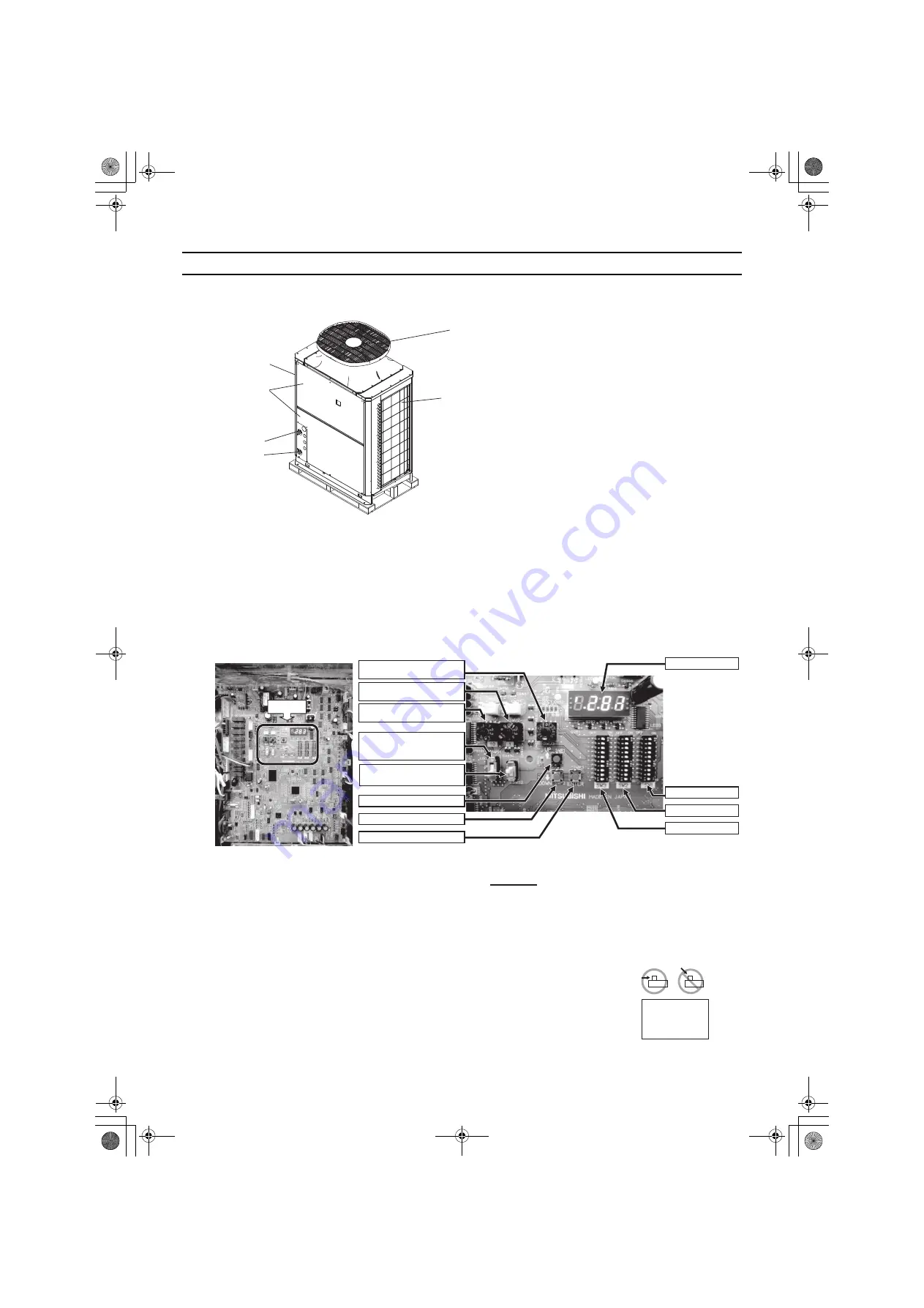
[
II
Restrictions ]
- 24 -
HWE1517A
GB
[5] Switch Types and the Factory Settings
(1) Switch names and functions
There are four main ways to set the settings as follows:
1
Dip switches (SW1 - SW3)
2
Dip switches used in combination with the push switches
3
Rotary switches
4
Slide switches
See below for how these switches are used to set certain items.
