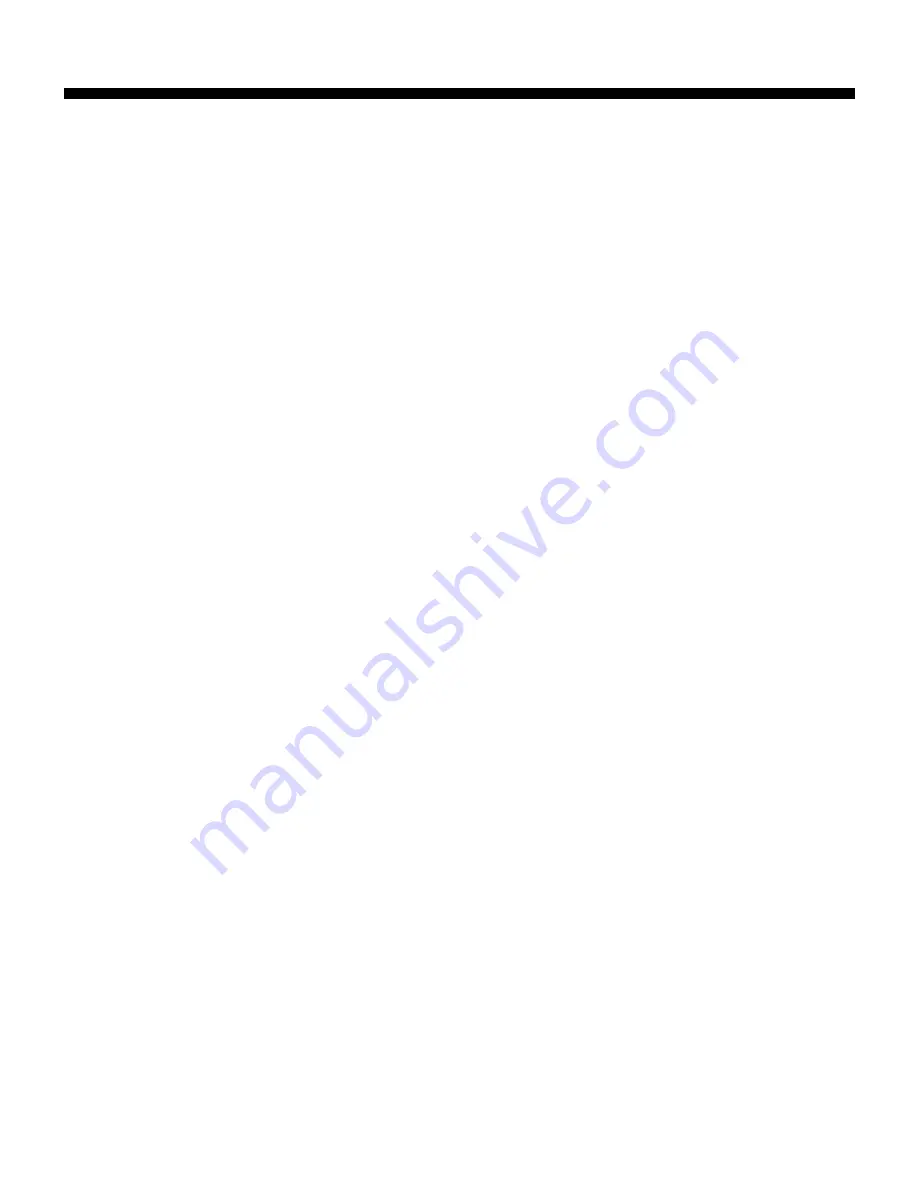
0-1
GROUP 0
GENERAL
CONTENTS
HOW TO USE THIS MANUAL. . . . . .
PRECAUTIONS BEFORE
SERVICE . . . . . . . . . . . . . . . . . . . . . .
PROTECTING THE VEHICLE . . . . . . . . . .
DOING SERVICE WORK IN GROUPS
OF TWO OR MORE MECHANICS . . . . . . .
REMOVAL AND DISASSEMBLY . . . . . . . .
SPECIAL TOOLS . . . . . . . . . . . . . . . . . . . .
PARTS TO BE REPLACED . . . . . . . . . . . .
PARTS . . . . . . . . . . . . . . . . . . . . . . . . . . . .
TUBES AND OTHER RUBBER PARTS . . .
LUBRICANTS . . . . . . . . . . . . . . . . . . . . . . .
BRAKE FLUID . . . . . . . . . . . . . . . . . . . . . . .
SERVICING THE ELECTRICAL
SYSTEM . . . . . . . . . . . . . . . . . . . . . . . . . . .
APPLICATION OF ANTI-CORROSION
AGENTS AND UNDERCOATS . . . . . . . . . .
PRE-INSPECTION CONDITION . . . . . . . . .
VEHICLE WASHING . . . . . . . . . . . . . . . . . .
MULTI USE TESTER (M.U.T.-III)
SUB ASSEMBLY . . . . . . . . . . . . . . . . . . . . .
IN ORDER TO PREVENT VEHICLES
FROM FIRE . . . . . . . . . . . . . . . . . . . . . . . . .
ENGINE OILS . . . . . . . . . . . . . . . . . . . . . . .
Summary of Contents for Pajero Sport 2013
Page 6: ...NOTES...
Page 16: ...BODY PRE DELIVERY INSPECTION 1 10...