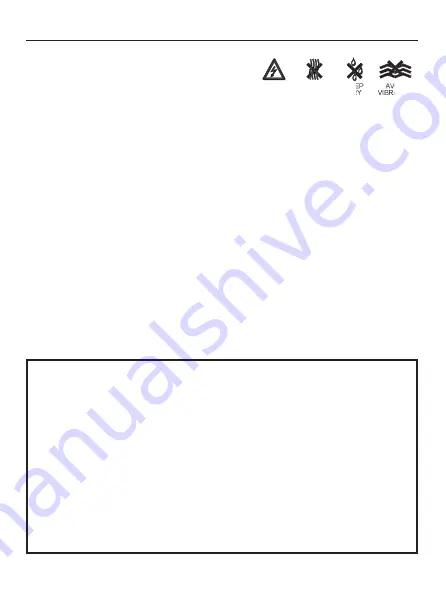
i
Safety Warnings
•
This symbol
denotes an important safety tip or warning.
Failure to observe these warnings may result in serious injury.
Please read these instructions carefully
before performing
any of the procedures contained in this manual.
•
DO NOT INSTALL, REMOVE, OR REWIRE THIS EQUIPMENT
WITH POWER APPLIED.
Have a qualified electrical technician
install, adjust and service this equipment. Follow the National
Electrical Code and all other applicable electrical and safety
codes, including the provisions of the Occupational Safety and
Health Act (OSHA), when installing equipment.
•
Reduce the chance of an electrical fire, shock, or explosion by
proper grounding, over-current protection, thermal protection,
and enclosure. Follow sound maintenance procedures.
It is possible for a drive to run at full speed as a result of
a component failure.
Minarik strongly recommends the
installation of a master switch in the main power input to stop
the drive in an emergency.
Circuit potentials are at 115 VAC or 230 VAC above earth
ground.
Avoid direct contact with the printed circuit board or
with circuit elements to prevent the risk of serious injury or
fatality. Use a non-metallic screwdriver for adjusting the
calibration trimpots. Use approved personal protective
equipment and insulated tools if working on this drive with
power applied.
SHOCK
HAZARD
AVOID
HEAT
KEE
DR
OID
ATION
Summary of Contents for XL1100A
Page 69: ...63 NOTES...
Page 70: ...64 NOTES...