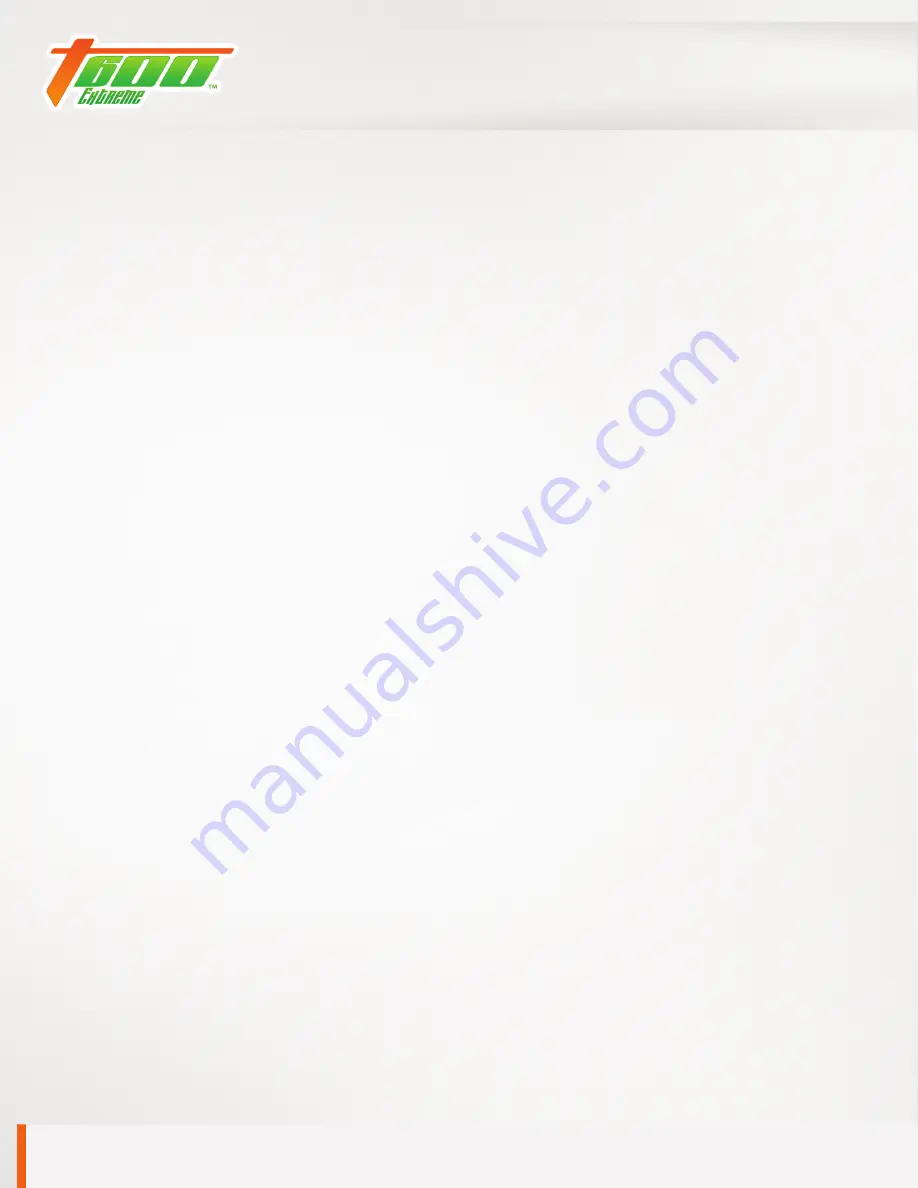
Instruction Manual
Page 2
TABLE OF CONTENTS
Chapter 1:
Intended Use
Chapter 2:
Explanation of Warnings
Chapter 3:
Electrical and Air Requirements
Chapter 4:
Principles of Heat Sealing
Chapter 5:
Definition of Controls
Chapter 6:
Recommended Replacement Parts
Chapter 7:
Machine Specifications
Chapter 8:
Maintenance
Chapter 9:
Transportation Specs and Storage
Chapter 10:
Technical Requirements
Page 3
Pages 4-5
Page 6
Page 7
Page 8-10
Page 11
Pages 12-14
Pages 15-24
Page 25
Page 26
Table of Contents