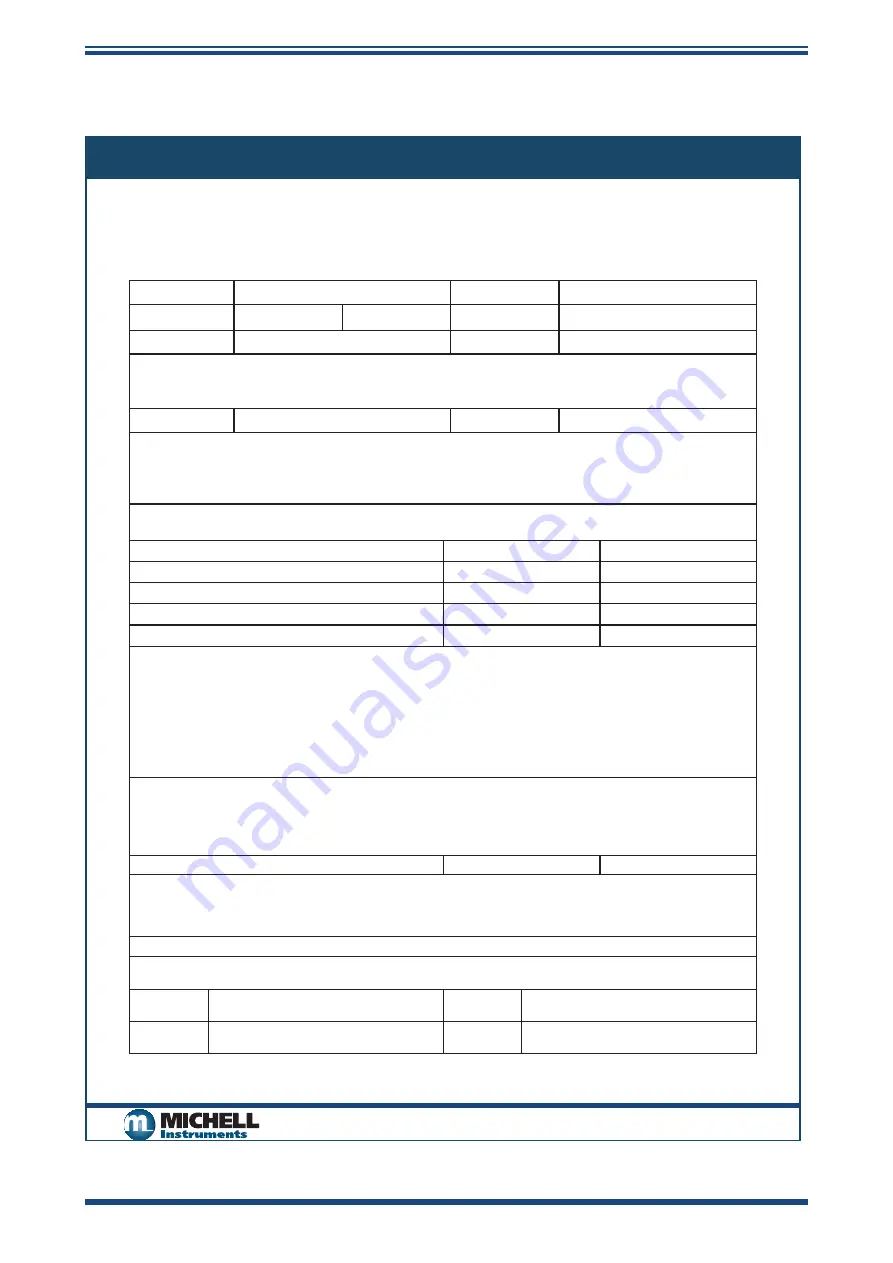
XZR250 User’s Manual
Michell Instruments
45
APPENDIX D
Appendix D
Analyzer Return Document & Decontamination Declaration
F0121, Issue 2, December 2011
Decontamination Certificate
IMPORTANT NOTE: Please complete this form prior to this instrument, or any components, leaving your
site and being returned to us, or, where applicable, prior to any work being carried out by a Michell
engineer at your site.
Instrument
Serial Number
Warranty Repair?
YES
NO
Original PO #
Company Name
Contact Name
Address
Telephone #
E-mail address
Reason for Return /Description of Fault:
Has this equipment been exposed (internally or externally) to any of the following?
Please circle (YES/NO) as applicable and provide details below
Biohazards
YES
NO
Biological agents
YES
NO
Hazardous chemicals
YES
NO
Radioactive substances
YES
NO
Other hazards
YES
NO
Please provide details of any hazardous materials used with this equipment as indicated above (use continuation sheet
if necessary)
Your method of cleaning/decontamination
Has the equipment been cleaned and decontaminated?
YES
NOT NECESSARY
Michell Instruments will not accept instruments that have been exposed to toxins, radio-activity or bio-hazardous
materials. For most applications involving solvents, acidic, basic, flammable or toxic gases a simple purge with dry
gas (dew point <-30°C) over 24 hours should be sufficient to decontaminate the unit prior to return.
Work will not be carried out on any unit that does not have a completed decontamination declaration.
Decontamination Declaration
I declare that the information above is true and complete to the best of my knowledge, and it is safe for Michell
personnel to service or repair the returned instrument.
Name (Print)
Position
Signature
Date