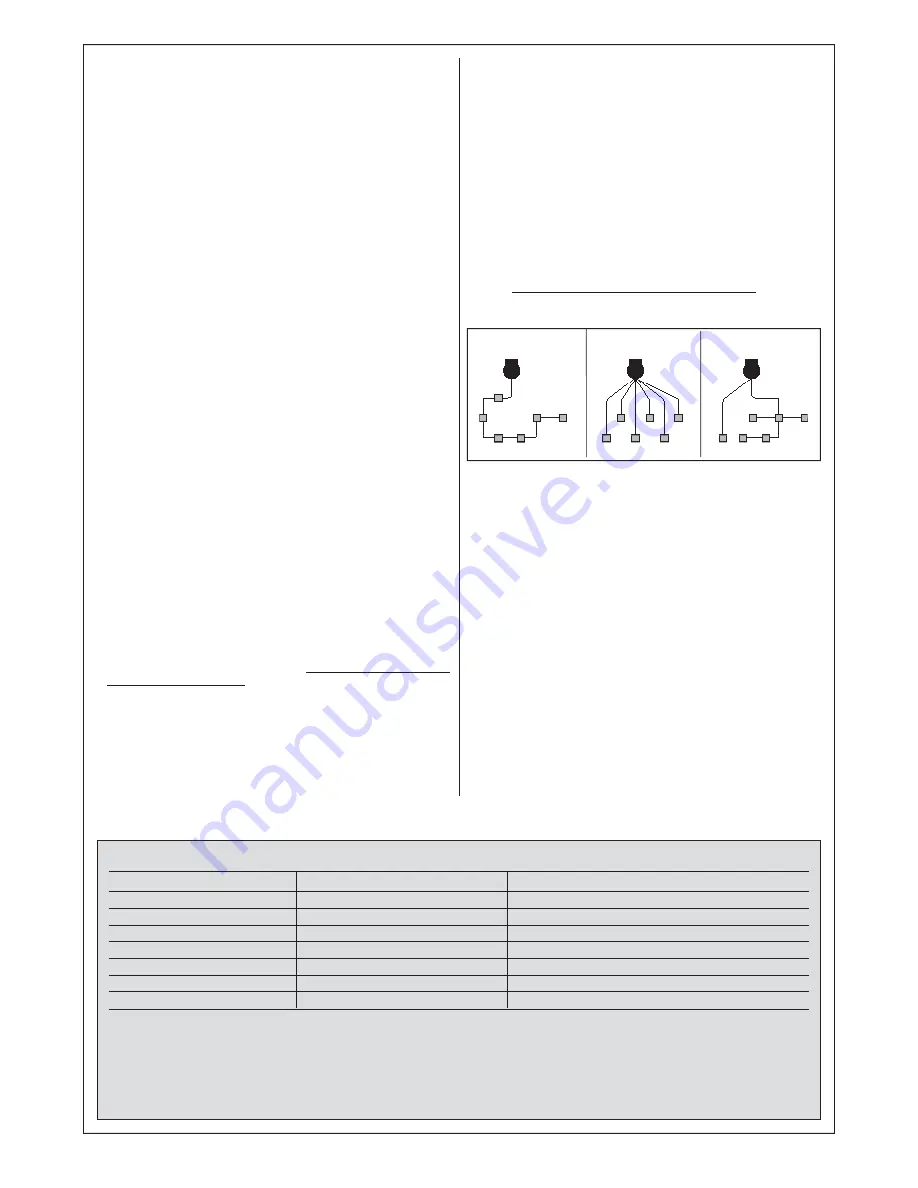
4
TABLE 2 - Technical specifications of electrical cables
Connection
Type of cable
(minimum section values)
Max. admissible length
A
- Power line
Cable 3 x 1.5 mm
2
30
m
(note 1)
B
- FLASH flashing light output
Cable 2 x 0.5 mm
2
20
m
C
- Radio aerial
RG58 type shielded cable
20 m (less than 5 m recommended)
D
- input/output ECSbus
Cable 2 x 0.5 mm
2
20
m
(note 2)
E
- STOP input
Cable 2 x 0.5 mm
2
20
m
(note 2)
F
- OPEN input
Cable 2 x 0.5 mm
2
20
m
(note 2)
G
- Motor output M1
Cable 3x1 mm
2
10
m
Note 1
- If the power cable is longer than 30 m, a cable with a larger section is required (e.g. 3x2.5 mm
2
) and safety earthing is necessary in the
vicinity of the automation.
