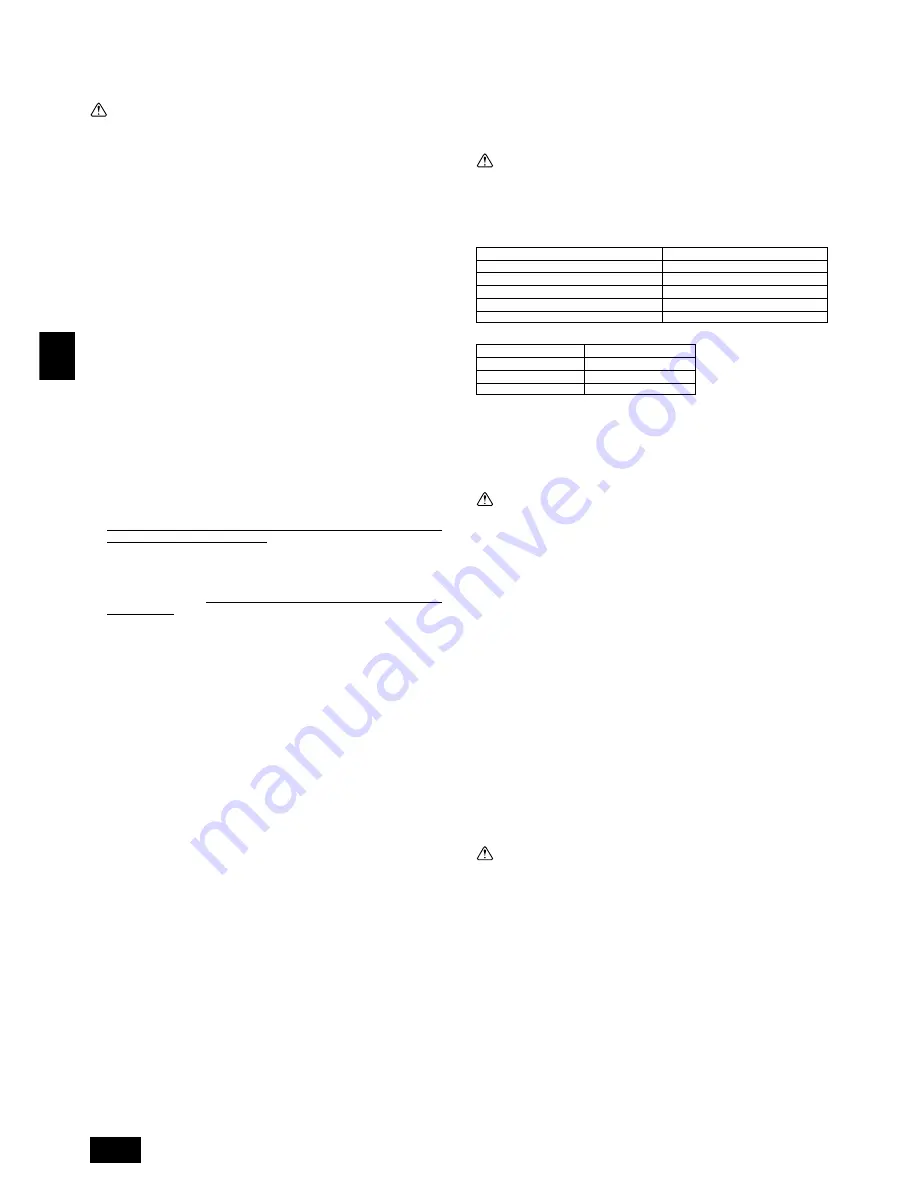
16
GB
D
F
I
NL
E
P
GR
RU
TR
M
ø12.7
N
To constant capacity unit
O
ø28.58
Warning:
Braze the distributor (gas) outside the unit, before mounting distributor (gas)*
to ball valve of the variable capacity unit.
- If brazed while mounted, the ball valve is heated and could result in cracking or
gas leaks. The wiring inside the unit could also be burned.
<For constant capacity unit>
•
Connect piping and operate valves exactly as described in the figure below.
•
Gas side connecting piping is already assembled when the equipment is
shipped.
1
When brazing to connecting pipe with flange, remove the connecting pipe
with flange from the ball valve, and braze at the outside of the unit.
2
During the time when removing the connecting pipe with flange, remove
the seal attached on the rear side of this sheet and paste it onto the flange
surface of the ball valve to prevent the entry of dust into the valve.
3
The refrigerant circuit is closed with a round, close-packed packing at the
shipment to prevent gas leak between flanges. As no operation can be
done under this state, be sure to replace the packing with the hollow pack-
ing attached at the piping connection.
4
At the mounting of the hollow packing, wipe off dust attached on the flange
sheet surface and the packing. Coat refrigerating machine oil (R407C: Es-
ter oil, ether oil or alkylbenzene [small amount]) onto both surfaces of the
packing.
[Fig. 9.2.5] (P.5)
A
Close-packed packing
B
Hollow packing
•
After evacuation and refrigerant charge, ensure that the handle is fully open. If
operating with the valve closed, abnormal pressure will be imparted to the
high- or low-pressure side of the refrigerant circuit, or a shortage of oil in the
compressor may occur due to lack of oil flow between units, giving damage to
the compressor, four-way valve, etc.
