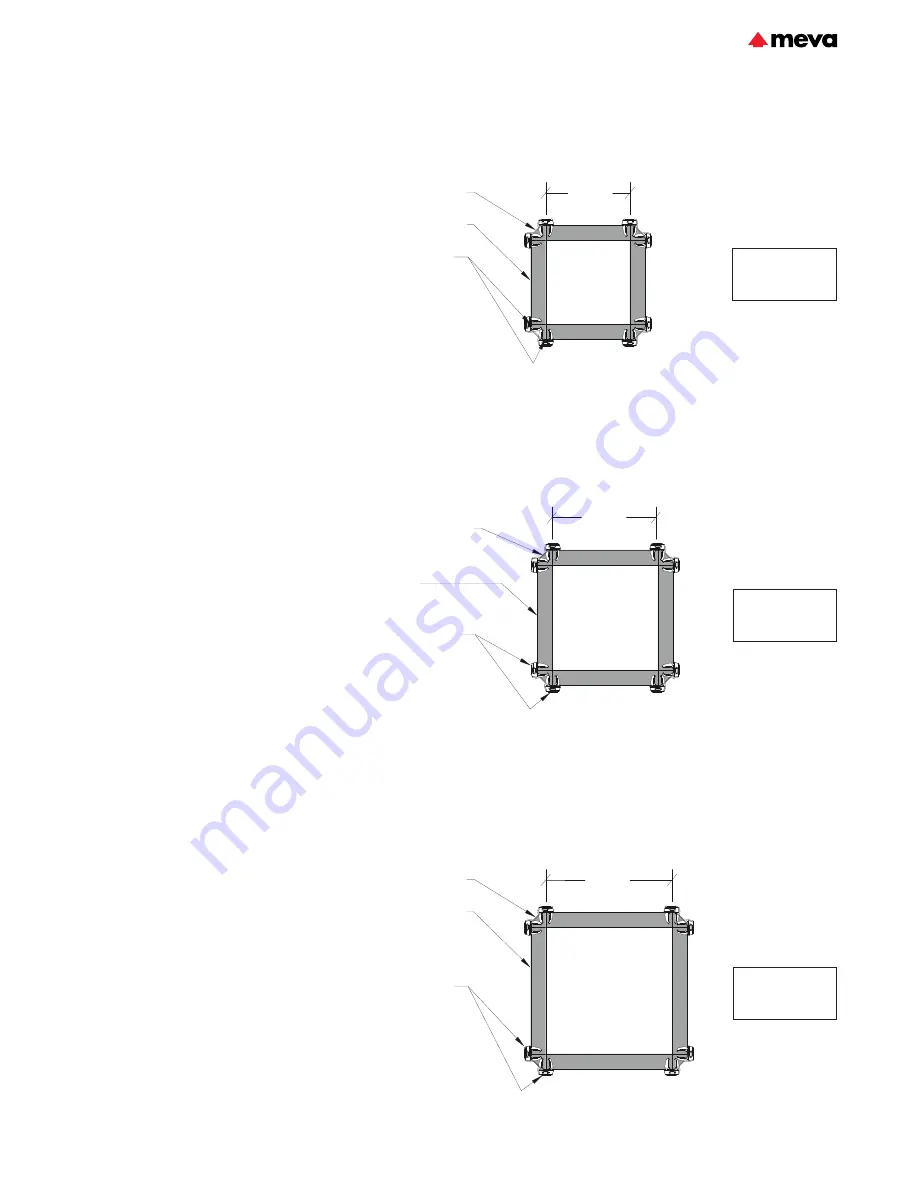
MevaLite
ML-29
Columns
Columns with Standard Panels
and Outside Corners:
Columns can also be formed
using standard panels and outside
corners. To form columns with
sizes in between the MevaLite
panel widths, the next largest
panel size is used and the forms
are furred out on the inside.
Columns can only be formed with
panels oriented vertically (panel
cross members horizontal).
The outside corner connections
require more assembly locks than
standard panel connections. The
connection requirements and
maximum allowable concrete
pressure depend on the column
size (with rectangular columns
the longer side controls) - see
Figures 29.1 - 29.3.
*For columns > 30" to ≤ 36"
1350 psf may be achieved with the
addition of reinforcing rails.
Refer to MEVA engineering for
guidance.
Fig. 29.1 Column sizes up to 24"
Locks required at
outside corner joints:
9' panel - 7 locks
6' panel - 5 locks
4' panel - 4 locks
3' panel - 3 locks
≤ 24"
≤ 30"
Outside corner, typ.
MevaLite panel, typ.
Outside corner, typ.
MevaLite
multi-purpose panel, typ.
Locks required at
outside corner joints:
9' panel - 8 locks
6' panel - 6 locks
4' panel - 4 locks
3' panel - 3 locks
Fig. 29.2 Column sizes up to 30"
Maximum allowable
concrete pressure =
1350 psf.
Maximum allowable
concrete pressure =
1350 psf.
Fig. 29.3 Column sizes up to 36"
Locks required at
outside corner joints:
9' panel - 8 locks
6' panel - 6 locks
4' panel - 4 locks
3' panel - 3 locks
≤ 36"
Outside corner, typ.
MevaLite panel, typ.
Maximum allowable
concrete pressure =
1100 psf. *
MPP
MPP
MPP
MPP
Wall formwork
Technical Instruction Manual / June 2022
Summary of Contents for MevaLite
Page 1: ...Technical Instruction Manual June 2022 MevaLite...
Page 57: ...Notes...
Page 58: ...Notes...
Page 87: ...Notes...