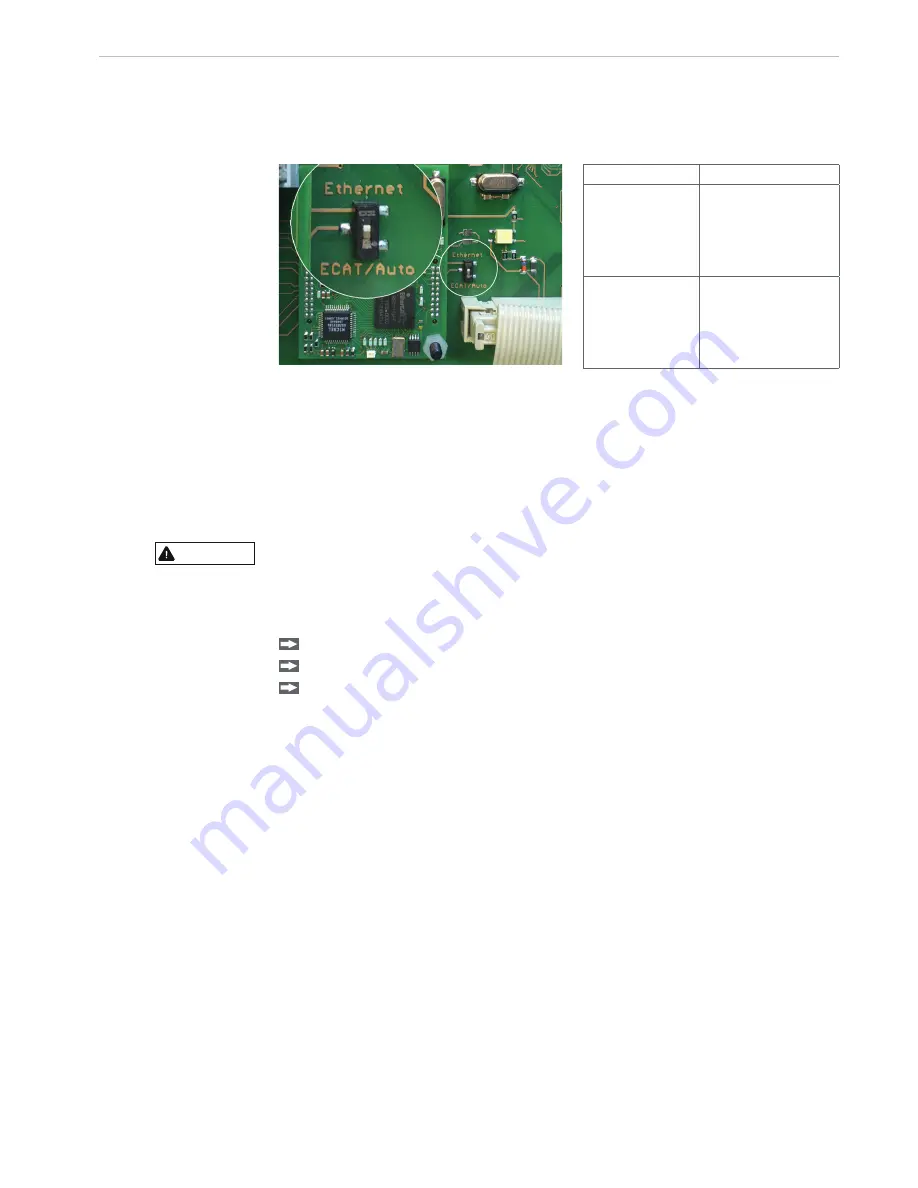
Operation and Maintenance
capaNCDT 6500
Page 47
7.2
Change Interface
You can not change directly to the EtherCAT interface through the web interface or com-
mand. Restart your controller to do this. Keep in mind also that the setting of the Ether-
CAT switch is in the correct position, see
Fig. 37
.
Switch position
Meaning
Ethernet
Regardless to the
software setting
always the Ethernet
interface is active.
ECAT/Auto
Active interface,
which is set via the
web interface or
command.
Fig. 37 Switch to change the interface
A change from the EtherCAT interface back to the Ethernet interface is possible with the
hardware switch on the DD6530 display board or via the corresponding CoE Object. In
both cases, then a restart of the controller is required.
To integrate the EtherCAT interface e.g. within TwinCAT an ESI-file is supplied.
You will find further instructions in the appendix, see Chap.
A 5
.
8.
Operation and Maintenance
Disconnect the power supply before touching the sensor surface.
> static discharge
> danger of injury
Please take care of the following:
Make sure that the sensor surface is always clean.
Switch off the power supply before cleaning.
Clean with a damp cloth; then rub the sensor surface dry.
Changing the target or very long operating times can lead to slight reductions in the
operating quality (long term errors). These can be eliminated by recalibration, see Chap.
5.3
, see Chap.
5.4
.
In the event of a defect in the controller, the preamplifier, the sensor or the sensor/pream-
plifier cable, the parts concerned must be sent back for repair or replacement.
In the case of faults the cause of which is not clearly identifiable, the whole measuring
system must be sent back for repair or replacement to
MICRO-EPSILON MESSTECHNIK
GmbH & Co. KG
Königbacher Straße 15
94496 Ortenburg / Germany
CAUTION
Summary of Contents for capaNCDT 6500
Page 67: ......