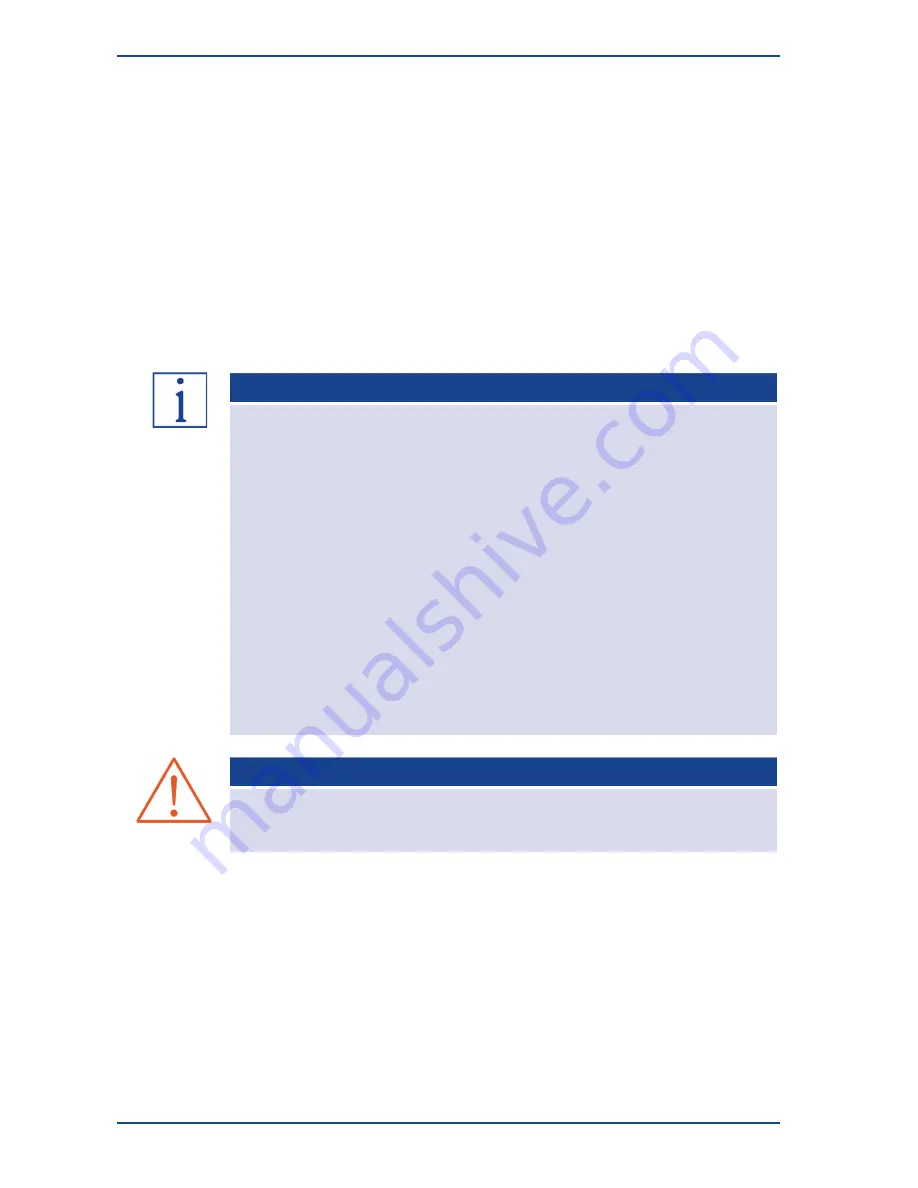
Page 6
Safety notes for electrical drives and controllers
Mounting Instructions „Servo drives BL 4000-C“
PRELIMINARY
Version 0.1
TRAINED AND QUALIFIED PERSONNEL
in the sense of this product manual or the safety notes on the product itself are persons who are
sufficiently familiar with the project, the setup, assembly, commissioning and operation of the product as
well as all warnings and precautions as per the instructions in this manual and who are sufficiently
qualified in their field of expertise:
Education and instruction concerning the standards and accident prevention regulations for the
application, or authorisation to switch devices/systems on and off and to ground them as per the
standards of safety engineering and to efficiently label them as per the job demands.
Education and instruction as per the standards of safety engineering regarding the maintenance and
use of adequate safety equipment.
First aid training.
The following notes must be read prior to the initial operation of the system to prevent personal injuries
and/or property damages:
INFORMATION
These safety notes must be complied with at all times.
Do not try to install or commission the servo drive before carefully reading all
safety notes for electrical drives and controllers contained in this document.
These safety instructions and all other user notes must be read prior to any work
with the servo drive.
In case you do not have any user notes for the servo drive, please contact your
sales representative. Immediately demand these documents to be sent to the
person responsible for the safe operation of the servo drive.
If you sell, rent and/or otherwise make this device available to others, these
safety notes must also be included.
The user must not open the servo drive for safety and warranty reasons.
Professional control process design is a prerequisite for sound functioning of the
servo drive!
DANGER!
Inappropriate handling of the servo drive and non-compliance with the warnings as
well as inappropriate intervention in the safety features may result in property
damage, personal injuries, electric shock or in extreme cases even death.