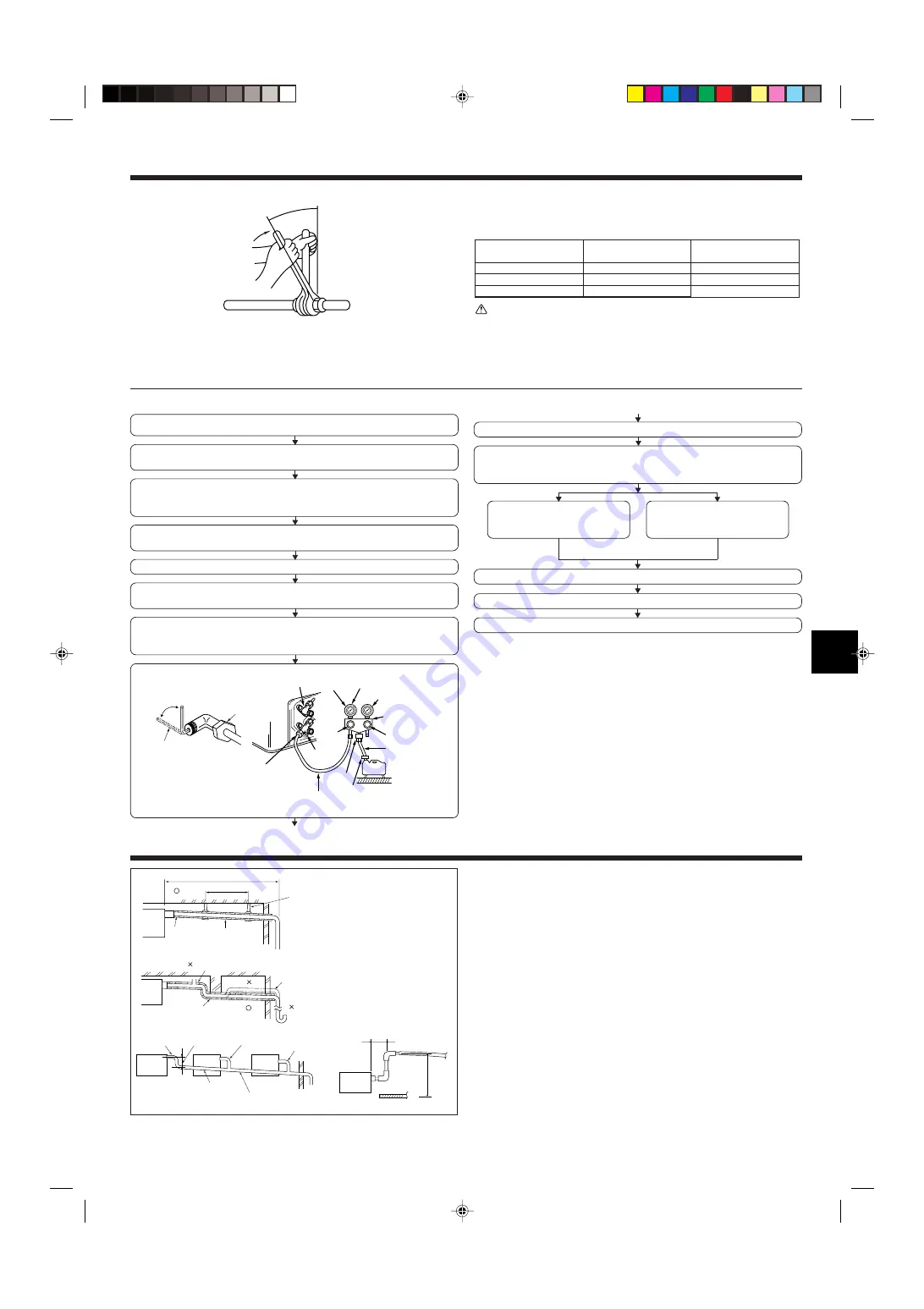
7
• Apply a thin coat of refrigeration oil on the seat surface of pipe. (Fig. 5-10)
• For connection first align the center, then tighten the first 3 to 4 turns of flare nut.
• Use tightening torque table below as a guideline for indoor unit side union joint section,
and tighten using two wrenches. Excessive tightening damages the flare section.
Copper pipe O.D.
Flare nut O.D.
Tightening torque
(mm)
(mm)
(N·m)
ø6.35
17
14 - 18
ø9.52
22
34 - 42
ø12.7
26
49 - 61
Warning:
Be careful of flying flare nut! (Internally pressurized)
Remove the flare nut as follows:
1. Loosen the nut until you hear a hissing noise.
2. Do not remove the nut until the gas has been completely released (i.e., hiss-
ing noise stops).
3. Check that the gas has been completely released, and then remove the nut.
5. Refrigerant piping work
Fig. 5-10
5.5. Purging procedures leak test
PURGING PROCEDURES
Connect the refrigerant pipes (both the liquid and gas pipes) between the indoor
and the outdoor units.
Remove the service port cap of the stop valve on the side of the outdoor unit gas pipe.
(The stop valve will not work in its initial state fresh out of the factory (totally closed
with cap on).)
Connect the gage manifold valve and the vacuum pump to the service port of the
stop valve on the gas pipe side of the outdoor unit.
Run the vacuum pump. (Vacuumize for more than 15 minutes.)
Check the vacuum with the gage manifold valve, then close the gage manifold valve,
and stop the vacuum pump.
Leave it as is for one or two minutes. Make sure the pointer of the gage manifold
valve remains in the same position. Confirm that the pressure gage show -0.101MPa
(-760 mmHg)
Pipe length :
7 m maximum
No gas charge is needed.
Pipe length exceeding 7 m
Charge the prescribed
amount of gas.
Remove the gage manifold valve quickly from the service port of the stop valve.
After refrigerant pipes are connected and evacuated, fully open all stop valves on
gas and liquid pipe sides.
Operating without fully opening lowers the performance and causes trouble.
Tighten the cap to the service port to obtain the initial status.
Retighten the cap
Leak test
*Close
*Open
Hexagonal wrench
Stop valve
*4 to 5 turns
Stop valve
(or the vacuum
pump with the
function to
prevent the back
flow)
Gauge manifold
valve (for R410A)
Pressure gauge
(for R410A)
Compound pressure
gauge (for R410A)
-0.101MPa
(-760 mmHg)
Handle
Low
Handle High
Window
Charge hose
(for R410A)
Vacuum
pump
Adapter for
preventing
the back flow
Charge hose
(for R410A)
Service port
Stop
valve
6. Drainage piping work
Max. 20m
1.5–2m
A
B
C
B
M
L
K
D
E
D
H
I
G
D
F
F
F
Max. 150 mm
J
F
Fig. 6-1
6.1. Drainage piping work (Fig. 6-1)
• Use VP25 (O. D. ø32 PVC TUBE) for drain piping and provide 1/100 or more down-
ward slope.
• Be sure to connect the piping joints using a polyvinyl type adhesive.
• Observe the figure for piping work.
• Use the included drain hose to change the extraction direction.
C
Support metal
K
Air bleeder
L
Raised
M
Odor trap
1
Correct piping
2
Wrong piping
A
Insulation (9 mm or more)
B
Downward slope (1/100 or more)
Grouped piping
D
O. D. ø32 PVC TUBE
E
Make it as large as possible
F
Indoor unit
G
Make the piping size large for grouped piping.
H
Downward slope (1/100 or more)
I
O. D. ø38 PVC TUBE for grouped piping.
(9 mm or more insulation)
J
Up to 500 mm
1
2