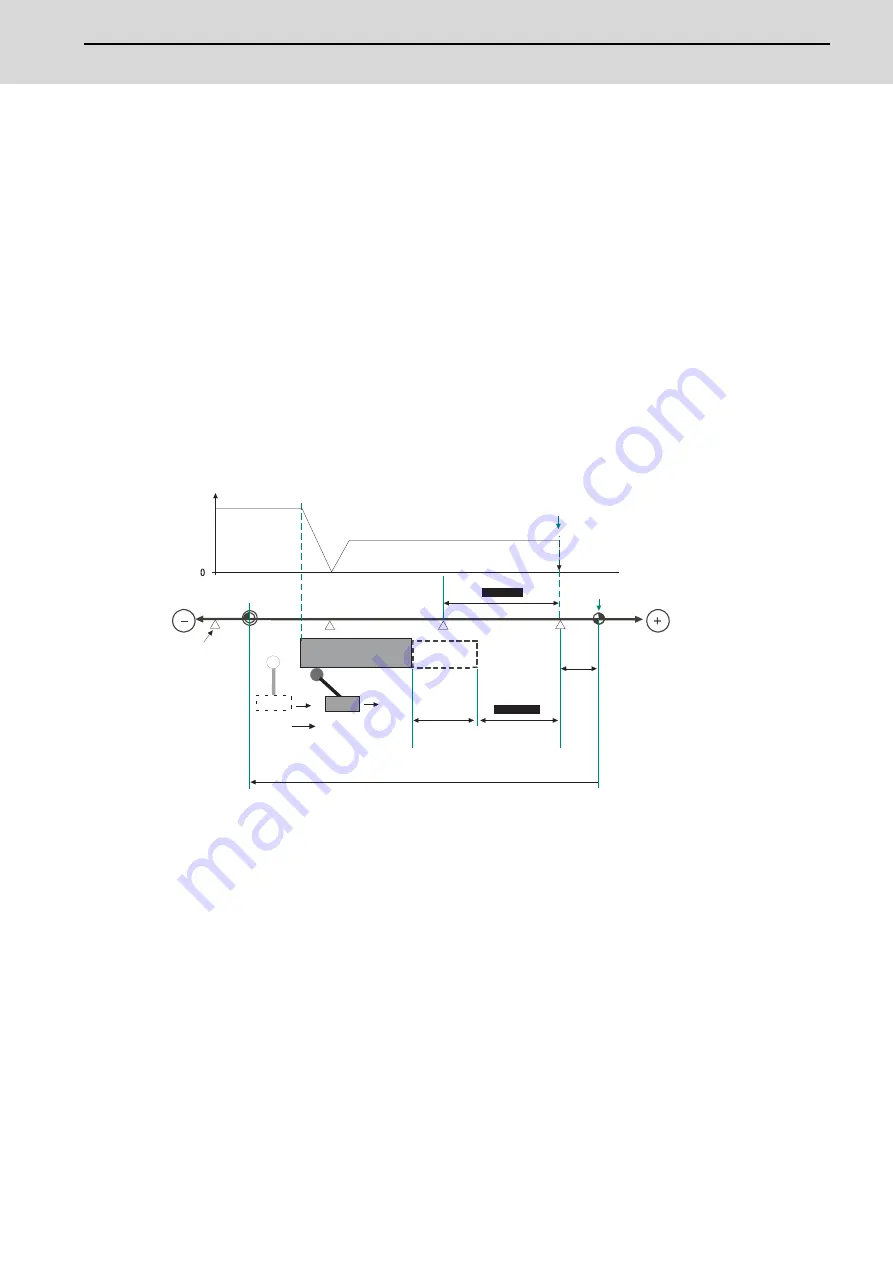
M800S/M80 Series Connection and Setup Manual
22 Setting the Position Detection System
399
IB-1501269-F
(7) Turn the power OFF and ON, and then execute reference position return.
(8) Confirm the grid space and grid amount values on DRIVE MONITOR screen.
If the grid amount value is approximately half of the grid space, the grid mask amount has been set correctly. If the
value is not approximately half, repeat the procedure from step (1).
(9) Set the reference position shift amount (#2027 G28sft).
To designate the electrical zero point as reference position, set "#2027 G28sft" to "0".
(10) Turn the power OFF and ON, and then execute the reference position return.
(Note)
The axis moves at the speed of "#2025 G28rap G28 rapid traverse rate".
The parameter "#2025 G28rap G28 rapid traverse rate" is usually set the maximum speed, which makes
the high-speed movement in the 2nd reference position return and later. Take extra care for the safe axis
movement.
(11) Set the machine coordinate system offset amount (#2037 G53ofs).
[Terms and parameters related to the dog-type reference position return]
Electrical zero point
The first grid point after the dog OFF.
If the grid point is at the position where the near-point dog is kicked OFF, the position of electrical zero point may be at
the grid point where the dog is kicked OFF or at the next grid point because of the delay of the limit switch operation. This
causes a deviation of reference position by the amount of the grid space.
Setting the grid mask amount ("#2028 grmask") prevents this deviation.
Reference position
The base for position and coordinate.
