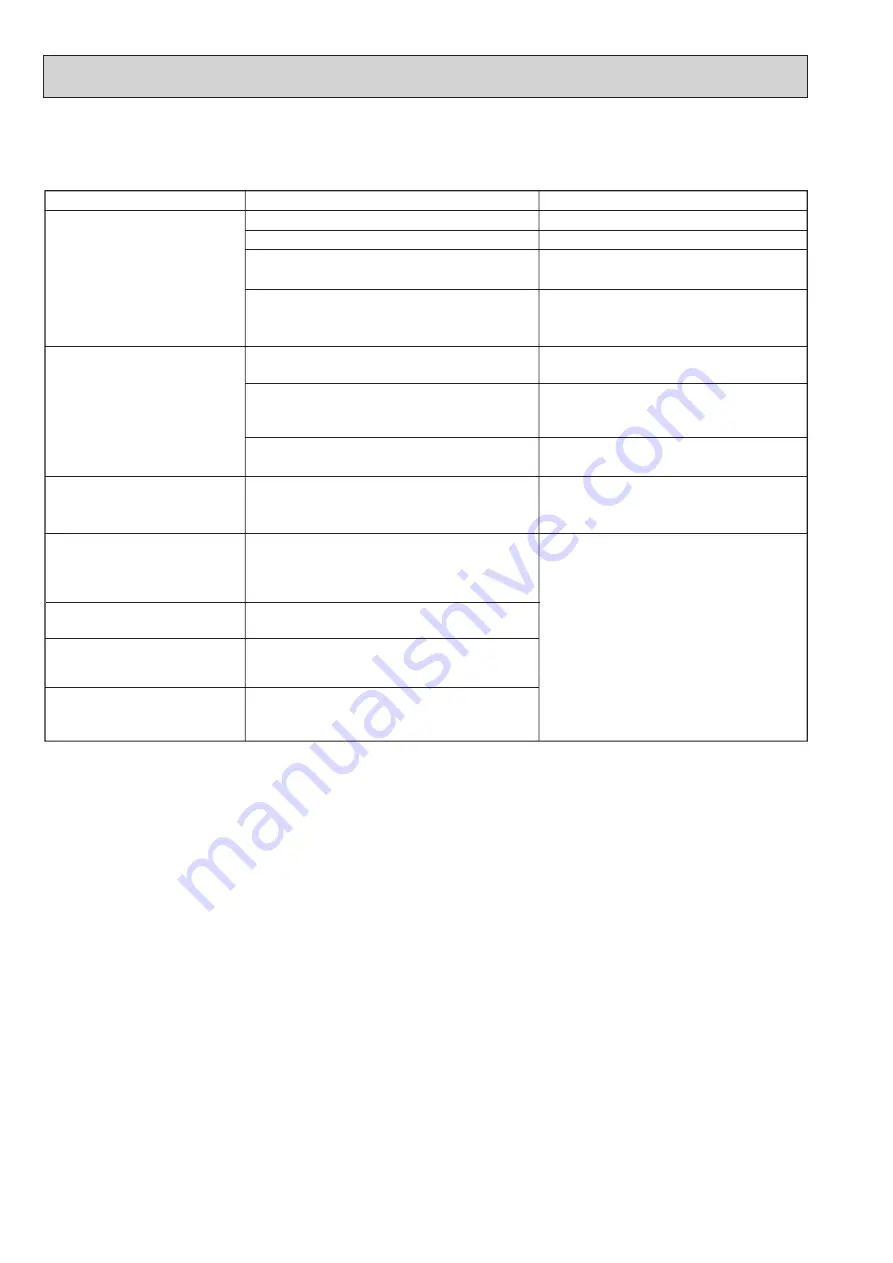
37
36
37
OCH728A
Problem
Possible Reason
Corrective Action
Intake grille does not function
with operation of the remote
controller.
Intake grille cannot be placed
in the correct position.
Intake grille stops lowering in
mid flow. (Intake grille would not
lower any further.)
Noises are made during
up/down operation. (While
intake grille is moving up/down.)
Noises are made while placing
the intake grille in.
Intake grille repeats rising and
lowering several times while being
placed in the correct position.
Intake grille leans toward one side
during the up/down operation.
Air-conditioner is running.
Power failure
Batteries are not inserted into the wireless remote
controller. Or battery power is running low.
There is something on the intake grille.
Or something is stuck in the intake grille.
There is something on the intake grille.
Filter is not properly installed.
Intake grille is not hung with all 4 hooks.
Because the intake grille has finished lowering to
the auto-stop position.
This is the noise made when the string is winded
and unwound.
This is the operational noise for placing the intake
grille in securely.
The speeds of winding each string is slightly
different.
Stop running the air-conditioner and try again.
After recovering from power failure, try again.
Install or replace the battery.
This is normal.
This is normal.
Note: If you want to change the setting for the
lowering distance, contact your dealer.
Lower the intake grille again and hang the
hook on the intake grille.
Lower the intake grille again and check
whether the filter is installed in the correct
position.
Remove the objects or obstacles from the
intake grille.
This is the operation for placing the intake grille in
securely.
Remove the objects or obstacles from the
intake grille. Or, remove the stuck object.
9-3. TROUBLESHOOTING