Different types of switches on the PCB
Set the slide switch SWS2 on the board inside the control box to the
lower side
during the trial run.
By default, it is set to the upper side for forced stop of the pump and compressor to prevent the pump
being damaged by the anti-freezing process in no water passing status or valve closed status before
the test run.
Upper side: A (under preparation)
Lower side: B (auto)
Always set to the lower side.
* Setting to the upper side forcefully stops the pump and compressor thus the unit does not
operate.
* When SWS2 is set to the upper side, the display shows “P.OFF” and the setting cannot be
made. When “P.OFF” appears, set SWS2 to the lower side.
Discharge air outlet
Service panel
Control box
Intake air inlet
Rotary switch (SWU3) (0-F)
Rotary switch (SWU2) (0-9)
Rotary switch (SWU1) (0-9)
Slide switch (SWS1)
(LOCAL, OFF, and REMOTE
from the top)
Push switch (SWP1) "UP"
Push switch (SWP2) "DOWN"
Push switch (SWP3) "ENTER"
Slide switch (SWS2) *
(A and B from the top)
Switches
]
s
e
h
c
t
i
w
s
e
h
t
f
o
w
e
i
v
d
e
g
r
a
l
n
E
[
]
B
C
P
a
f
o
w
e
i
v
e
r
i
t
n
E
[
LED display
Dip switch (SW1)
Dip switch (SW2)
Dip switch (SW3)
Slide the dip
switches; do not
push down the
switches.
Water outlet
Water inlet
0000001906.book 24 ページ 2018年7月19日 木曜日 午前7時22分
Summary of Contents for QAHV-N560YA-HPB
Page 1: ......
Page 7: ...CONTENTS HWE1517A GB 0000001906 book 2 ページ 2018年7月19日 木曜日 午前7時22分 ...
Page 9: ... 2 HWE1517A GB 0000001906 book 2 ページ 2018年7月19日 木曜日 午前7時22分 ...
Page 21: ... I Read Before Servicing 14 HWE1517A GB 0000001906 book 14 ページ 2018年7月19日 木曜日 午前7時22分 ...
Page 23: ... 16 HWE1517A GB 0000001906 book 16 ページ 2018年7月19日 木曜日 午前7時22分 ...
Page 53: ... 46 HWE1517A GB 0000001906 book 46 ページ 2018年7月19日 木曜日 午前7時22分 ...
Page 65: ... 58 HWE1517A GB 0000001906 book 58 ページ 2018年7月19日 木曜日 午前7時22分 ...
Page 77: ... 70 IV Remote Controller GB HWE1517A 0000001906 book 70 ページ 2018年7月19日 木曜日 午前7時22分 ...
Page 79: ... 72 HWE1517A GB 0000001906 book 72 ページ 2018年7月19日 木曜日 午前7時22分 ...
Page 85: ... 78 HWE1517A GB 0000001906 book 78 ページ 2018年7月19日 木曜日 午前7時22分 ...
Page 91: ... 84 HWE1517A GB 0000001906 book 84 ページ 2018年7月19日 木曜日 午前7時22分 ...
Page 121: ... 114 HWE1517A GB 0000001906 book 114 ページ 2018年7月19日 木曜日 午前7時22分 ...
Page 127: ... 120 HWE1517A GB 0000001906 book 120 ページ 2018年7月19日 木曜日 午前7時22分 ...
Page 173: ... 166 HWE1517A GB 0000001906 book 166 ページ 2018年7月19日 木曜日 午前7時22分 ...
Page 175: ... X Attachments 168 HWE1517A GB 0000001906 book 168 ページ 2018年7月19日 木曜日 午前7時22分 ...
Page 176: ......