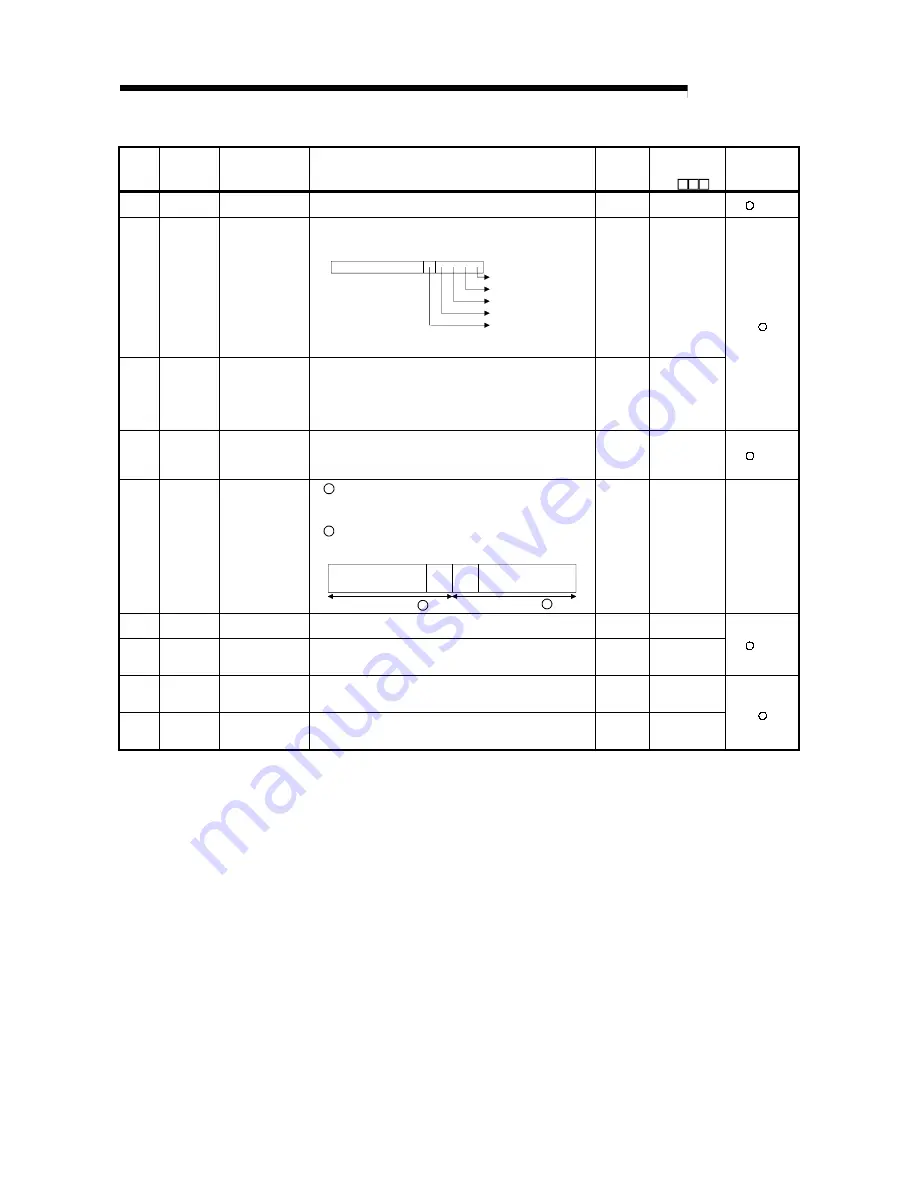
App - 27 App - 27
MELSEC-Q
APPENDICES
Special Register List (Continued)
Number
Name
Meaning
Explanation
Set by
(When set)
Corresponding
ACPU
D9
Corresponding
CPU
SD50
Error reset
Error number that
performs error reset
• Stores error number that performs error reset
U
New
+Rem
SD51
Battery low
latch
Bit pattern
indicating where
battery voltage drop
occurred
• All corresponding bits go ON when battery voltage drops.
• Subsequently, these remain ON even after battery voltage has
been returned to normal.
B4 B3
B0
B2 B1
CPU error
Memory card A alarm
Memory card A error
Memory card B alarm
Memory card B error
0< >
-------------------
• When QCPU is used, this flag is always OFF because memory
card B is used as standard memory.
S (Error)
New
SD52
Battery low
Bit pattern
indicating where
battery voltage drop
occurred
• Same configuration as SD51 above
• Subsequently, goes OFF when battery voltage is restored to
normal.
• When High Performance model QCPU is used, this flag is
always OFF because memory card B is used as standard
memory.
S (Error)
New
SD53
AC/DC
DOWN
detection
Number of times for
AC/DC DOWN
• Every time the input voltage falls to or below 85% (AC
power)/65% (DC power) of the rating during calculation of the
CPU module, the value is incremented by 1 and stored in BIN
code.
S (Error)
D9005
+Rem
SD54
MINI link
errors
Error detection
state
1
The relevant station bit goes ON when any of the Installed
MINI (-S3) X(n+0)/X(n+20), X(n+6)/(n+26), X(n+7)/(n+27) or
X(n+8)/X(n+28) goes ON.
2
Goes ON when communications between the installed MINI
(-S3) and the CPU are not possible.
B15
B8
B9
B0
8th
module
8th
module
1st
module
1st
module
.........
Information on
Information on
1
2
S (Error)
D9004 format
change
QnA
SD60
Blown fuse
number
Number of module
with blown fuse
• Value stored here is the lowest station I/O number of the module
with the blown fuse.
S (Error)
D9000
SD61
I/O module
verification
error number
I/O module
verification error
module number
• The lowest I/O number of the module where the I/O module
verification number took place.
S (Error)
D9002
+Rem
SD62
Annunciator
number
Annunciator
number
• The first annunciator number to be detected is stored here.
S
(Instruction
execution)
D9009
SD63
Number of
annunciators
Number of
annunciators
• Stores the number of annunciators searched.
S
(Instruction
execution)
D9124