The axis is positioned to this position by the manual reference position return command or G28 command in the
machining program.
The position is determined by shifting from the electrical zero point by the amount of "#2027 G28sft Reference position
shift amount".
#2037 G53ofs
Grid space
Basic machine coordinate
system zero point
Axis speed
Reference position
(for the reference position return)
Position
Electrical zero point
#2026 G28crp
(G28 approach speed)
#2025 G28rap
(G28 rapid traverse rate)
Grid point
OFF
ON
Switch
#2028 grmask
Grid mask
amount
Grid amount
#2027 G28sft
Reference position
shift distance
#2030 dir (-)
(Reference position
return direction)
Near-point dog
Grid mask
Summary of Contents for M80 series
Page 1: ......
Page 4: ......
Page 9: ......
Page 21: ......
Page 23: ......
Page 25: ......
Page 27: ......
Page 29: ......
Page 37: ......
Page 38: ...1 IB 1501269 F 1 System Basic Configuration...
Page 40: ...3 IB 1501269 F 2 General Connection Diagram...
Page 44: ...7 IB 1501269 F 3 List of Configuration...
Page 53: ...M800S M80 Series Connection and Setup Manual 3 List of Configuration 16 IB 1501269 F...
Page 54: ...17 IB 1501269 F 4 General Specifications...
Page 185: ...M800S M80 Series Connection and Setup Manual 4 General Specifications 148 IB 1501269 F...
Page 186: ...149 IB 1501269 F 5 Installation...
Page 211: ...M800S M80 Series Connection and Setup Manual 5 Installation 174 IB 1501269 F...
Page 212: ...175 IB 1501269 F 6 Precautions for Connecting...
Page 219: ...M800S M80 Series Connection and Setup Manual 6 Precautions for Connecting 182 IB 1501269 F...
Page 220: ...183 IB 1501269 F 7 Connection of Control Unit...
Page 245: ...M800S M80 Series Connection and Setup Manual 7 Connection of Control Unit 208 IB 1501269 F...
Page 246: ...209 IB 1501269 F 8 Connection of Keyboard Unit...
Page 248: ...211 IB 1501269 F 9 Connection of Operation Panel I O Unit...
Page 262: ...225 IB 1501269 F 10 Connection of Remote I O Unit...
Page 289: ...M800S M80 Series Connection and Setup Manual 10 Connection of Remote I O Unit 252 IB 1501269 F...
Page 290: ...253 IB 1501269 F 11 Connection of Manual Pulse Generator...
Page 294: ...257 IB 1501269 F 12 Connection of Synchronous Feed Encoder...
Page 296: ...259 IB 1501269 F 13 Connection of MITSUBISHI CNC Machine Operation Panel...
Page 308: ...271 IB 1501269 F 14 Connection of Handy Terminal...
Page 310: ...273 IB 1501269 F 15 Cable...
Page 349: ...M800S M80 Series Connection and Setup Manual 15 Cable 312 IB 1501269 F...
Page 350: ...313 IB 1501269 F 16 Setup Outline...
Page 354: ...317 IB 1501269 F 17 Setting the Hardware...
Page 383: ...M800S M80 Series Connection and Setup Manual 17 Setting the Hardware 346 IB 1501269 F...
Page 384: ...347 IB 1501269 F 18 Setting Up with M80 M800S SETUP INSTALLER...
Page 392: ...355 IB 1501269 F 19 Setting the Parameters and Date Time...
Page 398: ...361 IB 1501269 F 20 PLC Program Writing...
Page 410: ...373 IB 1501269 F 21 Confirming the Basic Operation...
Page 416: ...379 IB 1501269 F 22 Setting the Position Detection System...
Page 440: ...403 IB 1501269 F 23 Setting the Tool Entry Prohibited Range...
Page 454: ...417 IB 1501269 F 24 Confirming the Spindle Operation...
Page 458: ...421 IB 1501269 F 25 Setting the Handy Terminal...
Page 464: ...427 IB 1501269 F 26 Setting the Deceleration Check...
Page 474: ...437 IB 1501269 F 27 Adjust S analog Screen...
Page 479: ...M800S M80 Series Connection and Setup Manual 27 Adjust S analog Screen 442 IB 1501269 F...
Page 480: ...443 IB 1501269 F 28 Device Open Parameter Screen...
Page 486: ...449 IB 1501269 F 29 SRAM Open Parameter Screen...
Page 492: ...455 IB 1501269 F 30 Data Backup and Restoration...
Page 498: ...461 IB 1501269 F 31 Appx 1 Setting the System Lock...
Page 502: ...465 IB 1501269 F 32 Appx 2 Protection Setting...
Page 510: ...473 IB 1501269 F 33 Appx 3 Displaying Original Logo On Standard Screen...
Page 512: ...475 IB 1501269 F 34 Appx 4 EMC Installation Guidelines...
Page 524: ...487 IB 1501269 F 35 Appx 5 Restrictions for Lithium Batteries...
Page 532: ...495 IB 1501269 F 36 Appx 6 Precautions for Compliance to UL c UL Standards...
Page 538: ......
Page 542: ......