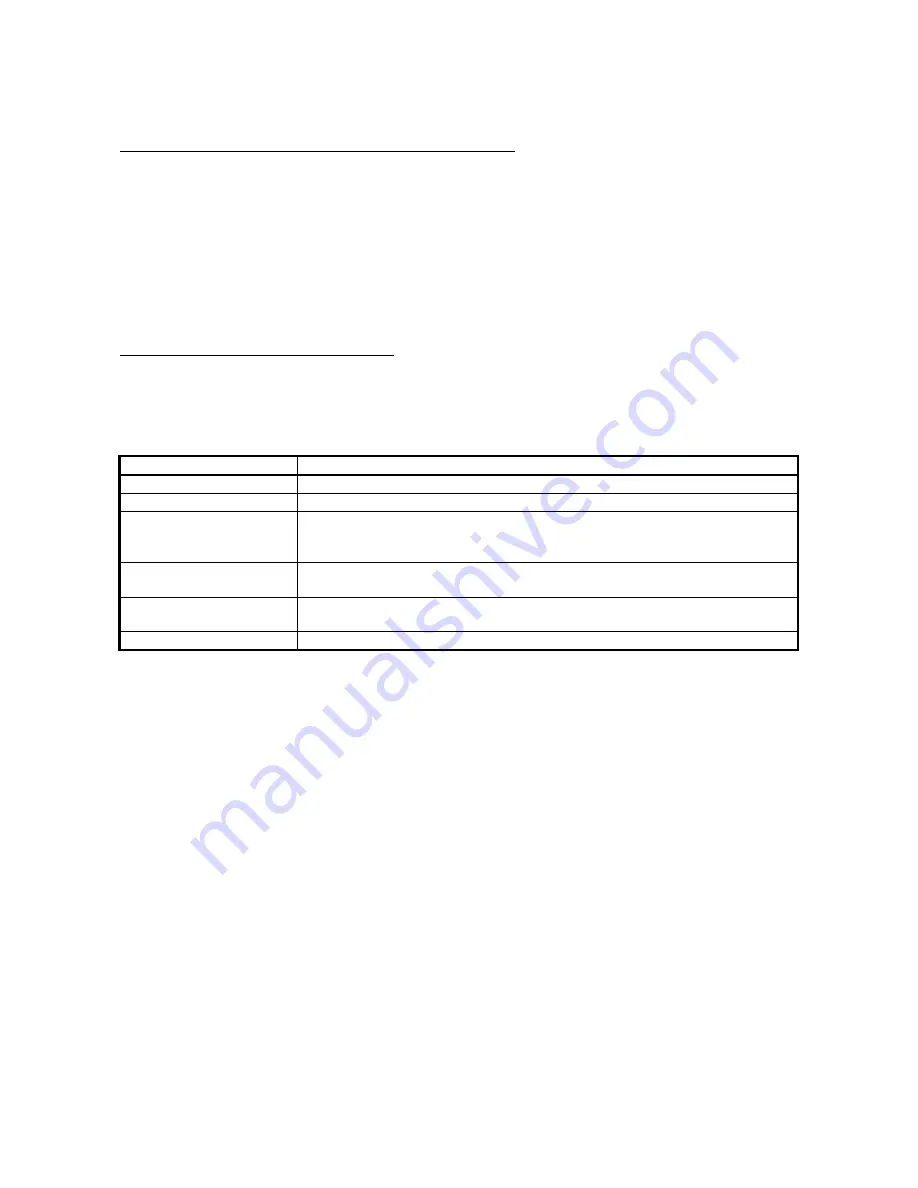
A - 8 A - 8
Conformation to the EMC Directive and Low Voltage Instruction
For details on making Mitsubishi PLC conform to the EMC directive and low voltage
instruction when installing it in your product, please see Chapter 3, "EMC Directive
and Low Voltage Instruction" of the User's Manual (Hardware) of the CPU module to
use.
The CE logo is printed on the rating plate on the main body of the PLC that conforms
to the EMC directive and low voltage instruction.
By making this product conform to the EMC directive and low voltage instruction, it is
not necessary to make those steps individually.
About the Generic Terms and Abbreviations
Unless otherwise specified, this manual uses the following generic terms and
abbreviations.
Abbreviation/general terms
Description of the abbreviation/general terms
D/A conversion module
Generic term for Q62DA, Q64DA, Q68DAV Q68DAI
DOS/V personal computer
IBM PC/AT
®
or compatible computer with DOS/V.
GX Developer
Generic product name of the product types SWnD5C-GPPW-E, SWnD5C-GPPW-EA,
SWnD5C-GPPW-EV and SWnD5C-GPPW-EVA.
"n" in the model name is 4 or greater.
GX Configurator-DA
Generic term for digital-analog conversion module setting and monitor tool GX
Configurator-DA (SW0D5C-QDAU-E)
QCPU (Q mode)
Generic term for Q00JCPU, Q00CPU, Q01CPU, Q02CPU, Q02HCPU, Q06HCPU,
Q12HCPU and Q25HCPU
Personal computer
Generic term for DOS/V personal computer