•
For evacuating, be sure to provide an oil balance pipe between the variable
capacity and constant capacity units.
•
Determine the amount of additional refrigerant charge by using the formula,
and charge refrigerant additionally through the service port after completing
piping connection work.
•
After completing work, shut the service port and cap tightly so that gas leaking
does not occur.
[Fig. 9.2.6] (P.5)
<A> [Ball valve (liquid side)]
<B> [Ball valve (gas side)]
<C> [Ball valve (oil balance side)]
The unit is set vertically between the compressor and control box.
<D> (This figure shows the valve in the fully open state.)
A
Valve stem
[Fully closed at the factory, when connecting the piping, when evacuating, and
when charging additional refrigerant. Open fully after the operations above are
completed.]
B
Stopper pin [Prevents the valve stem from turning 90
°
or more.]
C
Packing (accessory)
D
Connecting pipe (accessory)
[Use packing and securely install this pipe to the valve flange so that gas leak-
age will not occur. (Tightening torque: 25 N·m (250 kg·cm)) Coat both surfaces
of the packing with refrigerating machine oil (R407C: Ester oil, ether oil or
alkylbenzene [small amount])]
E
Open (Operate slowly)
F
Cap, copper packing
[Remove the cap and operate the valve stem. Always reinstall the cap after
operation is completed. (Valve stem cap tightening torque: 25 N·m (250 kg·cm)
or more)]
G
Service port
[Use this port to evacuate the refrigerant piping and add an additional charge
at site.
Open and close the port using a double-ended wrench.
Always reinstall the cap after operation is completed. (Service port cap tight-
ening torque: 14 N·m (140 kg·cm) or more)]
H
Flare nut
[Tightening torque: 55 N·m (550 kg·cm)
Use a double spanner to open and close. Apply a coat of refrigerating machine
oil (R407C: Ester oil, ether oil or alkylbenzene [small amount]) to the flare
bonding surface.]
I
ø28.58
J
To distributor (gas) inside variable capacity unit
K
ø12.7
L
To distributor (liquid)
M
To variable capacity unit
N
Fastening plate
Warning:
Be sure to remove the connecting pipe from the ball valve, and braze it out-
side the unit.
- If brazed while mounted, the ball valve is heated and could result in cracking or
gas leaks. The wiring inside the unit could also be burned.
Appropriate tightening torque by torque wrench:
Copper pipe external dia. (mm)
Tightening torque (N·m) / (kg·cm)
ø6.35
14 to 18 / 140 to 180
ø9.52
35 to 42 / 350 to 420
ø12.7
50 to 57.5 / 500 to 575
ø15.88
75 to 80 / 750 to 800
ø19.05
100 to 140 / 1000 to 1400
Tightening angle standard:
Pipe diameter (mm)
Tightening angle (
°
)
ø6.35, ø9.52
60 to 90
ø12.7, ø15.88
30 to 60
ø19.05
20 to 35
[Fig. 9.2.7] (P.5)
Note:
If a torque wrench is not available, use the following method as a standard:
When you tighten the flare nut with a wrench, you will reach a point where
the tightening torque will abruptly increase. Turn the flare nut beyond this
point by the angle shown in the table above.
Caution:
•
Always remove the connecting pipe from the ball valve and braze it out-
side the unit.
- Brazing the connecting pipe while it is installed will heat the ball valve and
cause trouble or gas leakage. The piping, etc. inside the unit may also be
burned.
•
Use ester oil, ether oil or alkylbenzene (small amount) as the refrigerat-
ing machine oil to coat flares and flange connections. (For R407C mod-
els)
- The refrigerating machine oil will degrade if it is mixed with a large amount of
mineral oil.
•
Do not use a leak detection additive.
9.3. Oil balance pipe connection method
•
Oil balance piping can be taken out from the front, bottom or side of the unit
(left side for the variable capacity unit, right side for the constant capacity unit).
•
Connect piping and operate valves exactly as described below (for details, see
item 9.2.).
1
After connecting oil balance pipe, be sure to evacuate using the service
port of the variable capacity unit side valve.
2
After evacuating, be sure to fully open each valve stem. If you operate with
the valve closed, a shortage of oil in the compressor may occur due to lack
of oil flow between units, which could result in damage to the compressor.
3
After completing work, shut the cap of the service port and handle section
tightly so that gas leaking does not occur.
Warning:
Failure to connect the oil balance pipe will result in the compressor being
damaged.
•
Provide 10 mm of clearance between the variable capacity and constant ca-
pacity units. Position the variable capacity unit so that its front is facing on the
right side and the constant capacity unit so that its front is facing on the left.
Connect the oil balance pipe for the distributor kit is attached with constant
capacity unit according to the following procedure.
1
Open the knock-out holes of the left side panel for the variable capacity
unit, and the right side panel for the constant capacity unit.
2
After installing the units, flare-connect the piping included with the unit
(ø12.7).
3
Block the clearance between units with the 2 seals included with the con-
stant capacity unit.
4
Put on pipe cover between oil balance pipe 2 and oil balance pipe 3 (ac-
cessory in distributor kit).