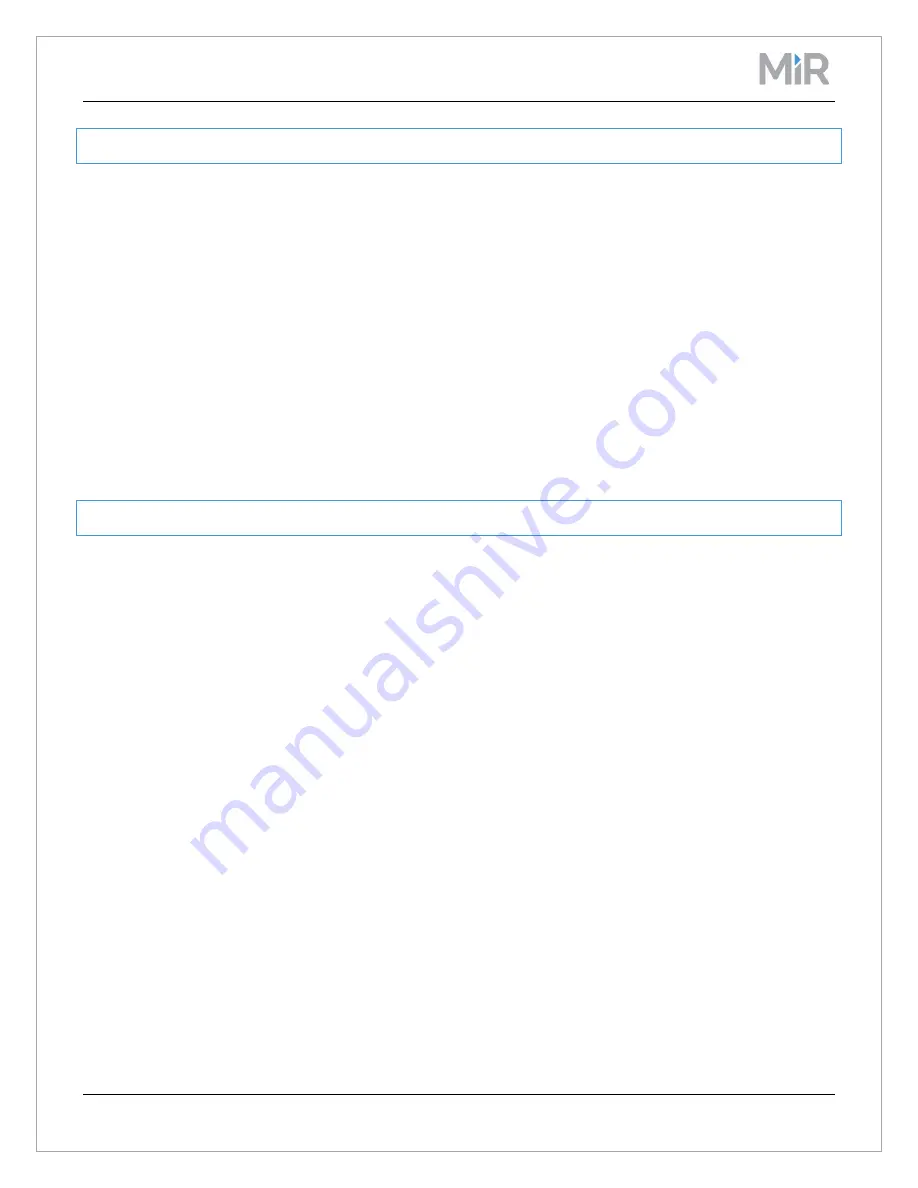
MiR100, MiR200 & MiRHook Risk Analysis
Copyright Mobile Industrial Robots 2019
Page
3
of
35
2
Introduction
This document describes scenarios with MiR100, MiR200 and MiRHook that require special attention. First, an
introduction to the terminology, assumptions, safety- and awareness indicators. This is followed by a section
describing normal use case scenarios.
Each scenario is divided into phases. The phases are described in chronological order.
For each residual risk, the compensating safety features are highlighted, and based on this a conclusion is made
on the significance of the residual risk.
Please note that all scenarios are illustrated with MiR200 and MiRHook, but they apply equally for MiR100 and
MiRHook.
This document does not provide an exhaustive list of scenarios in which MiR100, MiR200, MiRHook can be
used with a reduced safety level of the safety system. However, it describes the most common scenarios for
the intended use. The scenarios provided in this document can also be used as a template for making risk
analysis of similar scenarios during the commissioning phase.
3
Terminology
•
Awareness indicator
: Light and/or acoustic signals, see section 4.
•
Charging station
: Unit connected to a factory power outlet which enables a robot to autonomously
charge its batteries.
•
Docking
: Precision maneuvering to a relative marker.
•
Entry position
: Coordinate on the robot’s map that must be reached before initiating a docking
sequence.
•
Goal position
: Coordinate on the robot’s map that must be reached to finish a docking sequence.
•
Relative marker
: Object with specific physical dimensions and shape used for precision positioning of
the robot. Examples are pallet rack, charging station, V-, VL- and L-marker.
•
Operating hazard zone
: Marked area according to standard EN 1525:1997 clause A.3.2. No obstacles
other than those specified by each scenario can be placed inside this zone.
•
MiRHook
(MiRHook100 and MiRHook200): Top module that enables MiR100 and MiR200 to tow a cart.
•
Cart
: A cart commissioned to be moved by MiRHook.
•
PLd
: Performance level d as defined by ISO 13849-1.
•
Not a safety function
: A function that is not safety rated.
•
Protective field
: Area in which protective stop is automatically triggered if a person or object enters
the area.
•
Tolerance zone
: The safety laser scanner measures the distance to a diffuse reflection and causes a
tolerance to the measurement. In most situations, including during tests, the safety laser scanner will
detect a person within the tolerance zone.
•
Relative move
: When driving using a relative move the robot relies only on wheel encoders for
navigation, and the robot will only move in the specified direction, for example straight forward.