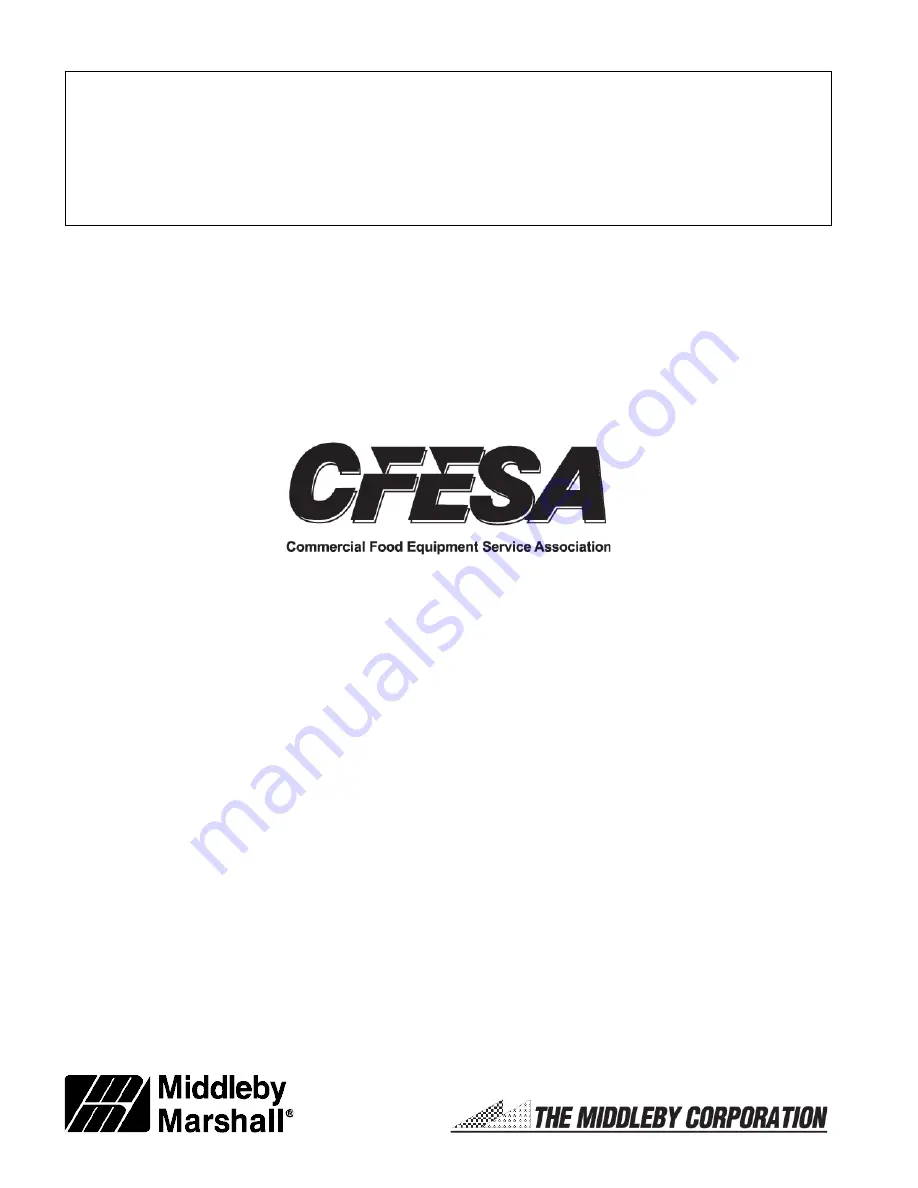
WARNING
Improper installation, adjustment, alteration, service or
maintenance can cause property damage, injury or death. Read
the installation, operating and maintenance instructions
thoroughly before installing or servicing this equipment.
NOTICE
During the warranty period, ALL parts replacement and servicing should be performed by your Middleby Marshall
Authorized Service Agent. Service that is performed by parties other than your Middleby Marshall Authorized
Service Agent may void your warranty.
NOTICE
Using any parts other than genuine Middleby Marshall factory manufactured parts relieves the manufacturer of all
warranty and liability.
NOTICE
Middleby Marshall reserves the right to change specifications at any time.
Middleby is proud to support the Commercial Food Equipment
Service Association (CFESA). We recognize and applaud
CFESA’s ongoing efforts to improve the quality of technical
service in the industry.
Middleby Cooking Systems Group • 1400 Toastmaster Drive • Elgin, IL 60120 • USA • (847)741-3300 • FAX (847)741-4406
www.middleby.com
Summary of Contents for PS629G Series
Page 10: ...SECTION 1 DESCRIPTION 10 Blank Plates two sizes and an Air Finger...
Page 17: ...SECTION 2 INSTALLATION 17 Model PS629G Dimensions with Optional Legs Casters...
Page 24: ...SECTION 2 INSTALLATION 24 NOTES...
Page 32: ...SECTION 3 OPERATION 32 NOTES...
Page 39: ...SECTION 4 MAINTENANCE 39...
Page 46: ...SECTION 4 MAINTENANCE 46 NOTES...
Page 49: ...SECTION 5 TROUBLESHOOTING 49 NOTES...
Page 50: ......