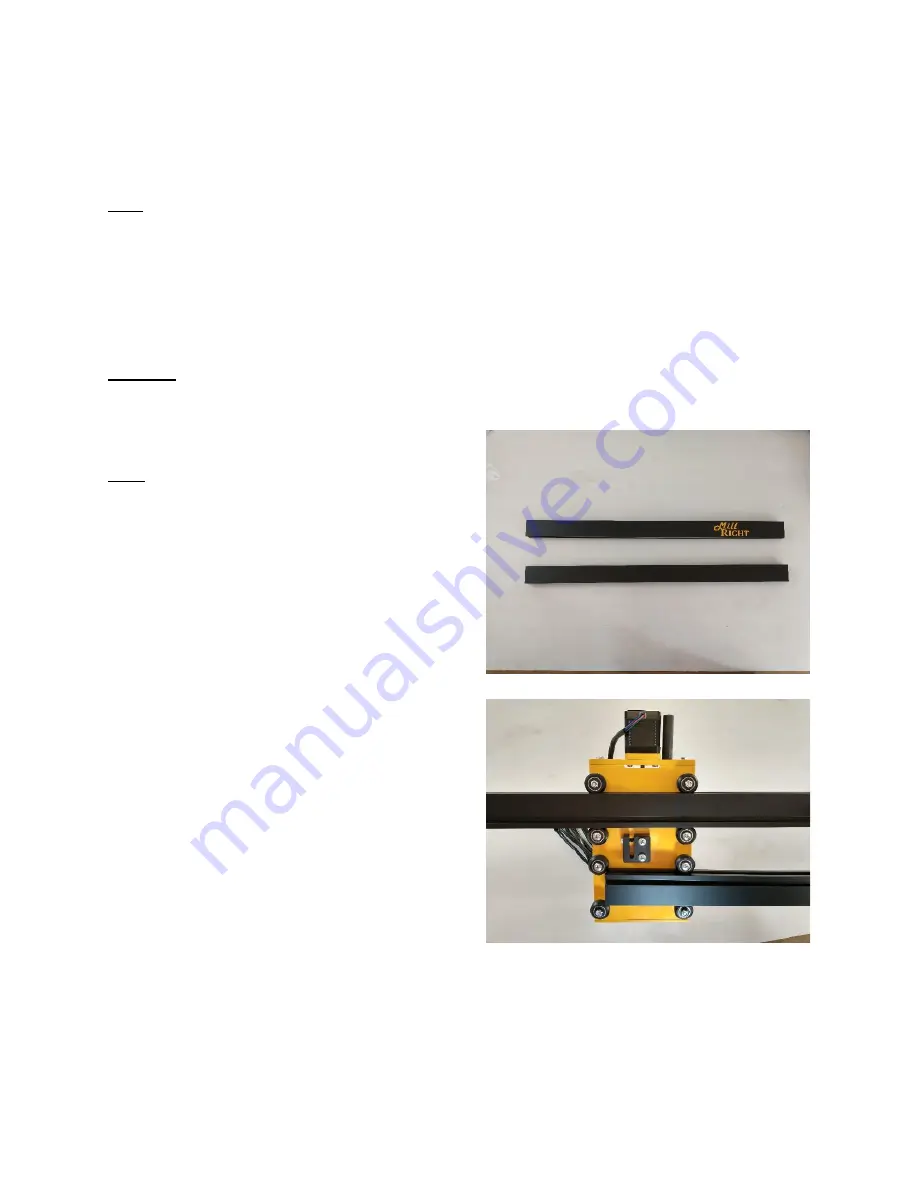
Page 17 or 34
Attaching XZ Assembly to Gantry Plates
Parts
613mm Extrusion w/ MillRight Sticker
613mm Extrusion
(1) 600mm Lead Screw
Hardware
(8) #10x1 Self-tapping Screws
Tools
Phillips Screwdriver
1.5mm Hex Key
2.5mm Hex Key
8mm or 5/16
”
Wrench or Socket
WD40 or Other Lubricant
Run the 613mm extrusions through the v-wheels on
the X Plate Extrusion. The extrusion with the
MillRight sticker will go up top. Make sure the
extrusions are oriented as pictured. If the wheels are
too tight, use the 10mm wrench to turn the eccentric
spacers until the extrusions fit. Once the extrusion is
in, turn the eccentric spacers until the wheels are
making good contact with the extrusion.
Tighten the v-wheels making sure not to turn the
eccentric spacers. Turn the XZ Assembly over and
move it to the end of the extrusions with the sticker.