Note 2
- For cables of ECSbus and those of the STOP and OPEN inputs, a single cable with multiple internal wires may be used, to combine
several connections: for example, the STOP and OPEN inputs can be connected to the KS100 selector switch with a cable of 4 x 0.5 mm
2
.
CAUTION! – The cables used must be suited to the installation environment: for example a cable type H03VV-F is recommended for
indoor environments, and a cable type H07RN-F for outdoor environments.
––– STEP 4 –––
4.1 - PRELIMINARY CHECKS FOR INSTALLATION
4.1.1 - Establish the position of devices in the system
With reference to
fig. 1
and
5
, locate the approximate position for instal-
lation of each device envisaged in the system.
Fig. 1
shows a system
made using this product and other optional accessories in the Mhouse
range. These elements are positioned according to a typical standard
layout. The components are:
[
a
] - 1 FL100 flashing light with integrated aerial
[
b
] - 1 pair of PH100 photocells (one TX and one RX)
[
c
] - 1 KS100 key-operated selector switch
[
d
] - 2 photocell posts
[
e
] - WS1SC Gearmotor equipped with integrated CLS2 control unit
[
f
] - WS1SK Gearmotor
[
g
] - Closing stop (not included)
WARNING! - Some of these devices are optional and may not be
present in the kit (see Mhouse product catalogue).
WARNINGS:
• The gearmotor must be anchored to the ground, laterally to the gate
using the related fixing plate.
• The fixed control devices must be positioned:
- in sight of the automation;
- far from moving parts;
- at a height of at least 1.5 m from the ground;
- not accessible by the public.
4.1.2 - Establish the position of all connection cables
Refer to the instructions in paragraph 4.2 to establish the layout of the
raceways for electric cable ducting.
4.1.3 - Ensure all equipment and materials for work are available
Before starting work, ensure that you have all equipment and materials
required to complete the work. Ensure that all items are in good condition
and comply with local safety standards.
4.1.4 - Completing the set-up work
Prepare the area for subsequent installation of the devices, completing all
preliminary work, such as:
- digging of raceways for protection ducting of electric cables (external
ducting may be used as an alternative);
- laying of protection ducting and embedding in concrete;
- sizing of all electric cables to required length (see paragraph 4.2) and
routing in protection ducting.
Caution! - In this phase, do not make
any electrical connections.
Warnings
:
• The hoses and ducting serve to protect electrical cables and prevent
accidental damage in the event of impact.
• When laying pipelines, take into account the risk of possible deposits of
water in the branch wells, where condensate may form in the pipelines
and the control unit with possible damage to the electronic circuits.
• Position the ends of the ducting at the points envisaged for fixture of
the various components
4.2 - PREPARING ELECTRIC CABLES
To prepare all connection cables, proceed as follows.
a)
- Refer to
fig. 5
to check the connections of the various devices to the
control unit and terminals to be used for each connection.
Impor-
tant
- Only devices using “ECSbus” technology can be connected to
the terminal “ECSbus”.
b)
- Refer to
fig. 1
to check positions of the electrical cables in the area.
Then draw a similar diagram on paper, adapting it to specific require-
ments of your system.
Note
- This diagram will be useful to establish
the route of the raceways for cable ducting, and to draw up a com-
plete list of the cables required.
c)
- Read
Table 2
to determine the type of cables to be used; then refer
to the diagram drawn above and on-site measurements to deter-
mine the length of each cable.
Caution! - No cable must exceed
the specific maximum length stated in Table 2.
WARNING
-
“ECSbus” technology enables the interconnection of devic-
es using a single “bus” cable, with 2 internal electrical wires. Connection
of several devices can be in the configuration “
cascade
”, “
star
” or the
latter two “
combined
”.
cascade
star
combined
Summary of Contents for MhouseKit WS2S
Page 2: ......
Page 7: ...5 D G B C D D E F a d g d e f b b c 1 3 4 5 A B E H F I 2 L G D C A...
Page 9: ...7 8 10 NO 11 E D C 12 13 9 A B F G...
Page 10: ...8 M L 15 17 N O P 16 Blue Yellow Green Brown 18 19 I 14 H H...
Page 30: ...28...
Page 34: ......
Page 35: ......