9. Latch over cavity plate.
10. Remove and clean gate bubbles.
11. Latch back cavity plate.
9-2
© 2020 Mold-Masters (2007) Limited. All Rights Reserved.
COLOR CHANGE
Hot Runner User Manual
Summary of Contents for Hot Runner
Page 1: ...Hot Runner User Manual Hot Runner User Manual version 31 Original Instructions...
Page 2: ......
Page 95: ......
Page 318: ......